Hand injuries are common in construction, affecting nearly half a million workers in Canada per year. Injuries include punctures, lacerations, crushes, fractures, burns, and strains, most of which are preventable with proper PPE and procedures to mitigate the risks.
While injuries can sometimes be an inevitable part of working in construction, these injuries can lead to time off work and come at a high cost to employers. OSHA’s hierarchy of controls provides guidelines for worker protection from most to least effective.
Hand injuries in construction are common
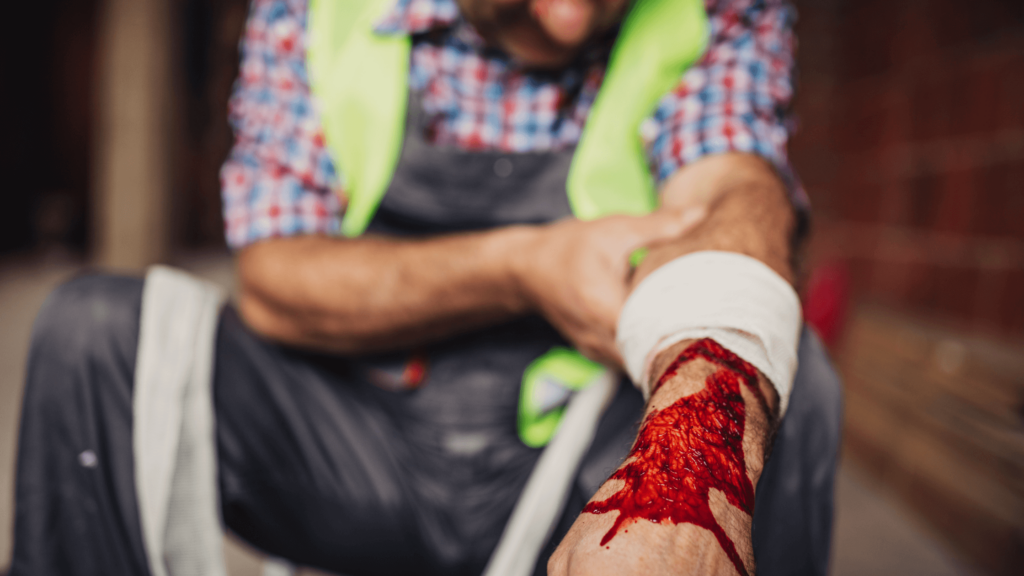
According to the US Bureau of Labor Statistics, hand injuries account for approximately 20% of all work-related injuries. Our hands are used in virtually everything we do, often put in vulnerable positions and situations on the job site. Even taking precautions, the unforeseen can quickly lead to accidents and injuries.
Common hand injuries
- Lacerations are the most common type of hand injury, usually caused by sharp objects or tools. They also typically occur due to improper gloves or no gloves at all.
- Crush injuries happen when a worker places their limb within a pinch point that closes. A pinch point is where you can get caught between moving and stationary equipment.
- Fractures often occur from machinery accidents, falling objects, or other hazards. They are broken bones, and there are two types: closed fractures, where no skin is broken, and compound fractures, which are open with broken bones penetrating the skin.
- Punctures occur when pointed objects pierce the skin. They could be from any source, like spurs from damaged metal cables, nails, or splinters from lumber. Wearing proper gloves for the task is vital to avoid punctures.
Less common hand injuries
- Amputations are less common but often the most traumatic. Amputations occur when limbs are completely severed from the body.
- Stiff joints usually occur from repetitive motion injuries.
- Nerve damage can occur when the median nerve is compressed, usually caused by repetitive hand movements while using tools.
- Paralysis occurs when you lose functionality in your hand(s). It occurs when messages from the brain are interrupted as they travel to your hand and prevent movement. Paralysis can be caused by injury or illness, such as neck or spinal cord injuries.
- Burns can be caused by heat, electrical, or chemical contact and can vary in severity. Some may require minor medical attention, while others may need surgery to repair the skin.
Implications of hand injuries
Workers suffer after hand injuries due to pain and suffering, loss of mobility and function, and possible loss of work. Employers also suffer from loss of productivity and possible temporary replacement of the injured worker. OHS Canada puts the average cost for each lost-time hand injury at $7,500.
