The construction industry is rapidly evolving, with new technologies revolutionizing project design, management, and execution. While younger workers often quickly embrace these advancements, older generations can find the shift more challenging, creating a gap that impacts efficiency and teamwork. By fostering collaboration and providing the proper support, construction companies can empower workers of all ages to adopt and benefit from innovative tools.
Quick look:
- Construction is lagging behind other industries in tech adoption, specifically where older generations are concerned.
- Generational differences create challenges in implementing new tools.
- Gen Z workers adapt quickly to technology, while older workers may face barriers.
- Reverse mentoring and collaborative training are effective strategies to ease the transition to technology integration.
The hesitancy with technology
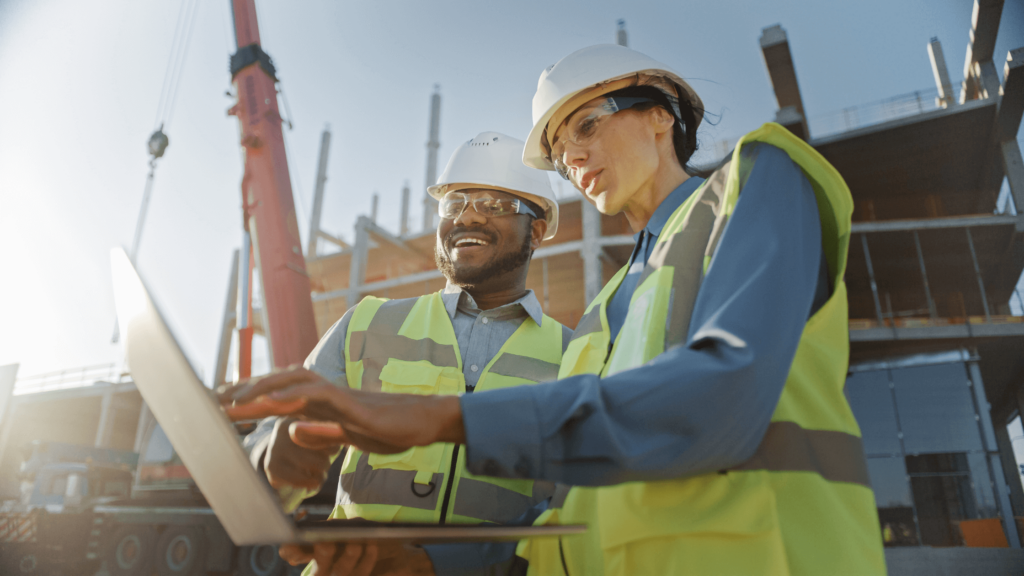
Adopting new technology in the construction industry often involves hurdles. One of the most significant barriers is cost. Advanced tools and systems can require substantial upfront investments, making it hard for companies to justify the expense without guaranteed returns. Beyond the financial aspect, training requirements also play a key role in slowing adoption. Learning new tools can be time-intensive, taking workers away from their daily responsibilities, which adds to the hesitation.
For older workers, age-related challenges can compound these issues. Navigating unfamiliar interfaces or adjusting to new workflows may feel intimidating, especially for those who’ve spent decades mastering traditional methods. Additionally, there’s often a lack of trust in technology, with skepticism about whether these tools will deliver the promised improvements or simply complicate established processes.
Lastly, the industry’s strong roots in tradition can hold back innovation. Construction professionals often rely on methods and tools that have “always worked,” making them reluctant to change. While these hesitations are understandable, they highlight the need for strategies to bridge technology and workforce generation gaps to make technology adoption more accessible for everyone.
Gen Z: A tech-driven generation
Gen Z, born into the digital age, has grown up surrounded by smartphones, apps, and instant access to information. This generation’s innate comfort with technology isn’t just a product of convenience; it’s a way of life. For Gen Z workers entering the skilled trades, adapting to tech-based tools like digital blueprints, project management software, or augmented reality (AR) solutions is second nature.
This tech fluency presents a unique opportunity for the construction industry. Gen Z’s ease with digital solutions can help accelerate the adoption of innovative tools across the workforce. By leveraging this expertise, companies can foster a collaborative environment where older workers gain hands-on support in integrating new technology. Programs like reverse mentoring, where younger employees teach older colleagues, can bridge generational gaps, empowering the entire workforce to work smarter, not harder.
5 ways to encourage tech adoption in construction
1. Reverse mentoring
One of the most effective ways to bridge the technology gap in construction is through reverse mentoring, where younger workers help older colleagues learn and adopt new tools. This approach leverages the tech-savvy nature of younger generations, like Gen Z, to provide hands-on guidance in using software, mobile apps, or advanced machinery.
The concept of reverse mentoring was introduced in 1999 by former General Electric CEO Jack Welch, who encouraged 500 senior staff members to meet with younger recruits to learn about the technology they were using. This initiative gave senior staff valuable insights into emerging tech while offering new hires direct access to leadership, fostering communication and collaboration across hierarchical lines.
