Adaptive reuse is an architectural design principle that focuses on repurposing existing buildings for new uses while maintaining the existing historic and architectural features. Taking on an adaptive reuse project helps preserve cultural heritage, slow urban sprawl, reduce construction costs, and optimize building energy consumption.
What is adaptive reuse?
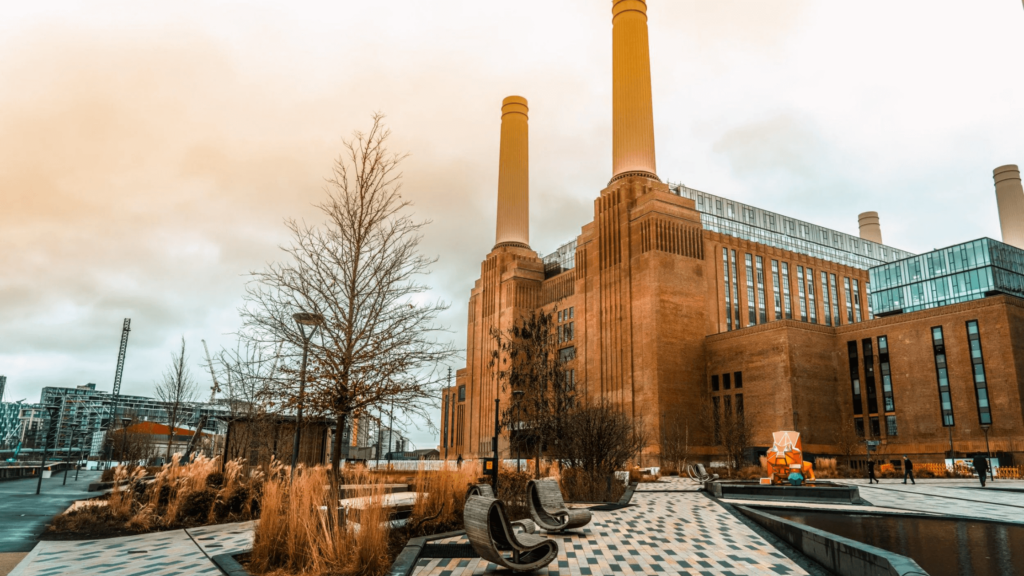
Walking through any city, you’ll find dozens, sometimes hundreds, of old, abandoned, and vacant buildings. A growing architectural approach called “adaptive reuse” paves the way for new life from old, empty historic buildings.
The adaptive reuse design principle repurposes existing buildings that have outlived their original purpose. The main goal is to preserve the buildings’ natural architectural and historic features while transforming them and giving them a new purpose and life.
You’ll see this often—old churches or industrial buildings turned into ultra-modern lofts or an old abandoned warehouse converted into a shopping center or mixed-use venue.
Put simply, adaptive reuse breathes new life into old historic structures by transforming them into something useful for the surrounding area.
Commercial developers usually tackle these projects because they have the financial means and construction expertise to complete them successfully.
4 reasons why developers should adopt adaptive reuse
1. Maintains historic and cultural heritage
Most cities are plentiful with historic buildings, and one of the main goals of adaptive reuse is to preserve that history. It restores culturally significant buildings and sites that would otherwise be demolished for new buildings or left to decay.
2. Slows urban sprawl
Urban sprawl—unrestricted expansion into urban areas—is happening everywhere. It occurs when builders must expand outside city limits to find new construction sites. And while new infrastructure is key to growth, urban sprawl is a huge contributor to air pollution and significantly impacts the environment, traffic patterns, and infrastructure costs. Adaptive reuse is one of the easiest ways to counter urban sprawl.
3. Reduces construction costs
Adaptive reuse projects are often less costly than starting new from the ground up. Plus, it’s also more sustainable and time efficient since companies avoid the legal, regulatory, and political challenges of demolition projects.
4. Optimizes energy consumption
When repurposing old buildings, contractors can implement energy-efficient and sustainable practices, such as environmentally friendly heating, ventilation, and air conditioning (HVAC) systems that help increase energy efficiency and reduce running costs.
