Building costs in major global cities have skyrocketed, and it’s not hard to see why. Limited land availability, high labor costs, and strict building regulations make construction much more expensive, especially in cities such as Hong Kong, London, and New York. For developers, these challenges can turn a simple project into a costly venture.
The 10 most expensive cities to build in
London, England
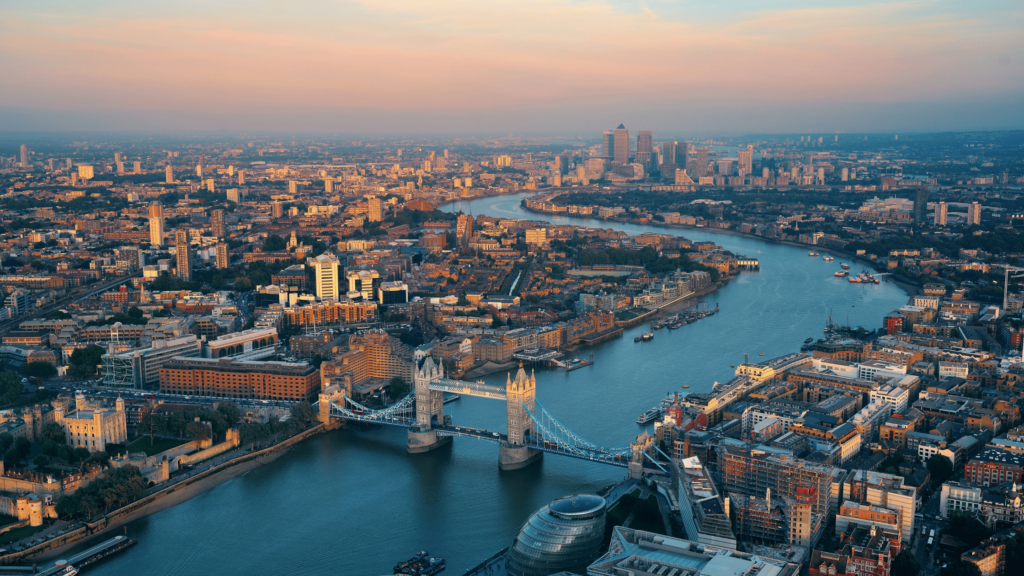
London is one of the priciest places to build, and it all comes down to a few key factors. First, land costs are through the roof, with so much demand and so little space to build on. Then, you’ve got tight building codes that add extra layers of complexity and cost to any project. On top of that, there’s a shortage of skilled labor, which drives wages up. When you put it all together—limited space, tight rules, and higher wages—it’s no surprise that London sits high on the list of expensive cities to build in.
Geneva, Switzerland
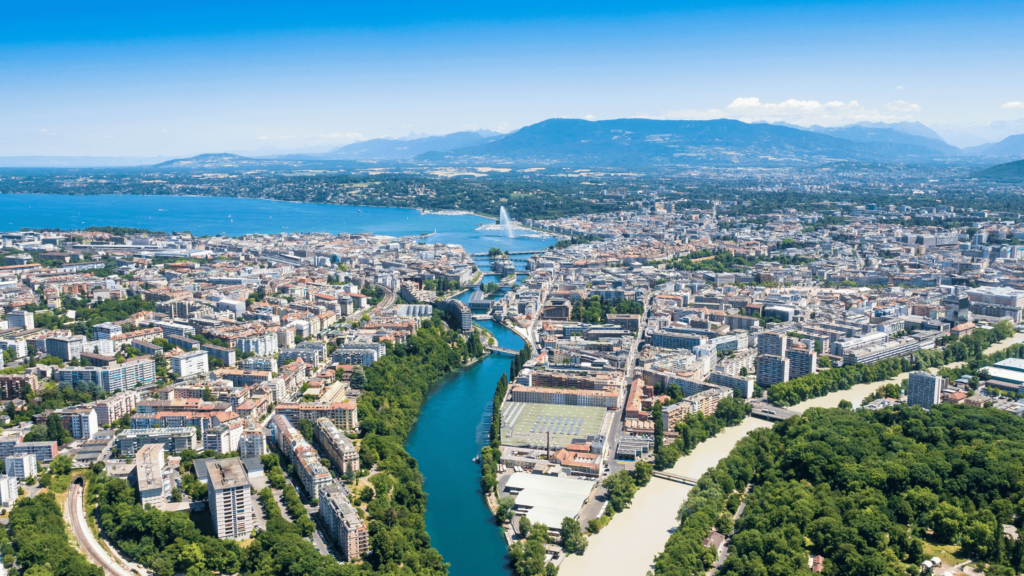
Geneva’s construction costs are some of the world’s highest, largely due to a few key factors. Wages in Switzerland are generally very high, so labor costs for construction projects quickly add up. Geneva also has strict environmental regulations that builders must follow, which can slow down projects and increase costs with eco-friendly materials and energy-efficient systems. To top it off, the city’s competitive real estate market drives demand, making everything from land to materials more expensive. Geneva’s strong emphasis on green building standards and practices only adds to the price tag.
