Off-site construction is becoming a popular alternative to traditional building methods, offering solutions to the inefficiencies of on-site projects. With its ability to reduce timelines, lower costs, and improve safety, off-site building is changing how we approach building. Knowing the key advantages of panelized, modular, or component construction helps stakeholders make informed decisions about project planning and execution.
Quick look
- Traditional on-site construction faces challenges like lengthy build times, high labor costs, and material waste, which affect project efficiency and budgets.
- Off-site building involves manufacturing components in a factory setting and transporting them to the construction site for assembly.
- Key types of off-site construction include volumetric modular, panelized, hybrid modular, and component-based methods, each suited to different project needs.
- Off-site construction enhances worker safety, boosts productivity, reduces costs, and allows for faster project completion, reducing timelines by up to 50%.
The problem with on-site construction
Traditional on-site construction is facing serious challenges. Building on-site means starting from scratch, with every part of the structure created on the site itself. Here are some of the top problems faced by traditional on-site construction:
- Lengthy build times and schedule disruptions: Factors like weather, logistical issues, and urban noise restrictions often delay on-site construction projects. These disruptions can slow down timelines, making it difficult to stay within budgets and timelines.
- Material waste: Traditional construction sites produce excess waste, with materials often cut or prepared inefficiently. This waste affects budgets and increases the environmental footprint.
- Labor costs and shortages: On-site construction is labor-intensive, requiring a skilled workforce that’s becoming increasingly hard to find. Rising wages and the demand for skilled workers make these projects more costly.
- Health and safety risks: Construction sites come with safety hazards, such as falls, equipment accidents, and exposure to harsh weather. Off-site construction in a controlled factory setting helps significantly reduce these risks, improving worker health and safety.
- Environmental impact: The traditional construction approach is resource-heavy, consuming large amounts of energy and creating pollution. Off-site methods allow builders to reduce their carbon footprint, making the process more sustainable.
The basics of modular and prefab construction
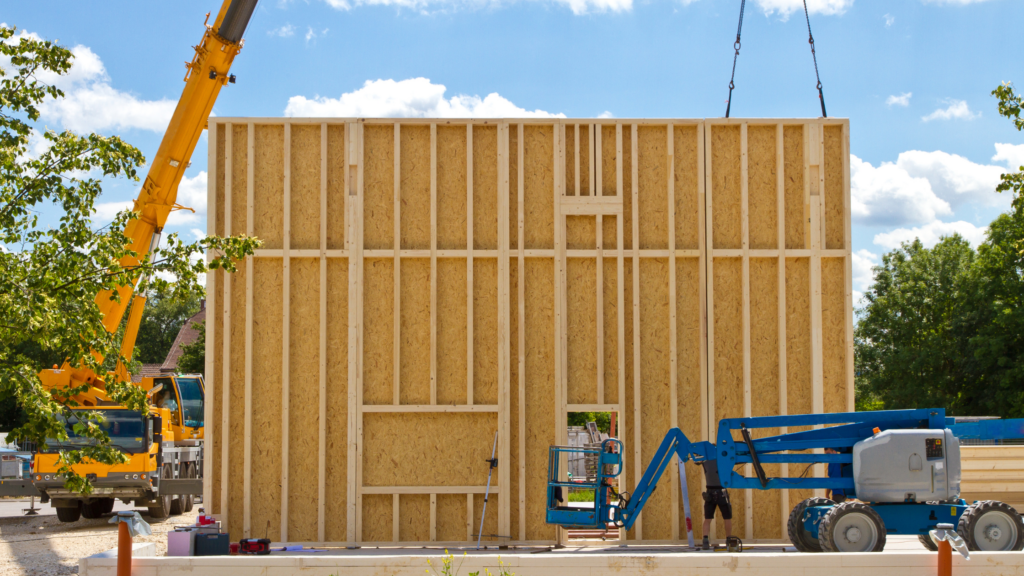
Off-site construction, including modular and prefabricated building methods, involves manufacturing building components in a factory setting and transporting them to the construction site for assembly. This approach differs from traditional construction, where each part of the structure is built directly on-site. Instead, modular and prefab methods allow for key elements—such as walls, floors, and entire rooms—to be made with precision off-site before being assembled on location.
Types of off-site construction
Off-site building isn’t a one-size-fits-all approach. There are several types, each with its unique benefits and applications. By understanding the distinctions, developers and contractors can choose the best method for their project needs.
1. Volumetric modular construction
Volumetric modular construction involves creating three-dimensional modules in a factory. Often fully or partially finished, these modules are transported to the site for assembly. This approach is commonly used in residential buildings, hotels, schools, and healthcare facilities. Volumetric construction allows site work and module production to co-occur, which helps speed up project timelines and reduce labor costs on-site.
2. Panelized construction
Panelized construction is another form of off-site building where flat panels, such as walls, floors, and roofs, are manufactured off-site and then assembled on-site. Panels can be made from wood, steel, or concrete, making this approach highly versatile. Panelized construction is suitable for residential homes, apartment buildings, commercial spaces, and schools, offering flexibility in design and reducing on-site construction time.