Reverse mentoring doesn’t just teach technical skills; it fosters collaboration and mutual respect between age groups. Older workers bring their years of expertise and industry knowledge, while younger employees contribute their familiarity with modern technology. Together, they create a more inclusive and productive work environment.
For example, companies like Skanska, Mott MacDonald, and Balfour Beatty have successfully implemented reverse mentoring programs. These programs pair seasoned employees with younger, tech-savvy colleagues to ensure smooth transitions to digital workflows. By encouraging knowledge sharing across generations, these programs improve technology adoption and strengthen team dynamics.
2. Collaborative training
Cross-generational training sessions offer a powerful way to build confidence and skills across the workforce and foster a collective approach to technology adoption. These sessions bring younger, tech-savvy employees and older, more experienced workers together in a collaborative learning environment where everyone benefits from each other’s strengths.
The key to successful collaborative training is a focus on practical, hands-on learning. For older workers, theory-heavy sessions can feel overwhelming or detached from their day-to-day tasks. Instead, providing opportunities to engage directly with new tools—whether learning to operate advanced machinery or navigating project management software—can help demystify the technology and make it less intimidating.
Companies like Turner Construction have implemented cross-generational training programs, where employees work side by side on real-world projects using innovative tools. This approach accelerates learning, fosters stronger team connections, and encourages open communication.
Collaborative training also provides a platform for addressing concerns or misconceptions about technology. By allowing workers to ask questions and troubleshoot in a supportive setting, companies can ease the transition and create a culture where learning and innovation go hand in hand.
3. Make data-driven decisions
One of the most effective ways to encourage technology adoption is to demonstrate its value through data-driven decisions. Workers and managers are more likely to trust new tools when they see measurable improvements in productivity, safety, or cost savings.
For example, telematics systems in construction equipment provide real-time data on fuel consumption, maintenance needs, and usage patterns. According to the Association of Equipment Manufacturers, telematics can reduce fuel costs by 10-15% and significantly decrease equipment downtime. Sharing these tangible results with your workforce can show them how technology directly impacts the bottom line while simplifying their daily tasks.
Data-driven insights also play a critical role in improving safety. Wearable tech, such as smart helmets or sensors, can monitor workers’ vitals and environmental conditions, alerting teams to potential hazards. By consistently showcasing the positive outcomes of using technology, construction companies can build trust and enthusiasm among their teams. When workers see how data leads to smarter decisions and safer worksites, they’re more likely to embrace innovation as a valuable asset rather than a disruptive change.
4. Tailored implementation
Introducing new technology in construction works best when it’s tailored to meet the needs of a diverse workforce. Selecting user-friendly tools that cater to varying skill levels ensures that employees, regardless of their technical experience, can adapt without feeling overwhelmed. Features like intuitive interfaces, clear instructions, and hands-on support can help foster adoption among older workers.
In addition to choosing the right tools, gradual rollouts are key to success. Implementing technology in phases allows employees to adjust at their own pace while providing opportunities for feedback and refinement. For instance, a construction company might start with pilot programs for specific teams, gather insights on usability, and then scale up once workers feel confident and comfortable.
Tailored implementation boosts confidence and sends a clear message: technology is here to support workers, not replace them. By respecting employees’ learning curves and offering the right tools and pace, companies can create a culture that embraces innovation without leaving anyone behind.
5. Foster a culture of curiosity
A thriving workforce is always willing to learn, experiment, and adapt—and fostering a culture of curiosity can help bridge the technology adoption gap. Encouraging employees to approach new tools with an open mind and a willingness to explore boosts engagement and reduces the fear of change.
Providing opportunities for continuous learning could include regular workshops, access to online training resources, or even informal sessions where workers can test out new technologies in a low-pressure environment. When employees feel empowered to ask questions and experiment, they’re more likely to discover the value of these tools for themselves.
Recognizing and rewarding employees who embrace and champion technology is another effective way to encourage adoption. Highlighting tech-savvy workers as role models or incentivizing those who go above and beyond can motivate others to follow suit. When employees feel supported and valued in their learning efforts, transitioning to new technology becomes a shared journey rather than a solitary challenge.
Bottom line
Bridging the technology adoption gap in construction is essential for staying competitive in a rapidly evolving industry. While the challenges may seem significant, there are clear, actionable strategies to ease the transition.
By fostering collaboration through reverse mentoring, offering hands-on, collaborative training, leveraging data to demonstrate value, and implementing tools gradually and thoughtfully, companies can empower workers of all ages to embrace innovation. This enhances productivity and safety, strengthens team dynamics, and futureproofs the workforce.
Adopting technology isn’t just about keeping up; it’s about setting the foundation for long-term success. When every team member feels confident and supported, the entire organization benefits, creating a culture that thrives on tradition and innovation.
Stay ahead in the ever-evolving construction industry by subscribing to our newsletter for the latest insights, tips, and strategies to drive innovation and success in your business.