Zurich, Switzerland
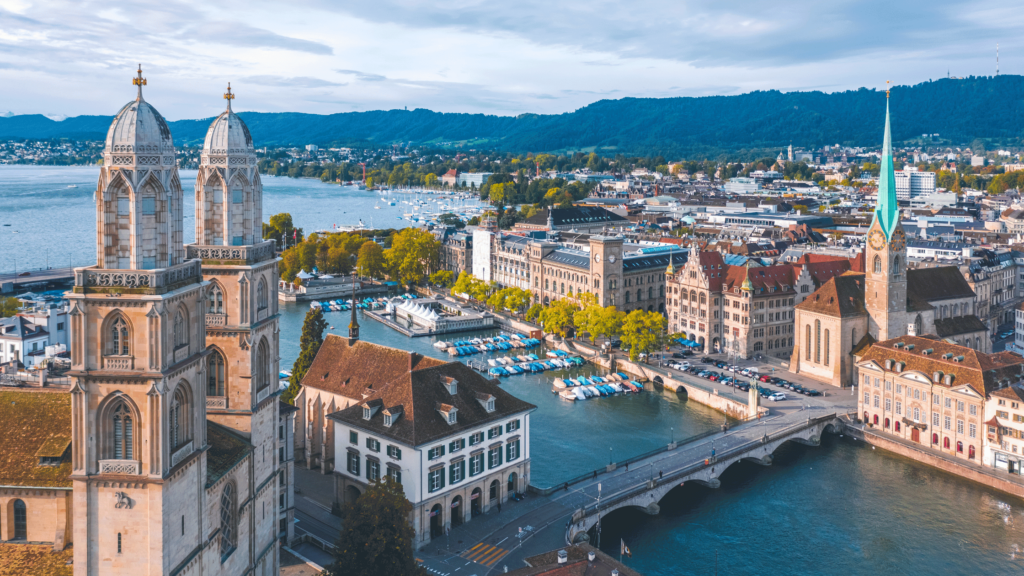
Zurich is no stranger to high construction costs, and a big reason is Switzerland’s overall high labor costs. Skilled workers in Zurich are well-paid, making any building project pricier from the start. On top of that, Zurich is known for its tight building standards, emphasizing quality and precision, so meeting these requirements often leads to more expensive materials and longer timelines. The city also faces a land shortage, which makes available plots highly competitive and expensive, driving up development costs even further.
