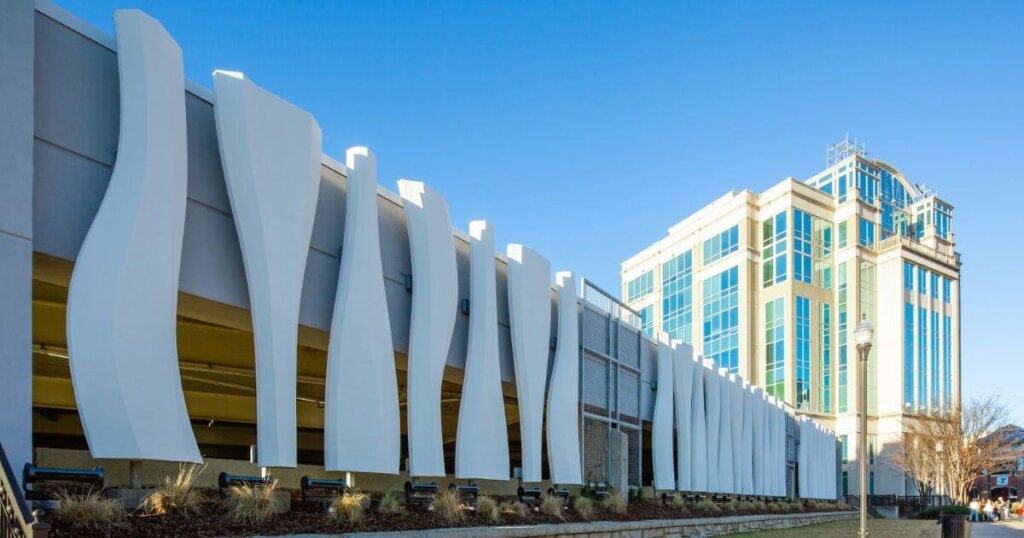
The future of construction is shifting toward smarter, more innovative methods that push the boundaries of design and sustainability. One company leading this transformation is Branch Technology, a Tennessee-based innovator using freeform 3D printing and robotic fabrication to revolutionize building. Their proprietary Composite Core™ construction method enables the creation of lightweight, structurally sound, and highly customized architectural elements, offering a new frontier for architects, engineers, and contractors alike.
What is Branch Technology?
Branch Technology blends additive manufacturing, computational design, and advanced materials to deliver complex, large-scale construction solutions. Their approach moves beyond traditional 3D printing by incorporating cellular fabrication (C-Fab®), an entirely new way of building that reduces material waste while allowing for unprecedented design flexibility.
Their process prints open-cell structures using industrial robotic arms and reinforces them with traditional construction materials like concrete and insulation. This method allows designs of any form to be fabricated at construction scale, achieving an unmatched strength-to-weight ratio while using 20 times less material and requiring five times less production time.
What does Branch Technology offer?
Branch Technology works closely with architects, engineers, and general contractors to bring complex visions to life, offering solutions that enhance aesthetics and performance. The company provides custom façade systems, large-scale 3D-printed architectural features, and structural wall panels. Some of their standout projects include:
- The world’s first freeform 3D-printed building façade
- Lightweight, thermally efficient architectural panels
- Sculptural interior and exterior elements that push design innovation
Why it matters
Traditional construction methods often limit architectural creativity while producing significant material waste. Branch Technology’s process solves both problems by enabling the following:
- Greater design freedom without compromising structural integrity
- Lighter, more efficient building components that reduce labor and installation time
- Sustainability improvements through waste reduction and energy-efficient materials
Combining 3D printing with prefab building democratizes construction by reducing project timelines, material waste, and unrestricted design freedom. “From an installation perspective, it cuts schedules by up to 80 percent,” said Platt Boyd, founder and CEO at Branch Technology. “Traditional exterior envelope projects can take up to six months. With 3D printing and prefabrication, you are looking at a month. In fact, that’s why the hospitality industry is beginning to rapidly embrace and adopt the technology. There are very, very tangible benefits to schedule acceleration.”
As the AEC industry seeks smarter, greener, and more adaptable building solutions, companies are proving that automation, 3D printing, and computational design can create a more efficient and sustainable future for construction. With an ever-growing portfolio of innovative projects, Branch Technology is setting a new standard for how buildings are designed and built—one freeform print at a time.
Want to stay updated on the latest innovations in AEC technology? Subscribe to our newsletter and follow us on social media for insights, industry trends, and expert perspectives!