The Capital One Arena in Washington, DC, is getting some fresh new upgrades, including expanded facilities, state-of-the-art upgrades, and design elements to attract fans to the arena. Monumental Sports and Entertainment (MSE) announced that Clark Construction Group (Clark), Gensler, and CAA ICON will partner to deliver the upgrades.
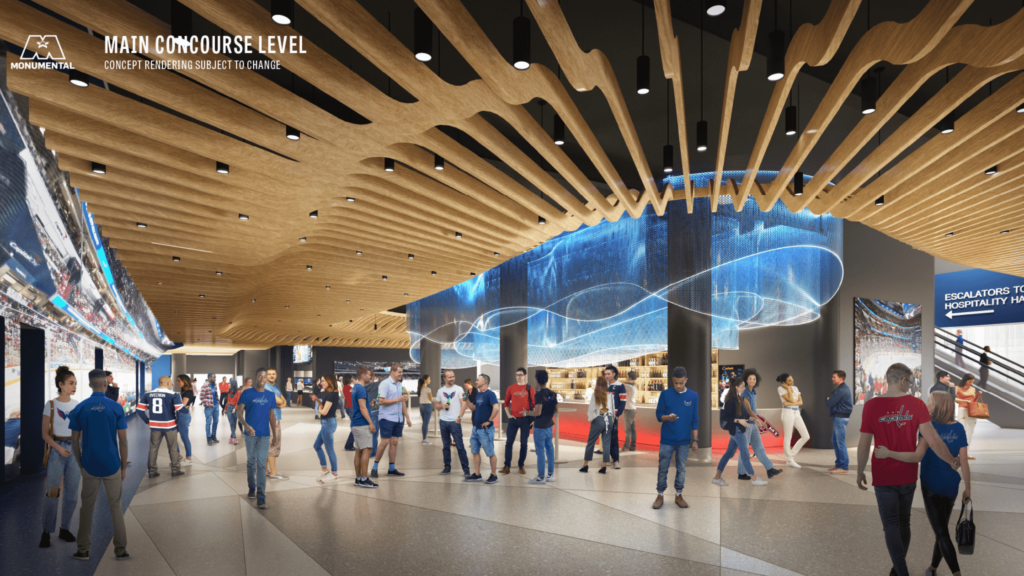
Clark Construction Group built the original arena, and MSE says that having the firm participate in the renovation ensures a smooth process due to their “unparalleled expertise and familiarity with the building’s structure.”
Design and architecture firm Gensler has taken the reins on the renovation’s design. Co-CEO Jordan Gensler explains that the changes are intended to improve the experience for fans and athletes alike, saying, “The upcoming transformation of Capital One Arena will improve the connection between player and fan through immersive engagement, significant architectural intervention, and enhanced arena operations.”
CAA ICON will join as MSE’s owner’s representative, ensuring the arena’s renovation vision and execution align with MSE’s goals.