Munich, Germany
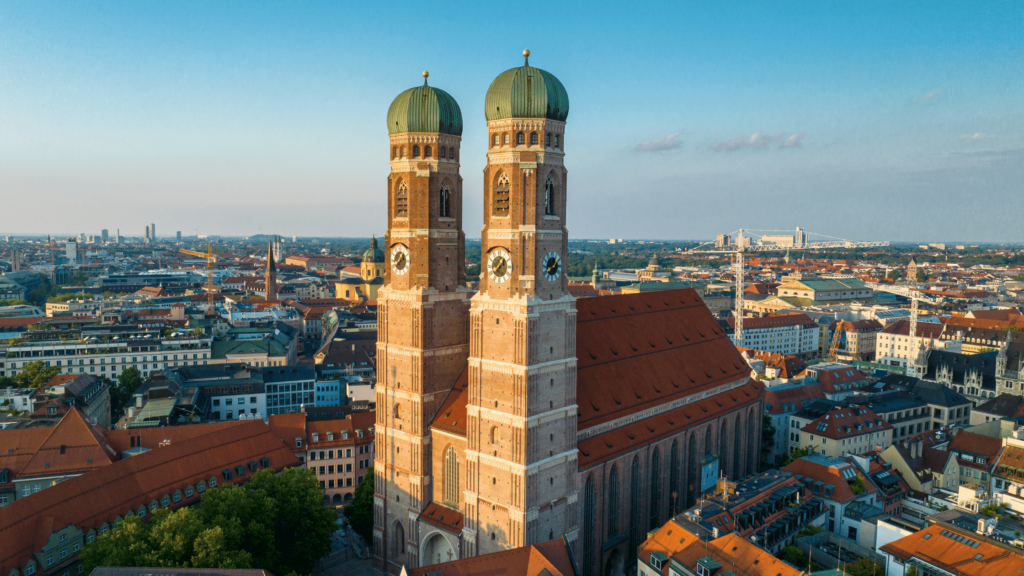
Munich’s booming economy is one of the main reasons construction costs are so high. With businesses thriving, there’s a huge demand for new buildings, particularly in the commercial sector, which pushes prices up. On top of that, local regulations are very rigorous, adding more complexity—and cost—to any construction project. Land in Munich is also expensive, thanks to its popularity and limited availability. Altogether, these factors make building in Munich a pricey endeavor for developers.
New York City, New York
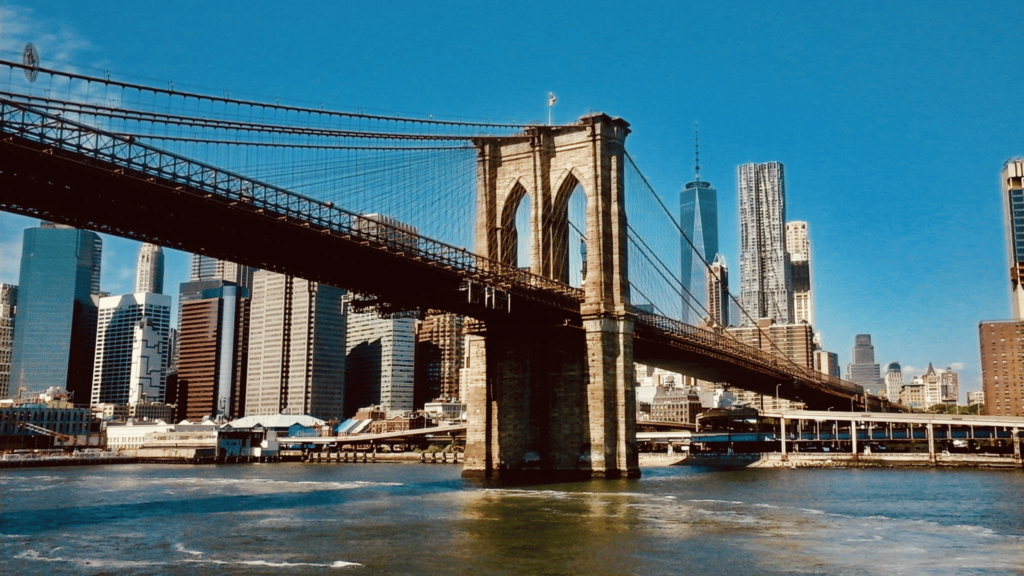
New York City is notorious for its sky-high construction costs, and there are a few reasons why. First, land in the city is incredibly expensive, especially with the constant demand for prime real estate. Construction labor shortages also play a big role, increasing wages and making projects costlier. Add to that the city’s complex building regulations, and even a simple project can become a financial headache. With NYC’s iconic skyline and the constant push for new developments, it’s no wonder the Big Apple ranks among the most expensive places to build.
