Heavy machinery is the backbone of construction, engineering, and industrial projects, playing a critical role in completing large-scale tasks efficiently. However, its size, complexity, and power make safety a top priority, as accidents can lead to severe injuries or significant project setbacks. Key measures like thorough equipment inspections, providing comprehensive operator training, and implementing technology solutions can enhance safety standards to keep workers protected while ensuring seamless operations.
Quick look
- Mishandling heavy machinery can lead to severe accidents. Understanding potential risks—like operator error, poor visibility, or equipment failure—helps crews stay alert and avoid dangerous situations.
- Routine checks are essential. Look for wear and tear, monitor fluid levels, and address warning lights before each shift to catch minor issues before they escalate into serious hazards.
- Proper training ensures operators understand their equipment’s capabilities and safety protocols. Refresher courses and emergency response drills are critical for maintaining job site safety.
- Awareness is critical for both operators and ground workers. Establishing clear walkways, using universal hand signals, and leveraging tools like radios minimize miscommunication and accidents.
- Proximity sensors, cameras, and telematics systems help detect blind spots, monitor machinery performance, and alert teams to potential issues, enhancing safety across the board.
- Emergency response plans, regular safety meetings, and accessible first aid kits prepare crews to handle accidents calmly and effectively, reducing risks and ensuring quick recovery.
The dangers of heavy equipment
Heavy machinery has the potential to cause severe injuries and fatalities if not appropriately handled. Accidents may result from equipment malfunction, poor visibility, or operator error, creating hazards for workers nearby. Inadequate training can compound these risks, leaving employees unaware of how to respond to emergencies. Additionally, machinery’s sheer weight and force can turn minor mistakes into catastrophic events. Ensuring all workers understand the dangers is the first step in fostering a safer job site.
10 best practices for using heavy equipment
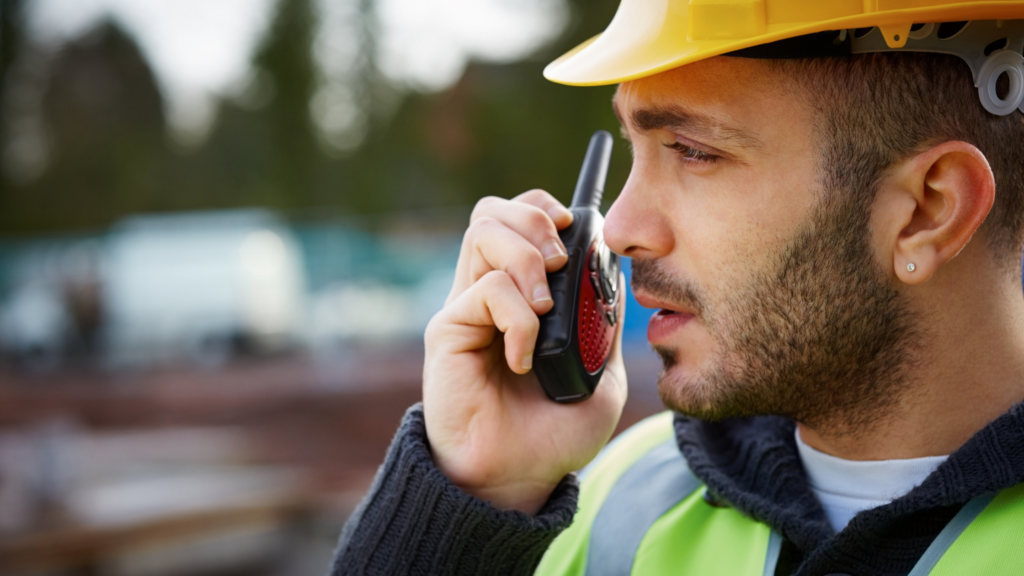
1. Always inspect before use
Routine inspections prevent small issues from escalating into dangerous situations. Operators should check brakes, hydraulics, and tires to ensure all parts are in good working order. Identifying wear and tear early can reduce the risk of equipment failure during operation. Fluid levels and warning lights also require monitoring, as they can indicate potential malfunctions. Ensuring machinery is safe before every shift protects both operators and nearby personnel.
2. Awareness
Staying alert is essential when working near heavy machinery. Operators must be aware of blind spots and surroundings to avoid collisions. Ground personnel should stay clear of moving equipment and use clear signals when approaching. Job sites should establish designated walkways to separate foot traffic from operating zones. Increased awareness minimizes preventable accidents and fosters a culture of safety.
3. Proper training and education
Thorough training ensures operators know how to manage their machinery safely. Workers should understand the manufacturer’s guidelines and safety protocols for every piece of equipment. Regular refresher courses can keep skills sharp and introduce new safety practices. Knowing emergency procedures is also crucial, ensuring quick action if something goes wrong. Investing in education empowers employees to work confidently and safely.
4. Know machine limitations
Understanding what equipment can and cannot do is vital for safe operation. Exceeding weight limits or misusing attachments can cause machinery to malfunction, leading to accidents. Operators should always follow the manufacturer’s specifications and avoid shortcuts that compromise safety. Knowing the machine’s capabilities helps operators make informed decisions and maintain control in challenging conditions.
5. Proper communication with operators
Clear communication between operators and ground personnel reduces misunderstandings that can lead to accidents. Two-way radios or hand signals ensure instructions are understood during operation. Job sites should establish universal signals to eliminate confusion, even among new team members. Keeping lines of communication open ensures everyone is on the same page, improving safety and efficiency.
6. Establish safety zones
Defining restricted areas around machinery minimizes the chance of unauthorized access and collisions. Safety barriers or cones can designate zones where only trained operators are allowed. Groundworkers should never enter these zones without notifying the operator. Clear boundaries keep both operators and nearby workers safe from unintentional harm.
7. Wear appropriate safety gear
Personal protective equipment (PPE) is non-negotiable on job sites with heavy machinery. Helmets, gloves, high-visibility clothing, and steel-toed boots are essential for reducing injury risk. Reflective gear is particularly useful in low-light conditions, making workers more visible to operators. Properly worn and maintained PPE is the last line of defense in an accident.
8. Implement technology solutions
Modern technology offers tools that enhance job site safety. Proximity sensors and cameras improve visibility, helping operators detect people or objects in blind spots. Telematics systems monitor equipment performance and notify operators of potential issues. By leveraging these tools, companies can prevent accidents and maintain better control over their operations.
9. Maintain consistent safety meetings
Regular meetings reinforce safety protocols and keep workers informed about potential hazards. These sessions can address recent near-misses and provide updates on equipment or procedures. Including all employees in safety discussions fosters accountability and ensures a unified approach to risk management. Frequent reminders help safety remain a top priority.
10. Develop emergency response plans
A well-practiced response plan ensures swift action in case of accidents. Workers should know the location of first aid kits, fire extinguishers, and emergency exits. Regular drills can prepare employees to act calmly under pressure. Planning for worst-case scenarios minimizes chaos and reduces the likelihood of severe outcomes.
Bottom line
Enhancing safety around heavy machinery requires commitment and proactive measures. These practices keep workers safe and improve job site efficiency and morale. To explore more expert tips and stay updated on construction safety, subscribe to our newsletter at Under the Hard Hat.
1 comment