The families of one ironworker killed and another injured at the University of Chicago Hospital construction site are suing Turner Construction Company and Adjustable Forms Inc. for negligence.
The first lawsuit was filed on behalf of Jeffrey A. Spyrka, an ironworker who fell over 100 feet when a scaffold at the University of Chicago Hospital’s new cancer center project failed in high winds. A second lawsuit, filed for the family of David O’Donnell, a technical engineer who suffered fatal injuries in the fall, was also filed in mid-June.
Partners of the Chicago-based law firm GWC Injury Lawyers, Louis C. Cairo, Louis Anthony Cairo, and Michael D. Fisher represent both lawsuits. They seek redress for the workers’ deaths and/or injuries. The Spyrka lawsuit names Turner Construction Company, alleging that the GC failed to take appropriate safety measures to ensure the scaffold system that surrounded all sides of the core of a new building was safely and properly erected.
The Spyrka lawsuit alleges that Turner caused scaffold work to continue at great heights on the building’s exterior when high winds were known to be occurring. The suit says these dangerous conditions were ignored, risking the safety of the men working on the scaffolding.
The Spyrka lawsuit also names Adjustable Forms, Inc. as a second defendant. The company built a concrete form pouring system with a trailing scaffold set up 20 feet below the form pouring section but improperly built the scaffold system.
The suit alleges that the scaffold was so shoddily built that the corners could separate and move under any condition, especially the pressure of high winds. According to the lawsuit, an Adjustable Forms representative assured workers that the scaffold system raised to the 9th floor was safe to work on despite weather conditions.
David O’Donnell was the last worker to reach the scaffold, stepping onto it and briefly talking with Spyrka and another Ironworker near the southwest corner of the scaffold. Soon after, a gust of wind separated the southwest corner of the scaffold, causing the southerly scaffold section to swing violently away from the wall. Spyrka and O’Donnell were tossed over eight stories to the ground.
Spyrka, 36, and his wife, Ashley, have been married for eight years. They have three children under six years old. He has extensive experience as a Local 1 Ironworker and has an impeccable safety record.
“The fact that Jeff survived this fall is nothing short of a miracle and a testament to the fine medical doctors who are treating him 24 hours a day in ICU at the same hospital where this horrific work accident occurred,” stated a press release from the law firm. “Nonetheless, he has suffered life-altering, catastrophic injuries as a result of this fall.”
“The Spyrka family is thankful that those efforts have saved Jeff’s life, although they mourn the loss of David O’Donnell, who was a friend, a building trades brother, and an amazing young man,” GWC said. “For years, David worked side by side with countless Ironworkers doing the layout work for their trade work. His passing is mourned by the members of both those in the Technical Engineers division of his Local 130 union, as well as the many Ironworkers in IW’s Local 1.”
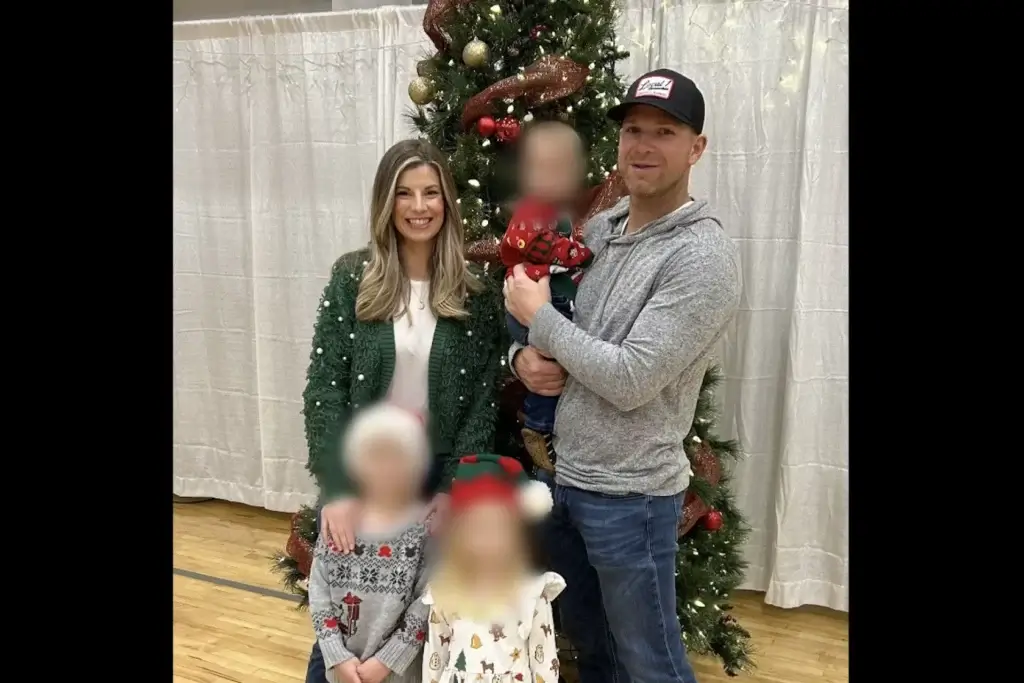
Jeffrey Spyrka, pictured with his family, survived a fall from scaffolding on June 6 while working on a construction site at the University of Chicago Hospital.