3. Hybrid modular construction
Hybrid modular construction combines both volumetric and panelized methods, using each approach where most effective. This method is ideal for complex projects, such as hospitals or multi-family housing, where design flexibility and efficiency are essential. By leveraging volumetric and panelized construction, hybrid modular construction maximizes efficiency and allows for more complex, customized designs.
4. Component (sub-assembly) construction
Component (sub-assembly) construction focuses on creating specific building components, like stairs, bathroom pods, or mechanical systems, in a factory setting. These components are then integrated into the main structure on-site. This approach improves quality control and reduces on-site installation time, making it a popular choice for residential, commercial, and industrial projects that require precise, high-quality components.
The benefits of integrating more off-site construction
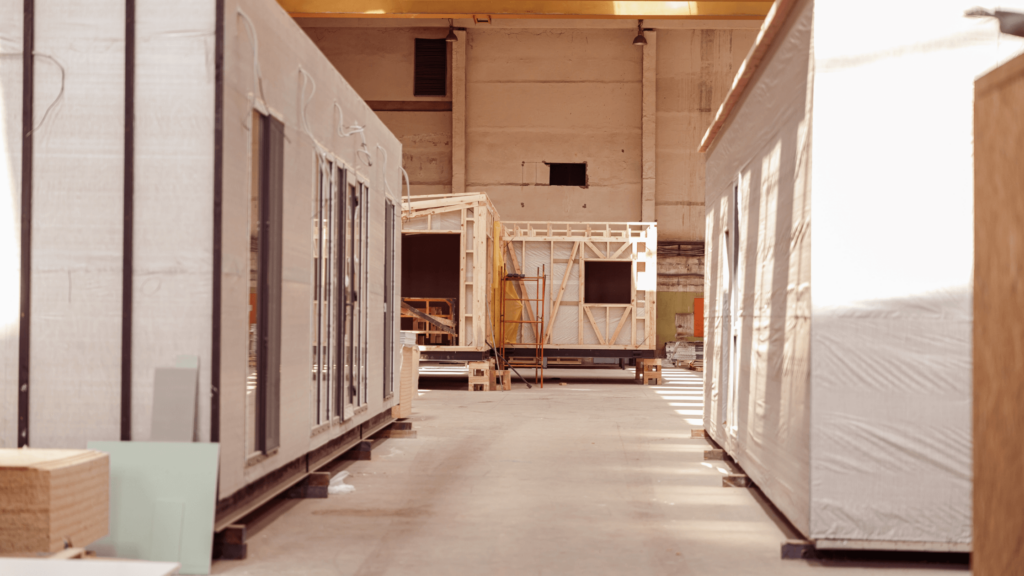
Integrating off-site construction methods comes with a wide range of benefits that can improve project outcomes across the board. Here are some of the biggest advantages:
Worker health and safety
By moving much of the construction process to a factory setting, off-site building reduces the risks workers face on traditional sites. Factory environments are more controlled, with fewer hazards like heights and heavy machinery, lowering the risks of accidents and injuries.
Productivity
Off-site construction allows for simultaneous work to happen in the factory and on-site, leading to faster project completion. Since factory operations are minimally impacted by factors like weather, they can maintain steady productivity levels, keeping projects on schedule and reducing downtime. This can reduce project timelines by 30% to 50%.
Cost savings
Off-site construction can significantly reduce costs by streamlining production and minimizing on-site labor. There’s less need for extensive on-site crews, and the efficient use of materials in a factory setting helps keep budgets under control.
Reduced materials waste
Factories allow for more precise material use, which means less waste overall. This efficiency reduces environmental impact and helps save on material costs, making off-site construction a more sustainable option.
Faster completion timelines
Projects can move forward more quickly with much of the building done off-site. Off-site building speeds up timelines by allowing site preparation and manufacturing to occur simultaneously.
Enhanced environmental sustainability
Off-site construction methods are generally more eco-friendly, producing less waste and consuming less energy than traditional methods. The controlled factory setting enables efficient use of materials and reduces the need for heavy on-site equipment, ultimately resulting in a smaller carbon footprint.
Improved quality control
Quality checks can be built into each production stage in a factory, ensuring consistency and high standards. This controlled environment reduces errors and rework, providing a better-quality end product for each project.
Reduced site disruption
Since much of the work is done off-site, there’s less noise, dust, and general disruption at the construction site. This is especially beneficial in urban or densely populated areas where minimizing noise is helpful for surrounding residents and businesses.
Bottom line
Off-site building offers a modern solution to many of the challenges traditional building methods face. By moving parts of the process to a controlled factory environment, projects can be completed faster, safer, and more sustainable. This approach reduces costs, enhances quality, and minimizes site disruption, making it an appealing choice for developers and contractors. As demand for efficient, reliable construction grows, off-site methods will likely play an even more prominent role in the industry’s future.
Want to learn more about how off-site construction can improve your next project? Subscribe to our weekly newsletter for expert insights, practical tips, and the latest updates on modular and prefab building innovations.