San Francisco, California
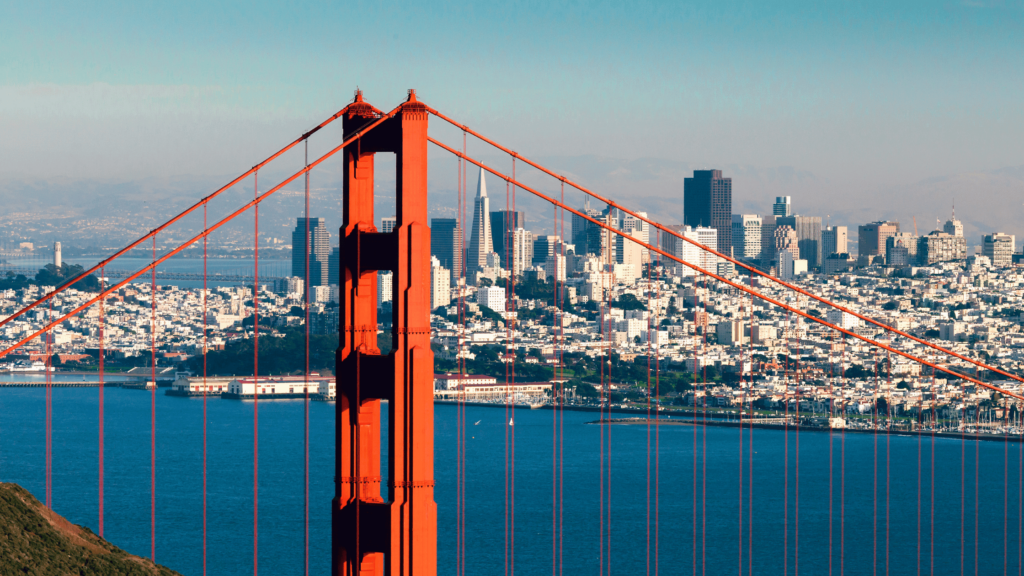
San Francisco’s tech boom has driven real estate prices through the roof, making land some of the country’s most valuable—and expensive. As a result, construction costs have skyrocketed to match. On top of that, the city’s location on the San Andreas Fault means that builders must use specialized techniques and materials to ensure structures can withstand seismic activity, which adds even more to the cost. With the high demand for development and the added expense of earthquake-resistant designs, building in San Francisco is expensive.
Philadelphia, Pennsylvania
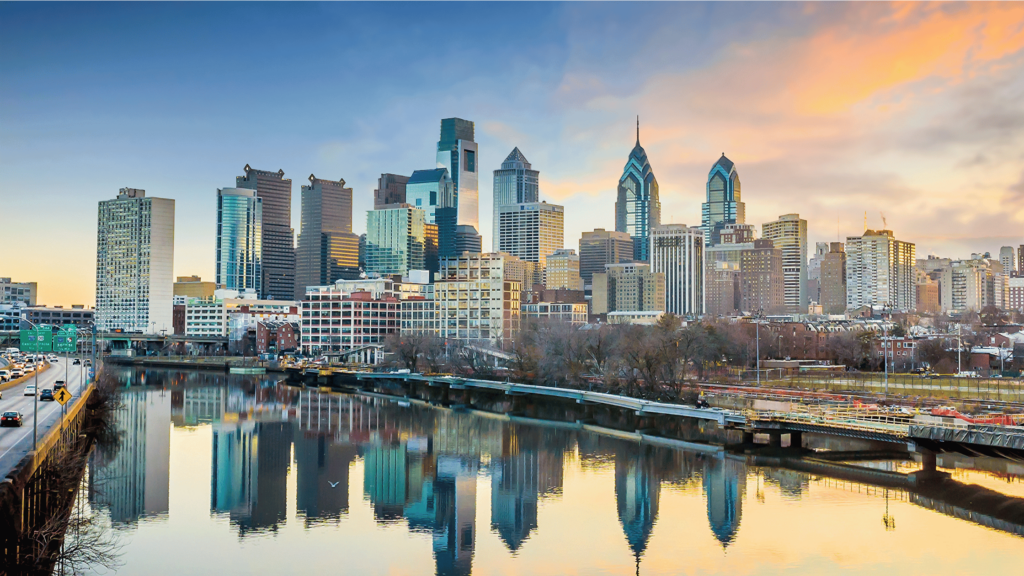
Philadelphia’s construction costs are rising, and several factors contribute to that. Rising labor expenses are a big driver, as the city’s skilled workforce comes at a premium. Regulatory requirements and building codes also add to the expense, particularly in older neighborhoods where infrastructure upgrades are often needed before new projects can even begin. As Philadelphia’s real estate market continues to grow, the increasing demand for residential and commercial developments further pushes construction costs, making it a pricier city to build in.
