Women continue to break barriers in the construction industry, stepping into leadership roles and running successful companies in a field traditionally dominated by men. From overseeing major infrastructure projects to managing design-build firms, female contractors are proving their expertise and driving change. Robin Thorne of CTI Environmental and Jean Bjork of Bjork Construction are just two examples of female-owned construction companies in North America.
Why more women are joining construction companies
The construction industry is seeing a surge in female representation across all levels. From managing job sites to running their own companies, more women are finding rewarding careers in construction. This increase reflects ongoing efforts to break stereotypes and promote diversity in traditionally male-dominated sectors.
According to the U.S. Bureau of Labor Statistics, the percentage of women in construction rose from 9.9% in 2018 to 11% in 2023. Even more encouraging, women now hold over 13% of executive-level positions in construction companies. Organizations like the National Association of Women in Construction (NAWIC) and Women Construction Owners & Executives (WCOE) have been pivotal in providing mentorship and support. As more women gain visibility and influence in the field, it inspires the next generation to pursue careers in construction.
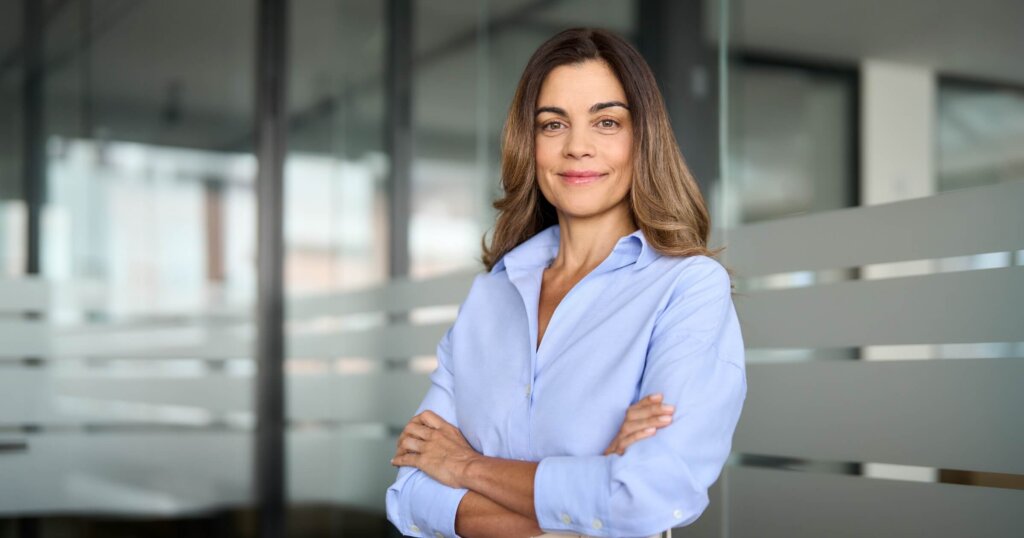
15 women-owned construction companies in North America
1. Robin Thorne: CTI Environmental
CTI Environmental delivers expert environmental consulting services, focusing on hazardous materials management, site assessments, and regulatory compliance. Robin Thorne, a chemical engineer and entrepreneur, identified a critical need for safer environmental solutions and founded the company to address that gap. Her emphasis on technical expertise and innovative practices has earned CTI Environmental a strong reputation in a competitive industry.
Robin’s dedication to diversity in the trades inspired her to create the DemoChicks initiative. This initiative introduces young women to careers in construction and STEM. She believes that exposing young minds to real-world opportunities can open doors to fulfilling careers in male-dominated fields.
2. Jean Bjork: Bjork Construction
Bjork Construction, a prominent general contracting firm in Northern California, specializes in commercial construction, tenant improvements, and building modernization. Jean Bjork took the reins from her father and transformed the company into a thriving business known for precision and client satisfaction. With a focus on expanding services, she established lasting partnerships with major tech companies and commercial developers.
Jean’s advocacy for women in construction extends beyond her own success. She actively mentors aspiring female contractors and fosters a culture of inclusion. She also speaks at industry events, sharing insights on navigating challenges in a traditionally male-dominated field.
3. Sheryl Palmer: Taylor Morrison
Taylor Morrison has become one of the largest women-owned construction companies in the United States. The company is recognized for offering personalized home designs tailored to modern lifestyles. Since becoming CEO in 2007, Sheryl Palmer has propelled the company forward by emphasizing customer satisfaction and integrating sustainable, energy-efficient designs into their homes. Her leadership has driven revenue growth and transformed Taylor Morrison into a brand synonymous with quality and innovation. Her focus on innovation has allowed Taylor Morrison to maintain a competitive edge in the housing market.