The U.S. Bureau of Labor Statistics data on hand injuries from 2021-2022 shows a breakdown of various factors relating to hand injuries. Most injuries occurred due to contact with an object or equipment, hand tools, and machinery. Cuts, lacerations, and punctures were the most common hand injuries.
Older workers often need up to 14 days to recover, and the compensation cost for lacerations and punctures came to nearly $31,000 per claim. In 2017, almost 10,000 workers missed days due to soreness and other pain from repetitive tasks and frequent hand movements that disrupted productivity.
Indirect costs of hand injuries include wages not covered by workers’ compensation, administrative time spent by supervisors, employee retraining or replacement costs, lost productivity, loss of morale after injury, and accommodations of injured employees.
Preventing hand injuries doesn’t start with PPE
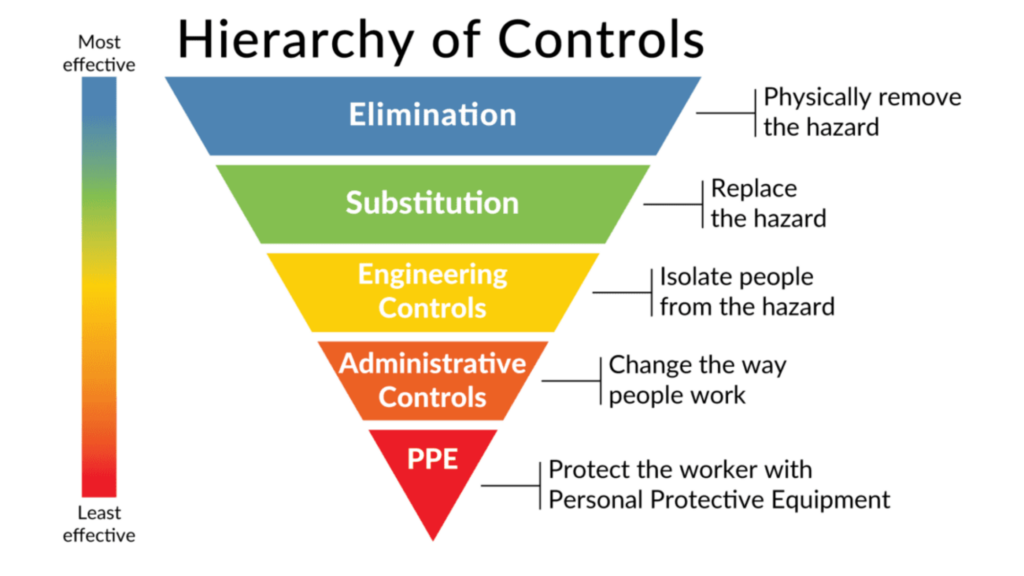
PPE is the least effective control method for worker protection based on OSHA’s hierarchy of controls.
- Elimination
- Substitution
- Engineering controls
- Administrative controls
- PPE
Elimination: This is the most effective control method. Although not always possible, designing the workplace with safety in mind can reduce incidents. Some ways to minimize injury are eliminating blindspots, controlling foot traffic in storage locations around moving equipment, and utilizing automated-guided vehicles and conveyors to mitigate workers entering hazardous areas.
Substitution: This refers to replacing hazardous equipment or processes with safer methods. For example, fork trucks can be replaced with powered walk-behind forklifts or hand trucks.
Engineering controls: These controls refer to isolating people from hazards with pedestrian aisles, barriers, and walkways to keep pedestrians away from dangerous situations. They also include adding mirrors at blind corners and motion detectors/alarms, limiting access to buildings, and limiting the speeds of mobile equipment.
Administrative controls: This can involve putting warning lights and backup alarms on mobile equipment or sensors on forklifts to sense objects and pedestrians. Procedures and training, limiting access to machine operation areas, providing appropriate training and awareness, requiring headlights, and coordination between people and forklift operators for specific tasks like inventory are also administrative controls to reduce injury incidence.
PPE: Requiring workers and visitors to wear appropriate personal protective equipment for job sites or tasks is the least effective control method but must be mandatory for all job sites. This can include high-visibility vests, safety glasses, appropriate gloves, hard hats, and safety boots.