O’Donnell, 27, is survived by his parents, David and Christine O’Donnell, and his brothers, Brendan (32), Kevin (26), and Patrick (20). O’Donnell was trained as a technical engineer in the Apprentice Training Program with Local 130 and has since worked for his father’s company.
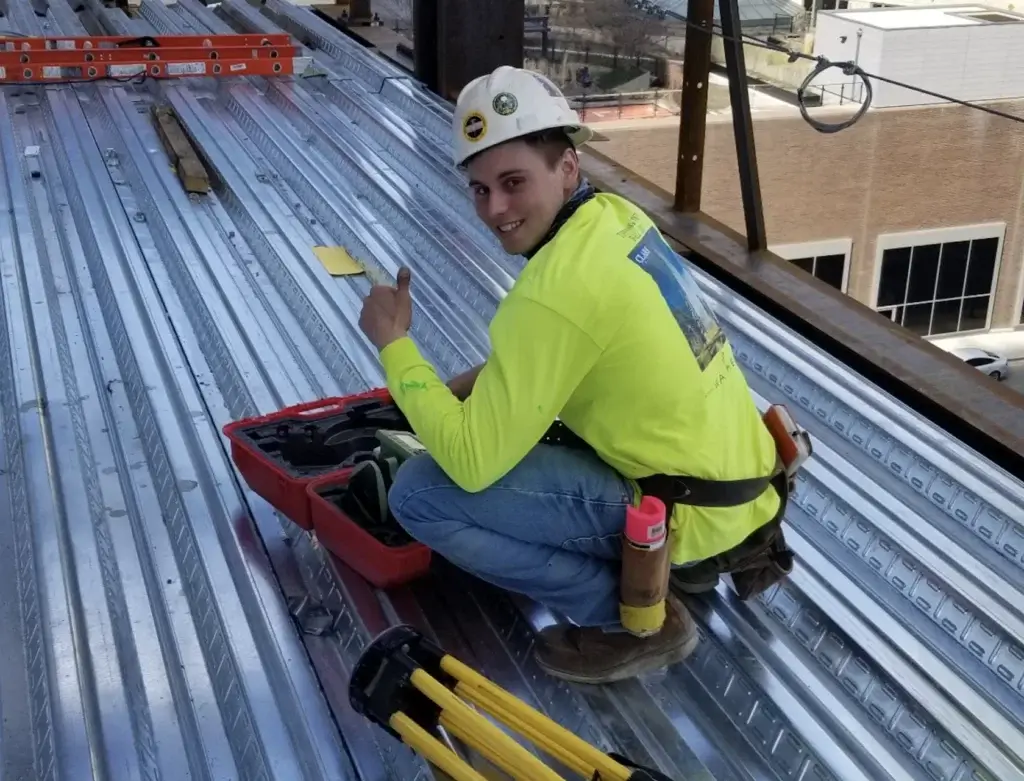
David O’Donnell, 27, died after being thrown from scaffolding more than eight stories to the ground.
“He has been groomed by his boss/father/dear friend, Dave Sr, to ultimately take over the company business. Dreams and aspirations have been shattered in the O’Donnell family as a result of this incident,” the GCW Law firm press release said.
Turner Construction did not answer requests for comments on this story. Lombard, IL.-based Adjustable Concrete did issue a statement.
“We are aware of the recent filings and continue to be deeply saddened to learn of this accident. We offer our sincerest condolences to the loved ones of those affected. Safety is integral to what we do, and Adjustable Concrete is partnering with Turner Construction to support a full investigation into this matter alongside the Occupational Safety and Health Administration. We are deeply grateful to the University of Chicago Medical Center doctors and all first responders involved,” Eric Lindquist, PE, President of Adjustable Concrete, said in a statement on the accident.