Design for Disassembly (DfD) is a philosophy centered around the idea that buildings should be designed and constructed with future disassembly and reuse of materials in mind. DfD is emerging as an intriguing solution to the pollution, waste, and environmental degradation caused by the construction industry, and it can reduce material costs, too. Some notable projects embodying the principles of DfD are the NASA Sustainability Base and The Circular Building.
Quick look:
- The construction industry accounts for 30% of natural resource extraction and up to 40% of solid waste globally.
- Some studies show that 57% of building demolitions are due to area redevelopment or because the buildings were no longer suitable for their anticipated use, not deficits in the buildings themselves.
- Design for Disassembly can result in 65% of building materials being reused.
- Notable projects following the principles of Design for Disassembly include the NASA Sustainability Base and the ICEhouse.
Construction: A wasteful industry
Construction is responsible for over 30% of natural resource extraction, and waste from construction, demolition, and renovation accounts for between 30 and 40% of globally-generated solid waste.
The constant need to build, renovate, demolish, and rebuild creates a cycle of extraction and waste that’s devastating for the environment and our health. Hazardous materials like asbestos, lead, mercury, polychlorinated biphenyls (PCB), chlorofluorocarbons, and radioactive sources are present in buildings of all ages and can cause devastating impacts on the health of those who build, inhabit, and eventually demolish the structures.
Design for Disassembly
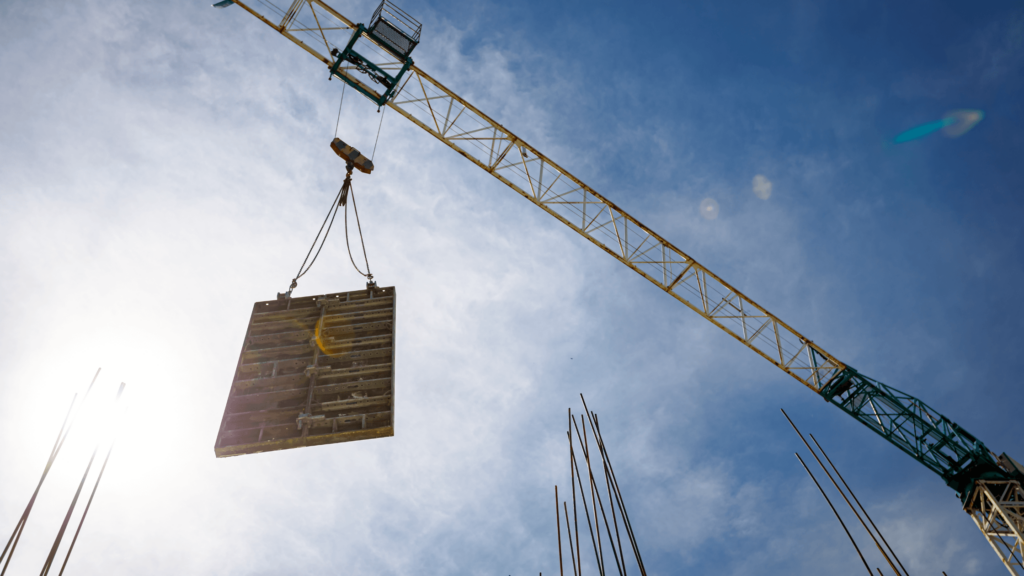
According to one American case study, 57% of building demolitions occurred due to “area redevelopment” and because they were “not suitable for anticipated use” rather than issues with the building’s structural integrity. As a result, millions of tons of construction material are sent to landfills after the demolition and destruction of perfectly usable structures.
Design for Disassembly seeks to address the issue of waste in the construction industry by creating buildings with their eventual disassembly in mind. DfD focuses on choosing simple designs, durable materials, easily removed connection points, and simple construction that’s equally easy to take apart. Constructing a building with these principles ensures that most components can be removed and reused, reducing waste, lessening the burden on natural resources, and limiting or eliminating hazardous materials.
Key benefits of Design for Disassembly
Beyond being a nice idea, DfD has several concrete benefits that may make it an attractive option for developers.
Environmental impact
Buildings constructed with a DfD philosophy can be easily deconstructed, and most materials used in the building can be repurposed, reducing the amount of solid waste generated.
A 2023 case study of a building constructed with DfD principles states that it has a Global Warming Potential “26% below baseline industry target values for the product and construction stage, operates using less energy than targets for education and office buildings, and has been designed to enable the reuse of 65%, by mass, of the substructure and superstructure at end-of-life.”
Another study showed that designing a steel building to be disassembled can save 80% of the greenhouse gases compared to melting the steel down for recycling and 70% of the energy.
Cost savings
Over 80% of construction materials have increased in price since 2020, with an average cost increase of 19%. Design for Disassembly may help lower these rising construction costs by reducing the need for new materials, providing a potential revenue stream for the sale of materials after disassembly, and lowering disposal fees for waste materials.