Copenhagen, Denmark
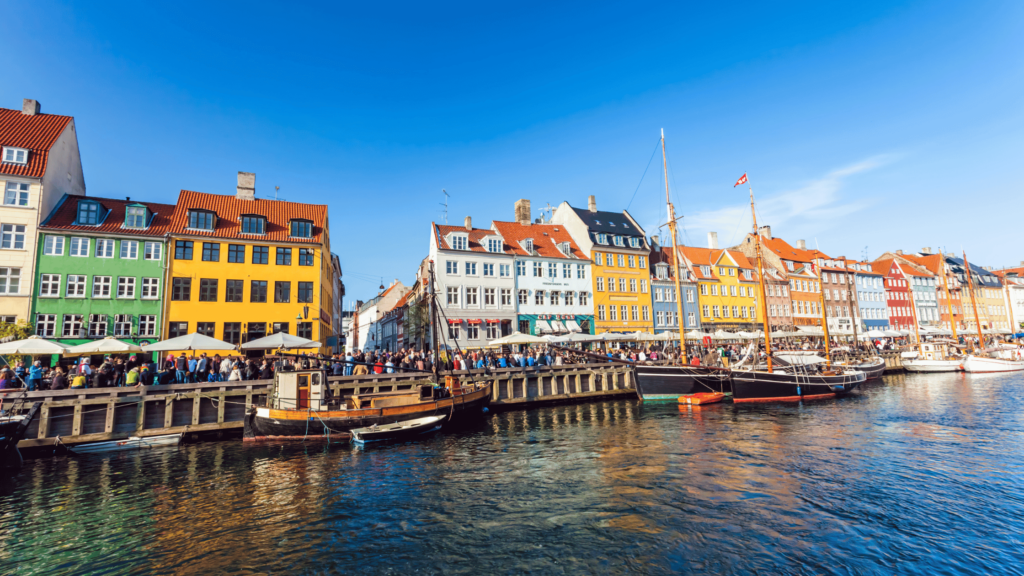
Copenhagen is known for its high construction costs, and there are several reasons why. Denmark’s strong labor unions mean that wages are relatively high, driving up labor costs for any project. The city also has strict building codes that must be followed, adding complexity and expense to construction plans. On top of that, Copenhagen strongly focuses on sustainability, so eco-friendly construction methods and materials are often required, which can be more expensive than traditional options.