4. Guiomar Obregon: Precision 2000 Inc.
Precision 2000 Inc. (P2K), based in Atlanta, Georgia, delivers high-quality civil infrastructure and general contracting services, including airport improvements, facility renovations, and site development. Guiomar Obregon, a civil engineer and co-founder, leveraged her technical expertise to secure contracts with notable clients like the City of Atlanta and Hartsfield-Jackson Atlanta International Airport. Her ability to manage large-scale infrastructure projects with precision has been a driving force behind P2K’s success.
5. Angela Cacace: A. Marie Design Build
A. Marie Design Build, a North Carolina-based firm, blends residential remodeling with custom renovation services. Angela Cacace, a licensed contractor and award-winning designer, established the company to merge her love for construction and interior design. Her ability to create functional, visually stunning spaces has gained her a loyal clientele and industry recognition. From luxury kitchen remodels to intricate home additions, Angela’s attention to detail and focus on quality craftsmanship consistently exceed client expectations.
Angela’s passion for diversifying the trades inspired her to launch the Move Over Bob initiative, encouraging more women to pursue careers in construction. She frequently hosts workshops and speaking engagements to demystify the industry for aspiring female contractors.
6. Rachel Street: The Street Group
The Street Group, led by Rachel Street, focuses on real estate development, renovation, and historic property restoration in Philadelphia. A licensed contractor and realtor, Rachel combines her expertise in architecture and community revitalization to transform neglected properties into vibrant, functional spaces. Her work gained national attention through DIY Network’s “Philly Revival,” where she showcased her ability to breathe new life into historic homes. Rachel’s commitment to preserving the architectural heritage of Philadelphia while incorporating modern functionality has made her a respected figure in the real estate and renovation sectors.
7. Patricia Zugibe: Holt Construction
Holt Construction, a century-old firm, delivers construction management services across sectors such as healthcare, aviation, and hospitality. As the company’s first female CEO, Patricia Zugibe leverages her expertise in construction law and project management to navigate complex projects and maintain the firm’s reputation for excellence. She has successfully overseen multimillion-dollar projects while implementing best practices that ensure operational efficiency and client satisfaction.
8. Jennifer Todd: LMS General Contractors
LMS General Contractors, headquartered in Florida, excels in demolition, abatement, and disaster response. Jennifer Todd, founder and president of this female-owned construction company, is a recognized industry leader known for her ability to manage high-risk projects with precision. Her deep knowledge of hazardous materials and commitment to safety has been a cornerstone of LMS’s reputation for excellence. Jennifer’s experience in navigating complex regulatory environments has allowed the company to expand its services nationwide.
Jennifer’s emphasis on safety, quality, and community engagement has earned LMS General Contractors a reputation as a trusted partner across the country. Her contributions to workforce development have left a lasting impact on the industry.
9. Kathryn Cahill Thompson: Cahill Contractors
Cahill Contractors, a San Francisco-based firm, specializes in commercial and residential construction with a strong focus on sustainable building practices. As a third-generation leader, Kathryn Cahill Thompson has expanded the company’s portfolio to include LEED-certified projects and environmentally conscious designs. Her leadership has guided Cahill Contractors through the integration of cutting-edge technologies and sustainable construction methods, ensuring the firm remains ahead of industry trends.
10. Jane Kaplan Peck: Kaplan Construction
Kaplan Construction, a woman-owned construction company in Boston, provides general contracting and design-build services for healthcare, commercial, and institutional projects. Jane Kaplan Peck has expanded the company’s reach while maintaining its reputation for collaborative, client-focused work. Her leadership has driven the adoption of innovative building techniques, allowing Kaplan Construction to deliver projects that exceed client expectations.
11. Rita Brown: Brown Construction Collective
Brown Construction Collective, a consulting firm specializing in project management, diversity consulting, and community outreach, was founded by industry leader Rita Brown. Her extensive experience on high-profile projects, combined with her commitment to advocacy, has positioned her firm as a catalyst for meaningful change. Rita’s approach involves integrating diversity best practices into every phase of project management, ensuring that inclusivity becomes a standard across the industry.
12. Marilyn Grabowski: Atlantic Infra
Meet Marilyn Grabowski, the dynamic President of Atlantic Infra, a Certified Woman Business Enterprise based in Wall Township, New Jersey. Inspired by her grandmother’s legacy in homebuilding, Grabowski leads four female-owned construction companies under the Atlantic Infra banner, all dedicated to supporting the utility industry across the state. Known as the “Lady in Red,” her company’s bold red branding—from uniforms to fleet—has become a symbol of excellence and reliability. With a background in chemistry and pharmaceutical sales, Grabowski combines technical expertise with a sharp business sense, all while mentoring the next generation of entrepreneurs and serving on multiple industry boards.