Flexibility
When you use the principles of DfD to design a project, you also provide greater flexibility before the building is disassembled. Buildings created to be eventually taken apart and reused allow users to adapt the building to evolving technologies, easily swap out elements and features, and even shift the way the building functions to reflect changing needs. This offers greater flexibility in design features, making a space more functional and user-friendly during its lifespan.
DfD also focuses on designing buildings with more adaptable and modular elements for future use, meaning that materials can be reused and repurposed almost indefinitely.
Economic viability
To make new construction economically viable, it’s crucial to embrace innovative approaches in building design, construction, and demolition. Utilizing DfD can mean the difference between coming in on budget or risking costly overruns.
Recovered components of disassembled buildings can be repurposed, reused, or sold to other projects, offsetting construction costs and contributing to the circular economy.
10 principles of DfD
Design for Disassembly is guided by 10 fundamental principles, which provide instructions for implementing this concept in architectural, engineering, and construction (AEC) environments.
- Document materials and methods for deconstruction: It’s challenging to disassemble a building and reuse the materials when you don’t know what they are or how to take them apart safely and effectively. Documenting a project “as-built” provides a roadmap for its eventual destruction and reuse.
- Select materials using the precautionary principle: The precautionary principle states that you should avoid using a new product or process if there is scientific uncertainty about its effects or if it is likely to cause harm. Applying this principle to design means, wherever possible, choosing materials that have stood the test of time and have the highest chance of being successfully disassembled and reused.
- Design connections that are accessible: Making connection points between structures and materials visible and accessible means simpler disassembly, which is less likely to require complex equipment or safety precautions.
- Minimize or eliminate chemical connections: Many materials become unsuitable for reuse when attached together with chemical connections, such as glue and sealants.
- Use bolted, screwed, or nailed connections: Choosing mechanical connections like nails or screws increases the likelihood that building materials can be repurposed.
- Separate mechanical, electrical, and plumbing (MEP) systems: Keeping MEP systems separate and unintegrated makes it easier to reuse materials.
- Design to the worker and labor of separation: Constructing a building from human-scale materials and using commonly available mechanical equipment means that removal and disassembly will be simpler and more accessible to workers of all skill levels—no need for heavy machinery or specialized tools.
- Simplicity of structure and form: DfD calls for standard dimensional grids and open-span structural systems to keep construction simple and facilitate the repurposing of materials from one building to the next.
- Interchangeability: Likewise, materials that are independent, standardized, and modular will be more easily reused and rebuilt into other structures.
- Safe deconstruction: Making connection points accessible, materials safe, non-hazardous, and easily disassembled means deconstructing a structure that will be safe for workers.
Design for Disassembly in architecture
Several projects have used Design for Disassembly principles in their construction.
NASA Sustainability Base
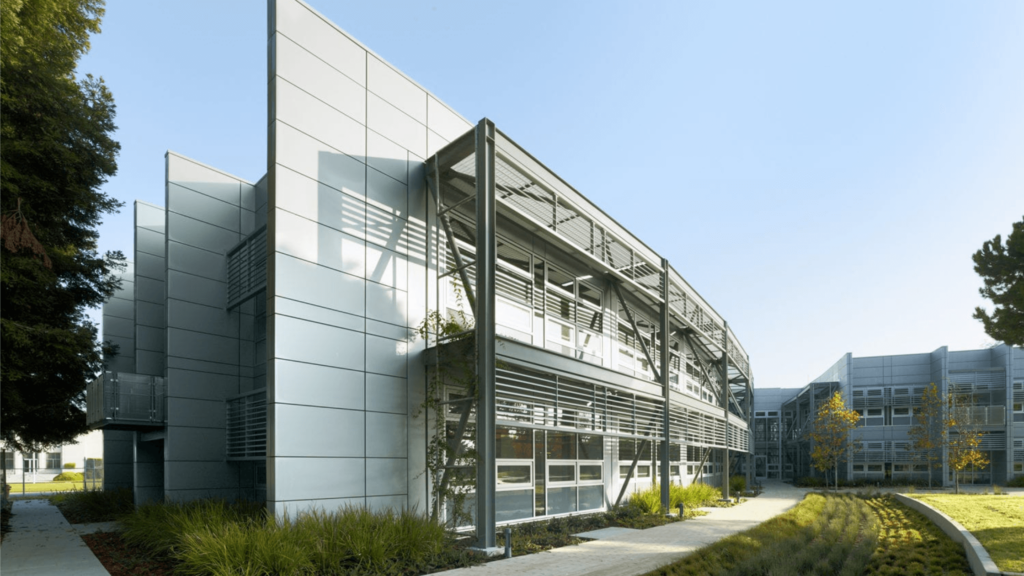
Designed by William McDonough + Partners, the NASA Sustainability Base in Moffett Field, California, has earned LEED® Platinum certification for features like solar panels, greywater systems, passive heating, and its focus on DfD principles.
Most materials used in the building’s construction were salvaged, reused, recycled, or rapidly renewable, and they were selected for their benefits to human health and environmental well-being.
