Construction costs can quickly spiral out of control without the right strategies, but that doesn’t mean quality has to suffer. Prefabricated construction, supplier partnerships, and the latest technology are just a few ways to save money while maintaining high standards. From smarter planning to better collaboration, there are many ways to control expenses and keep projects on track.
Quick look
- Effective cost management boosts your bottom line, allowing you to reinvest in tools, skilled labor, and business growth.
- A lean budget provides flexibility to adapt to economic fluctuations and unforeseen challenges.
- Prefabricated components save time, reduce waste, and cut labor costs while maintaining high standards.
- Early collaboration and efficient layouts help control expenses without sacrificing functionality.
- Proper training, lean practices, and organized workflows minimize downtime and labor costs.
Why cost reduction matters in construction
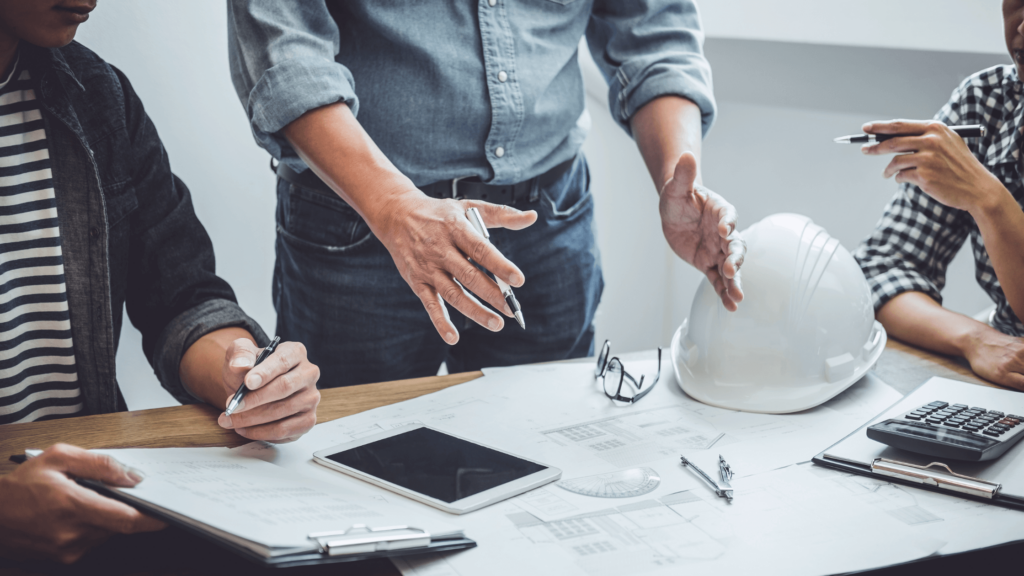
Profitability
Lowering expenses has a direct and significant impact on a construction company’s bottom line, ensuring projects remain financially viable. When budgets are optimized, the savings can be reinvested into growth opportunities, such as purchasing advanced tools, expanding services, or hiring skilled workers. Companies that consistently meet or beat their budget goals develop a strong financial foundation that promotes long-term sustainability.
Effective cost management builds resilience, helping firms weather market fluctuations and unforeseen challenges. This focus on profitability attracts new projects and reinforces trust with stakeholders.
Project success
Managing costs effectively ensures projects are completed within their original scope and on time, which are key indicators of success. Allocating resources strategically helps prevent unnecessary spending while ensuring critical aspects of the build receive proper attention. When costs are controlled, there’s less risk of mid-project disruptions, such as material shortages or financial overruns. Consistent budgeting allows teams to focus on execution, fostering a seamless workflow that supports timely completion. Ultimately, cost control enables all stakeholders to deliver a project that meets or exceeds expectations.
Client satisfaction
Clients value transparency and efficiency, especially when it comes to budgeting. When companies consistently deliver projects within the agreed-upon budget, it builds trust and strengthens relationships. By minimizing unexpected costs and delivering value for every dollar spent, construction teams create positive client experiences that lead to repeat business. Clear communication about cost-saving measures also helps clients feel involved and reassured about the project’s financial health. Happy clients are more likely to refer your services, enhancing your reputation and generating new opportunities.