Hong Kong
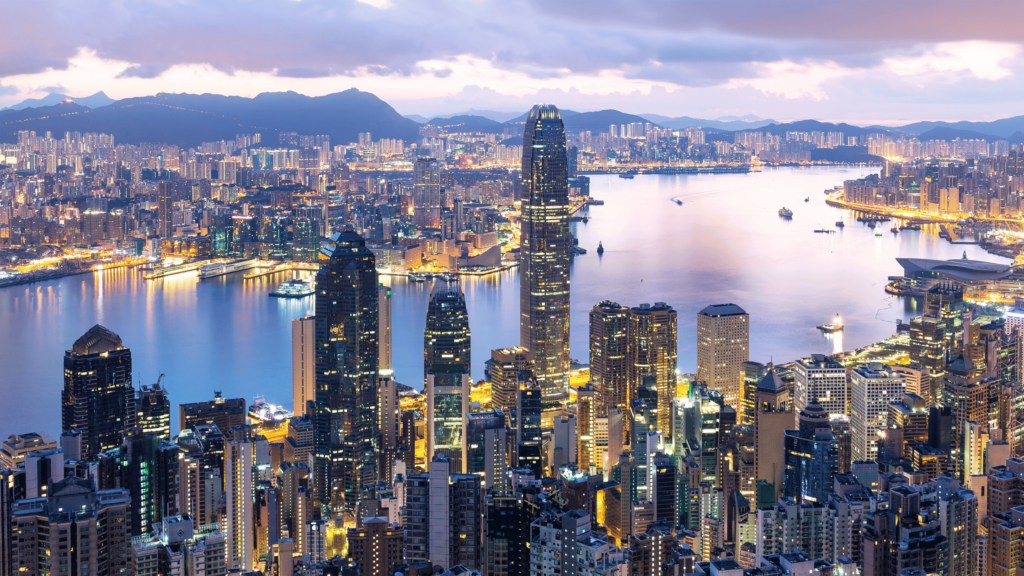
Hong Kong is one of the most densely populated cities in the world, and with such limited land available, construction costs are sky-high. The city’s steep terrain adds another layer of complexity, often requiring advanced engineering solutions that drive up prices even more. Labor and material costs are also higher due to Hong Kong’s booming economy, making every aspect of a building project more expensive. With all these challenges combined, it’s no wonder construction in Hong Kong comes with such a hefty price tag.
Bristol, England
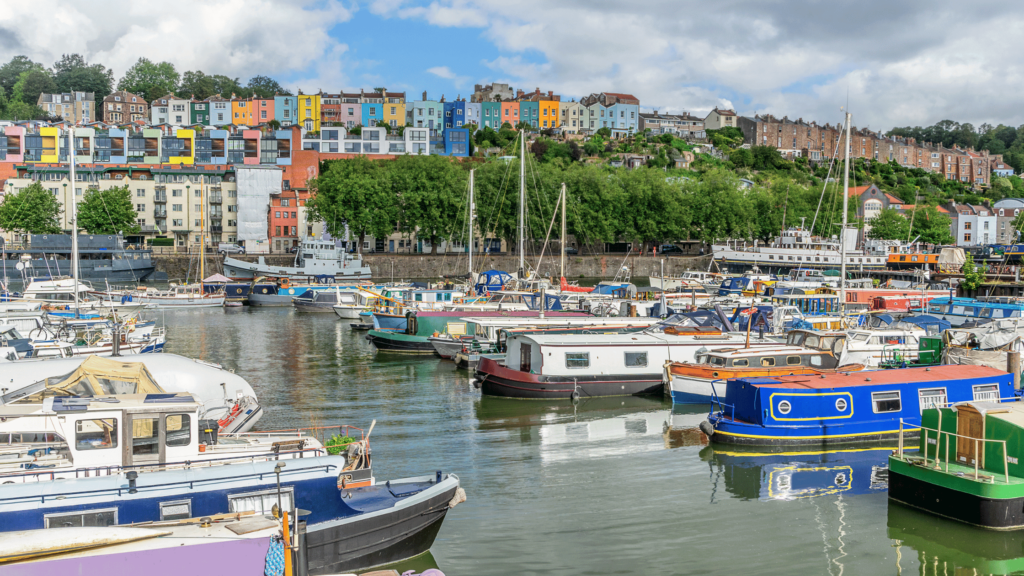
Built around the River Avon, Bristol’s construction costs have climbed in recent years, mainly due to high demand for housing that has outpaced supply. Labor shortages in the construction industry are another big factor, leading to higher wages and increased project costs. The city’s dedication to preserving its rich historical architecture also means that many building projects face complex building codes and additional expenses to maintain Bristol’s unique character. On top of that, there’s a growing emphasis on sustainable building practices, which can add extra layers of cost to any construction effort.
Building in these cities is not for the faint of heart (or wallet). Whether you’re a developer or just curious, understanding these cost drivers can provide valuable insights into the global construction landscape.