The Circular Building
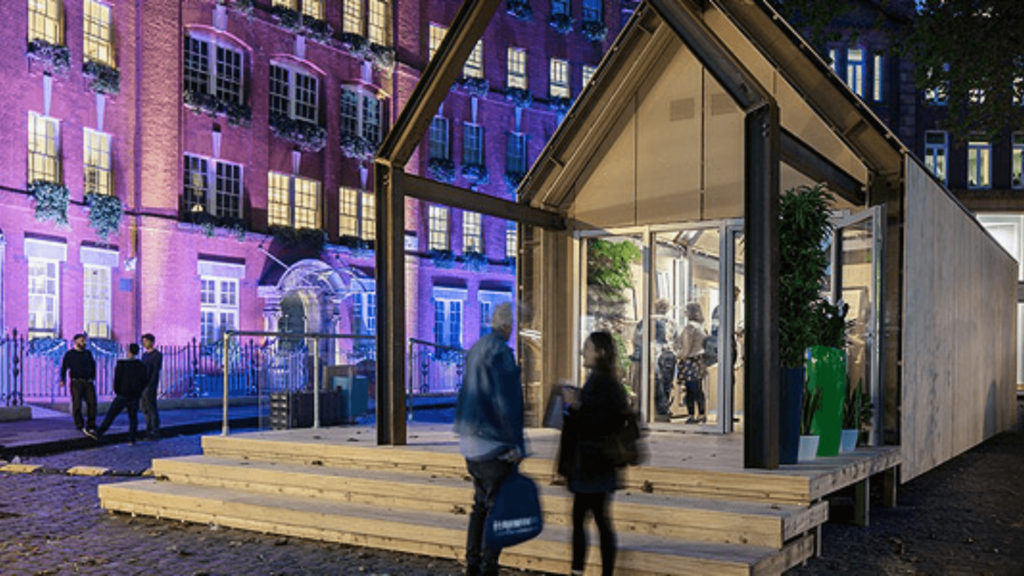
For the 2016 London Design Festival, Arup Associates created The Circular Building. This prototype structure was the first to satisfy the Circular Economy principle: “All components need to be implemented and utilized to their full potential and to the duration of their life cycle while creating a comfortable and aesthetic environment for the user.” The building also embodied DfD principles in its construction, which easily enabled its materials to be disassembled and reused.
ICEhouse
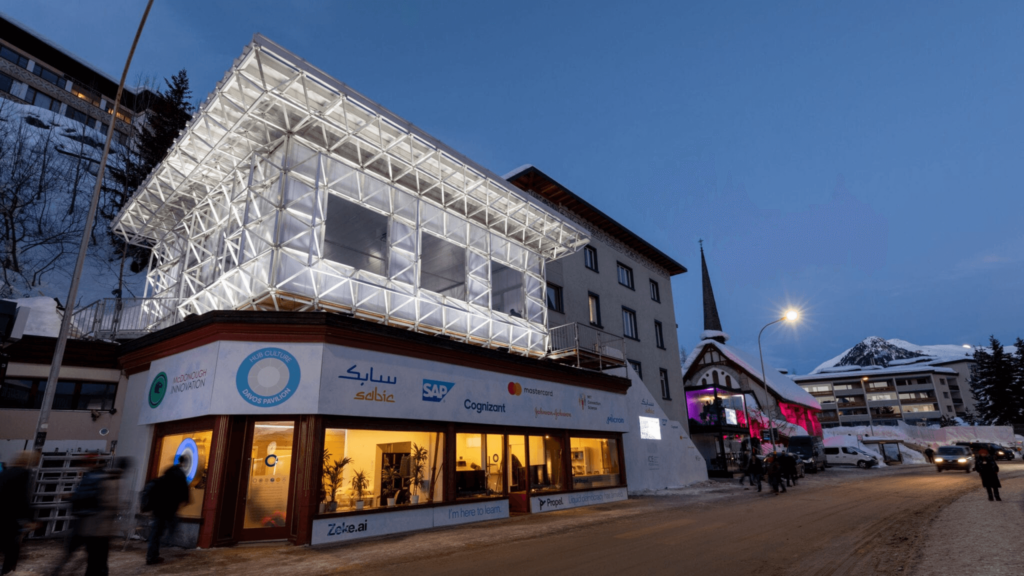
The ICEhouse (Innovation for the Circular Economy) is another project by William McDonough + Partners. This building is not only Designed for Disassembly; it’s already been disassembled and reassembled once. First built in Davos, Switzerland, it was later taken apart and reassembled in the Netherlands.
The ICEhouse is constructed with three primary materials: aluminum (for the frame),
Polymers (for the walls, roof, carpet, and light fixtures) and aerogel (for the insulation). All materials are Cradle to Cradle Certified and can be endlessly recycled or reused without degradation in quality.
Bottom line
Reducing construction’s impact on the environment and the economy requires shifting our approach to designing, building, and demolishing structures. Choosing reused or reusable materials, durability over convenience, and disassembly over demolition can provide a big payoff for the economy and the environment.
For more of the latest architecture, design, and construction innovations, subscribe to our newsletter!