Competitive advantage
Effective cost reduction provides a critical edge in an industry where margins can be tight. Offering competitive pricing without sacrificing quality attracts clients who are budget-conscious yet demand high standards. Companies that manage budgets well often gain a reputation as reliable and efficient, making them the go-to choice for large projects. This competitive advantage wins more contracts and builds a loyal client base that sustains the business during slower periods. Staying ahead in cost management creates a strong differentiator in the crowded construction market.
Sustainable practices
Reducing construction costs often goes hand in hand with adopting sustainable practices, creating benefits for both the environment and the bottom line. For example, reusing materials or integrating energy-efficient designs lowers material and operational expenses.
Sustainable initiatives like waste reduction and renewable energy sources also appeal to clients looking to minimize their environmental footprint. Over time, eco-friendly construction practices can lead to long-term savings through reduced energy bills and maintenance costs. Balancing cost reduction with environmental responsibility boosts financial performance and aligns with modern client expectations.
8 methods to reduce construction costs without sacrificing quality
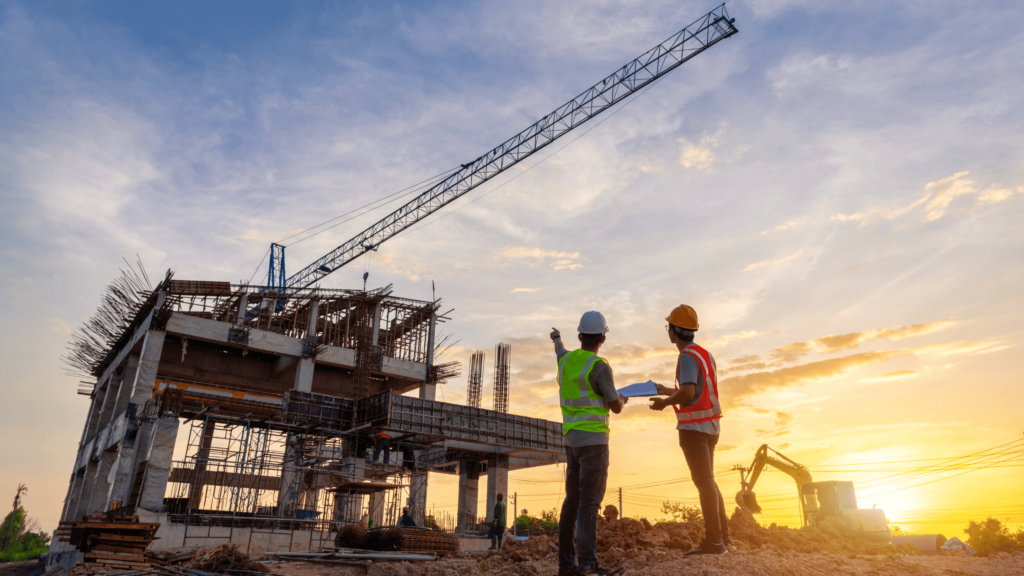
1. Prefabricated/modular construction
Prefabricated construction, where components are manufactured off-site and assembled on-site, has revolutionized cost-conscious building projects. This approach reduces waste by using precise manufacturing processes in controlled environments, reducing excess materials. It also lowers labor costs, as the streamlined assembly process requires fewer workers on-site.
Another advantage is faster timelines, with projects often completed in a fraction of the usual time, saving on financing and overhead. Quality is consistently higher due to factory conditions ensuring uniform standards, which minimizes defects. Additionally, modular builds frequently incorporate eco-friendly materials, contributing to reduced environmental impact while maintaining excellent design and functionality.
These advantages make prefab construction an attractive solution for projects of all sizes, offering financial and logistical benefits without compromising quality.