13. Jannette J. Yates: Yates Construction
Yates Construction, a prominent firm in Mississippi, specializes in commercial and industrial construction. Jannette J. Yates, an expert in project management and business operations, has been a key driver in the company’s growth since joining the leadership team. Her strategic vision and ability to oversee large-scale projects have solidified Yates Construction’s reputation for delivering quality work on time and within budget.
14. Mel Baiser & Kate Stephenson: HELM Construction Solutions
HELM Construction Solutions, based in Vermont, is a mission-driven company that provides consulting, project management, and training services to support sustainable building practices. Co-owners Mel Baiser and Kate Stephenson are passionate advocates for high-performance building and advancing equity in the construction industry. HELM works with builders, architects, and organizations to implement climate-conscious solutions and improve operational efficiency.
15. Anna Mehr: Milidaro
Milidaro is a woman-owned and led construction company based in Pacoima, California, dedicated to delivering high-quality construction services with a focus on innovation and sustainability. Their services include post-production construction, soundproofing solutions, green building practices, general contracting, and wet utility installation. They’ve worked on local business home improvements, municipality contracts, and even large scale electrical and solar array government projects.
Best states for women in construction
Several states provide strong support systems for female contractors and entrepreneurs. These states not only have higher percentages of women in construction but also offer resources and networks that promote success.
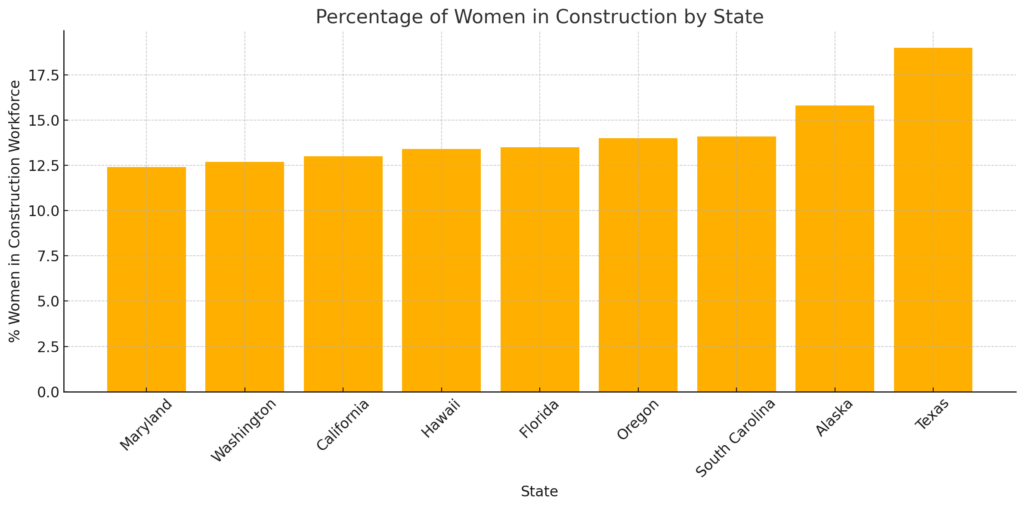
- Texas – With 19% of the construction workforce being female, Texas is the clear leader amongst all states.
- Alaska: Women comprise 15.8% of Alaska’s construction workforce giving it the second most in the United States.
- South Carolina: Women represent 14.1% of the construction workforce in South Carolina.
- Oregon: In Oregon, women make up 14.0% of the construction workforce.
- Florida: With 13.5% female participation, Florida’s construction industry benefits from programs encouraging entrepreneurship among women.
- Hawaii: Women account for 13.4% of Hawaii’s construction workforce.
- California – Women make up 13% of the construction workforce, with strong support from organizations like NAWIC and WCOE.
- Washington: In Washington State, women represent 12.7% of the construction workforce.
- Maryland: Maryland’s construction industry includes 12.4% women.
These states not only have higher percentages of women in construction but also offer resources and networks that promote success for female-owned construction companies.
Final thoughts
The construction industry has been traditionally dominated by men, but these remarkable women are breaking barriers, leading successful businesses, and advocating for greater diversity within the field. The contributions of these trailblazing women will continue to shape the industry for years to come, offering new paths to success and redefining what it means to be a leader in construction.
If you’re interested in reading more about the changing face of construction, subscribe to Under the Hard Hat’s newsletter to stay informed.