The wholesale lumber industry is shifting as major companies buy out smaller ones, consolidating the market like never before. This trend raises questions about the future for builders, suppliers, and even homeowners. As smaller businesses disappear and larger corporations dominate, it could reshape pricing, competition, and the availability of materials.
Drivers of consolidation in the lumber industry
The lumber industry has seen a wave of mergers and acquisitions, especially in the past decade. For example, in 2022, Interfor Corporation acquired EACOM Timber Corporation, expanding its presence in Eastern Canada. In December 2021, West Fraser completed the purchase of the Angelina Forest Products lumber mill in Lufkin, Texas, further strengthening its presence in the Southern U.S. Interfor and West Fraser are some of the largest producers of lumber in North America. Yet, these acquisitions are just the tip of the iceberg. Many have since followed.
This trend has raised concerns among the owners of smaller wholesale lumber yards, who believe they won’t be able to compete in the future. While competition is generally considered good, consolidation brings news challenges, eventually phasing smaller companies out. This has a profound effect on the entire lumber industry.
Concerns associated with industry consolidation
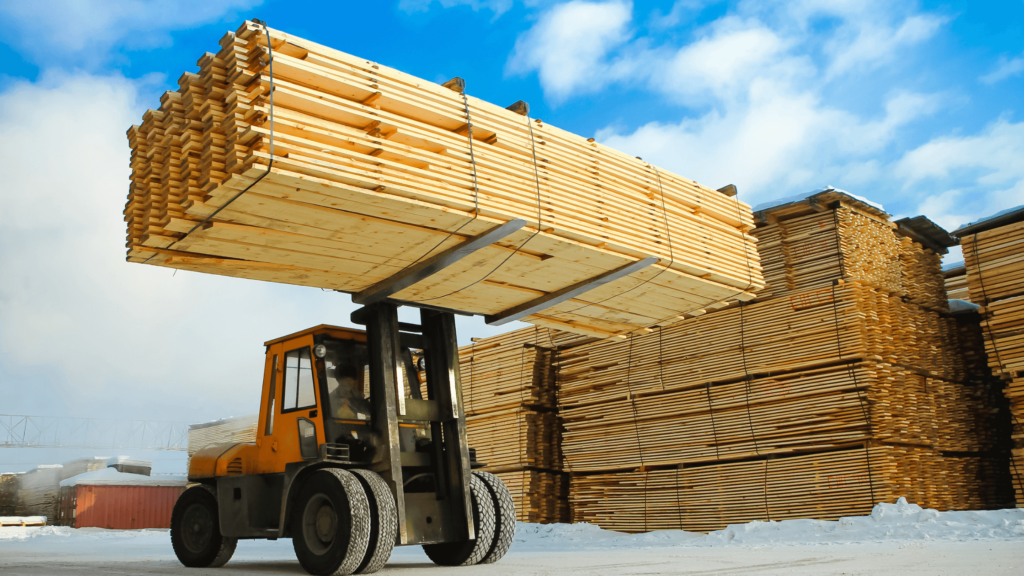
The bigger companies can eventually produce lumber far more efficiently than smaller companies because they operate on a larger scale. They can buy materials in bulk quantities that smaller lumber yards simply can’t afford. In doing so, they’re able to reduce production costs and cut overhead expenses, allowing them to set prices much lower than family-run mills with little pushback. The ability to use price manipulation for profit often leads to higher costs for builders and, ultimately, homeowners who rely on affordable materials.
In addition, as major players grow, their revenue allows them to buy more expensive equipment, further increasing their operational efficiency. With little room to make mistakes, family-run mills or regional suppliers often can’t compete with larger corporations’ resources, leading to closures, job losses, and fewer options for buyers looking to source materials locally.
Consolidation might seem like a natural progression for any industry, but it brings challenges that can’t be ignored. With fewer players in the market, there’s less pressure to develop new methods, products, or technologies. Instead of competing to stay ahead, dominant companies may focus more on maintaining their position.
Potential benefits of consolidation
While consolidation raises concerns, it also offers advantages that can’t be overlooked. Larger companies bring efficiency and improved supply chain management, which can positively impact the industry.
Here are some potential benefits of consolidation:
- Cost savings for larger companies: Streamlined operations, bulk purchasing, and advanced equipment reduce production costs, which could lower prices for customers in the short term.
- Innovation opportunities: With more resources, bigger companies can invest in research and development, leading to advancements like sustainable materials or more efficient milling techniques. However, larger companies may also get complacent and push resources to maintain market dominance instead.
- Improved supply chain management: Major companies can better coordinate production, distribution, and retail, ensuring a steady flow of materials during high demand or disruptions.
- Standardized practices: Fewer players in the market could lead to consistent quality and predictable availability, which benefits builders working on large-scale projects.
What the future holds for the lumber industry
Consolidation in the lumber industry shows no signs of slowing down. As large companies expand their influence, the market will likely become more centralized in 2025. For smaller businesses, this means an uphill battle to survive unless they find ways to carve out unique niches or offer specialized products.
The changes could have mixed outcomes for builders and contractors. On one hand, larger companies offer better supply chain reliability and access to innovative materials. On the other hand, the lack of competition could drive material prices up, making project budgeting more challenging.
But the real people paying the price will be the homeowners and consumers. Fewer competitors in the market will lead to fewer choices and higher lumber prices, impacting the affordability of home improvements or new construction.
Bottom line
Staying informed is the best way to prepare for this future. Builders and contractors should explore partnerships with multiple suppliers to reduce their reliance on a single source. Small businesses can focus on differentiating themselves through exceptional service or niche offerings. And consumers should know how these changes influence the cost and availability of materials for their projects. The industry is changing, but those who adapt will find ways to thrive.
If you found this article helpful and want to stay ahead of changes in the lumber industry, subscribe to our newsletter. You’ll get access to the latest insights, updates, and expert advice delivered directly to your inbox.