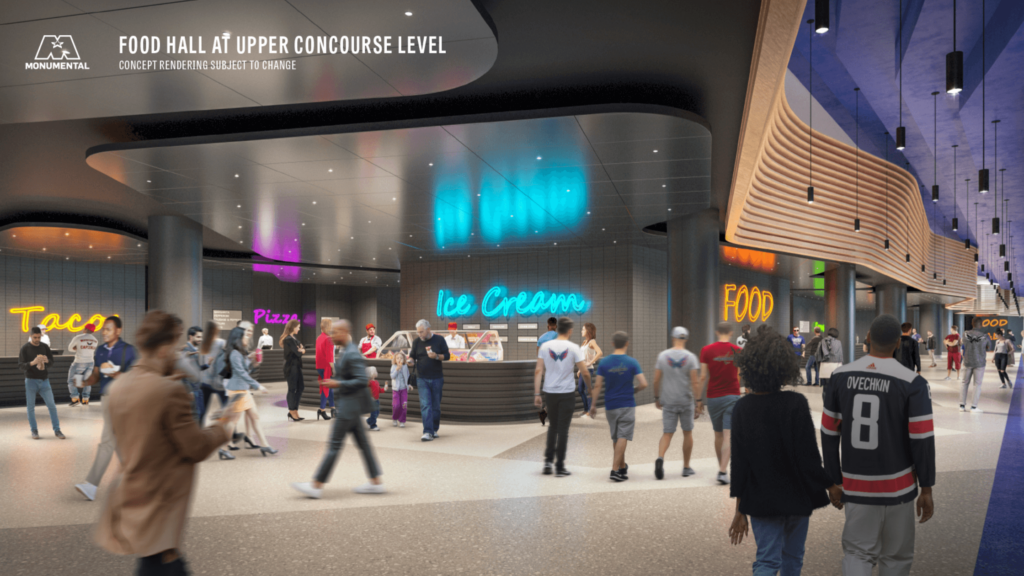
In a press release, Jordan Silberman, president of venues at MSE, said: “Clark, Gensler, and CAA ICON are industry leaders with a wealth of local and national experience and proven track records in planning and executing complex projects. We are excited to collaborate with them to reimagine Capital One Arena, creating the spaces for unforgettable experiences for fans, athletes, and the community. Together, we’re laying the foundation for an entertainment district that will serve as a vibrant destination for generations to come.”
The upgrade’s specifics include 65% more concession space, 30% more bathrooms, a new players’ lounge and dining room, and an expanded entrance at F Street to assist fans entering and exiting the arena.
The project is expected to positively impact Washinton’s economy by supporting local businesses and prioritizing DC residents when hiring for job opportunities. The cost of arena upgrades will be shared, with Washington District paying $515 million towards arena renovations and MSE contributing at least $372 million, plus any costs over the initial project cost estimate.
The project is expected to be completed in time for the 2027-2028 season.
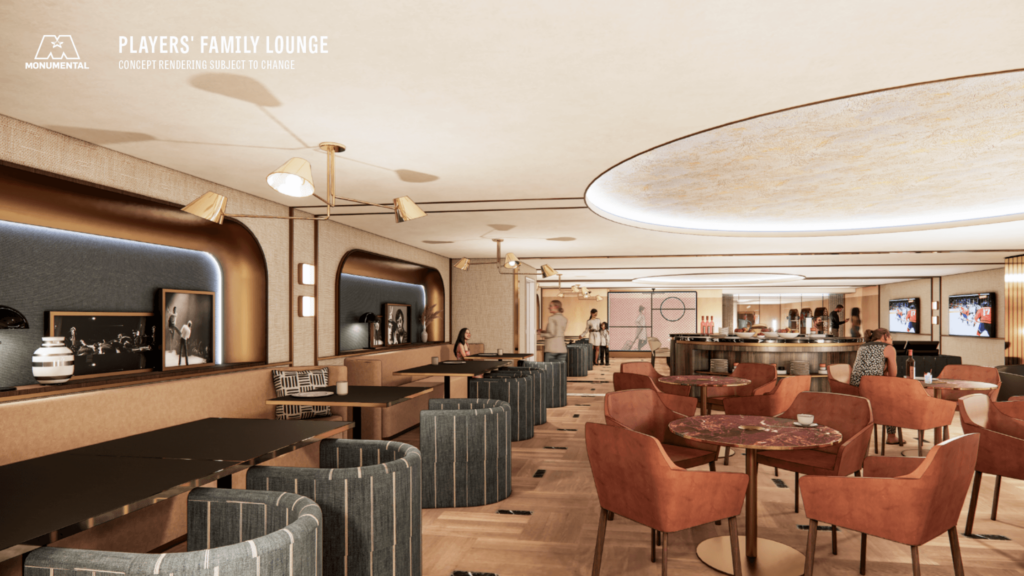
Like this and want more? Follow us on social media and subscribe to our weekly newsletter for current projects, health and wellness, technology, and more.