Tips to prevent hand injuries on the job site
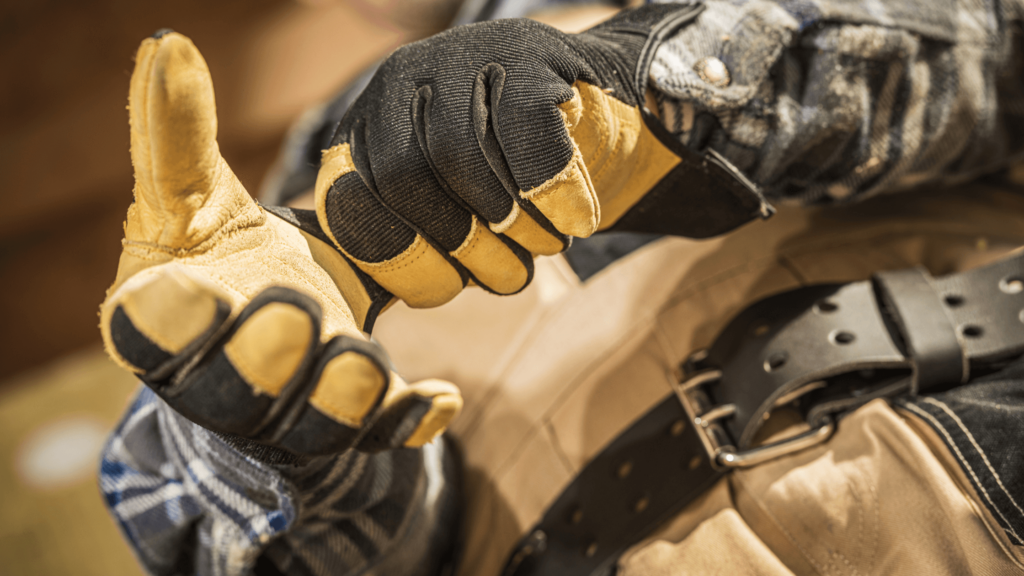
1. Eliminate the hazard
When possible, eliminate the hazard from human reach. Keep hands out of the hazardous zone by utilizing objects like a push stick or pike pole. If possible, use lock-out tag-out (LOTO) to completely shut off equipment.
2. Proper safety training
Never perform a task you haven’t been trained to do. If unsure, ask for training to proceed. Never agree to unsafe work, always insist on proper planning and training with each job task for everyone’s safety.
3. Hand protection
The cost of supplying a high volume of gloves to workers is relatively high for employers, but injuries cost more in the long run. Data shows that roughly 70% of workers who received a hand injury weren’t wearing gloves, and the other 30% had inadequate/damaged or the wrong type of gloves. Not all gloves are made the same, nor for every job.
- Leather gloves provide great protection against rough surfaces and sharp edges that can cut or puncture. They are best for equipment handling and general construction.
- Cotton gloves improve grip, insulate from heat or cold, and provide some protection from cuts. They are best for light-duty and general material handling.
- Kevlar is highly cut-resistant when wet. These are best for working with metal and glass.
- Dyneema fiber is an ultra-high-molecular-weight polyethylene (UHMWPE) glove. It offers advanced protection with gel-spun, multi-filament fibers. It’s best for metalwork, automotive, and heavy equipment.
- Spectra fiber is another ultra-high molecular weight polyethylene fiber that is cut-resistant when wet. It’s best for metalwork, automotive, food preparation, and warehouse work.
- Metal mesh is made of interlocked stainless-steel mesh and offers advanced protection against cuts and punctures. It’s best for metalwork, food preparation, and textile cutting.
4. Be aware of your surroundings
Always be aware of what’s around you and where your hands are. Stay alert and be mindful of moving equipment and pinch points. It’s also important to pay attention to who is around you that could be at risk.
5. Shortcuts
Avoid shortcuts to finish the job faster—work at your own pace. The frequency of hand injuries is proportional to how fast you work. Do a risk assessment for the task, regardless of whether your employer requires one.
6. Job safety analysis (JSA)
A job safety analysis (JSA) identifies and records the steps involved in a specific task. It may include potential safety/health hazards and how to reduce/eliminate them, who may get injured during the task, determined level of risk, types of injuries, how frequent the exposure is, and what safety gear is needed for optimal protection.
Learning from hand injuries and prevention
Safety should be the number one priority for both employers and workers. While the cost of hazard mitigation may seem high, it’s quickly outweighed by the cost of injuries, time away from work, and loss of employees. Following OSHA’s hierarchy of controls offers a simple way to reduce the number of injuries and accidents, but it’s not a be-all. Proper training and awareness are also essential to ensure worker safety.
2 comments