2. Technology integration
Technology is reshaping the construction industry by streamlining workflows and minimizing costly mistakes. Estimating software plays a crucial role in generating accurate project bids, ensuring realistic budgets, and reducing the risks of financial miscalculations. Real-time budgeting tools help track expenses as they occur, preventing overruns and keeping projects on track financially.
Building Information Modeling (BIM) fosters collaboration by producing detailed 3D models that identify potential issues before construction begins, reducing delays and rework. Drones enhance site inspections and monitor progress efficiently, saving time and reducing reliance on on-site labor. Additionally, project management software centralizes scheduling, communication, and budget tracking, improving coordination across teams and ensuring smoother project execution.
Integrating these tools minimizes errors, improves efficiency, and delivers substantial cost savings throughout construction.
3. Accurate billing
Accurate billing is a crucial but often overlooked aspect of construction cost management. Ensuring clear and detailed invoices reduces disputes, which can delay payments and disrupt cash flow. Advanced billing software can automate the process, minimizing human error and saving time. Clients who understand every charge are less likely to question or delay payments.
Accurate billing also supports better project tracking, as financial discrepancies can be quickly identified and addressed. Over time, this practice builds client trust and enhances the company’s financial stability.
4. Supplier collaboration
Strong relationships with suppliers can yield significant cost benefits. Partnering with local suppliers helps cut transportation costs and ensures timely materials delivery, reducing downtime. Long-term contracts with trusted suppliers often result in bulk discounts and priority access during shortages.
Open communication allows companies to negotiate better prices while ensuring the quality of materials remains high. Collaborative planning with suppliers can also lead to innovative solutions, such as recommending alternative materials that meet project needs at a lower cost. These partnerships are vital for keeping budgets under control while maintaining project standards.
5. Planning and design optimization
Efficient planning and thoughtful design are essential for minimizing costs without affecting quality. Value engineering, which evaluates cost-effective alternatives for every aspect of a project, ensures maximum functionality at minimal expense. Early collaboration between designers, engineers, and contractors identifies potential challenges and cost-saving opportunities before construction begins.
Using standardized components simplifies construction and reduces manufacturing time, further controlling costs. Designing for efficiency, such as incorporating simple layouts and prioritizing energy efficiency, creates long-term savings while meeting project goals. Careful planning ensures that every dollar spent delivers value.
6. Streamlined project management
Efficient project management plays a pivotal role in controlling costs by eliminating inefficiencies. Regularly tracking progress against the budget ensures timely adjustments, preventing overruns. Using software to centralize workflows and schedules keeps teams on the same page, reducing misunderstandings and redundant work.
Clear communication ensures everyone understands their roles and responsibilities, avoiding costly delays. Strong leadership ensures that resources are allocated effectively, maximizing productivity. A well-managed project not only stays within budget but also delivers higher-quality results.
7. Material substitutions
Exploring alternative materials can significantly reduce costs while maintaining durability and aesthetics. For instance, using engineered wood instead of traditional hardwood can lower expenses without compromising structural integrity. Advances in materials science have also introduced cost-effective, high-performance options such as lightweight concrete or recycled steel.
Consulting with architects and suppliers ensures material substitutions align with project specifications and safety standards. Smart material choices can reduce initial costs and create opportunities for long-term savings in maintenance and repairs.
8. On-site efficiency
Maximizing on-site efficiency directly impacts labor costs and project timelines. Proper training ensures workers can perform tasks efficiently and safely. Implementing lean construction principles, which prioritize reducing waste and optimizing workflows, improves overall productivity.
Organizing tools, materials, and equipment ensures they are readily available when needed, reducing downtime. Investing in modern equipment can also speed up processes and minimize labor hours. An efficient construction site is critical to staying on budget and delivering quality results.
Bottom line
Cutting costs doesn’t mean cutting corners. By adopting strategies like prefabrication, smart material choices, and strong supplier relationships, construction companies can deliver exceptional results while staying within budget. Combining technology with thoughtful planning ensures projects are efficient and cost-effective.
Stay ahead in the construction industry—subscribe to our newsletter at Under the Hard Hat for more insights and tips to manage construction projects effectively.