5 types of adaptive reuse
1. Facade
Facadism is a type of adaptive reuse that preserves the building’s facade (the front part or exterior) while demolishing most of the remaining building. This process is called a facadectomy—it preserves the streetscape view but updates the bulk of the building. However, this type of adaptive reuse can be pricey since the historic (and fragile) exterior must be supported and protected during construction.
2. Integration
In an integration, an existing historic structure is built within an entirely new structure—it’s ‘integrated’ into a new building, allowing the original building to be preserved while enclosed in a new site. One of the best examples of integration is Denmark’s Jægersborg Water Tower, which now stands as student housing.
3. Renovation
Adaptive reuse naturally implies some semblance of renovation, but while renovation generally involves repairing and refinishing but preserving the building’s original purpose, renovation in adaptive reuse implies transforming the building’s use. Put simply, renovation replaces elements of a historical building that are in poor condition but maintain their core structure and appearance.
4. Infrastructure
Adaptive reuse isn’t limited to just historical buildings—it can also be applied to infrastructure, such as bridges, viaducts, and grain silos. Many adaptive reuse projects transform outdated or unused infrastructure into parts of a community.
5. Historic preservation
Adaptive reuse and historic preservation preserve a building’s integrity and history but take different approaches. Adaptive reuse repurposes an old building or site for a new use—a compromise between preserving and demolishing. On the other hand, historic preservation maintains the building’s existing form, integrity, and materials without integrating new materials, additions, or structural alterations. That said, minimally invasive procedures, like mechanical, electrical, and plumbing (MEP) upgrades required to meet new building codes, are typically allowed, according to standards published by the National Park Service.
Put simply, adaptive reuse offers the flexibility to use new, more efficient architectural materials while paying homage to the building or structure’s history.
Cool adaptive reuse projects across North America
The High Line, New York City, New York
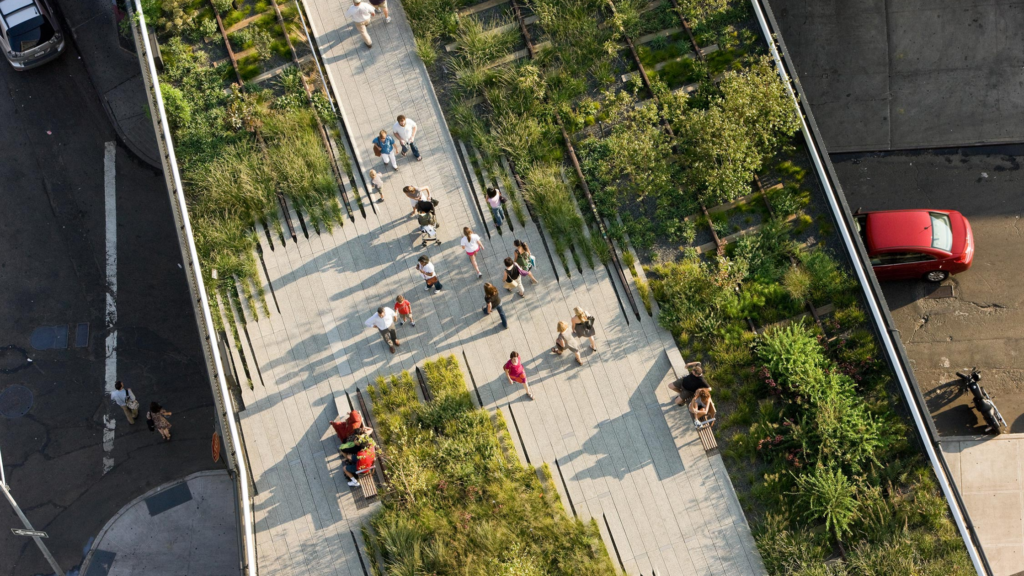
The High Line in New York City is one of the most well-known adaptive reuse projects—and a fantastic example of adaptive reuse isn’t relegated to just buildings. Opened in 1934, the High Line railway enabled the transportation of food items, but it became inoperable in the 80s with the rise of transport trucks. After decades of disuse, Joshua David and Robert Hammond founded Friends of the High Line, a non-profit conservancy, to advocate for preserving and reusing the High Line as a public space. Transformed by landscape architecture firm James Corner Field Operations, design studio Diller Scofidio + Renfro, and planting designer Piet Oudolf, the High Line now operates as a public park.
Ghirardelli Square, San Francisco, California
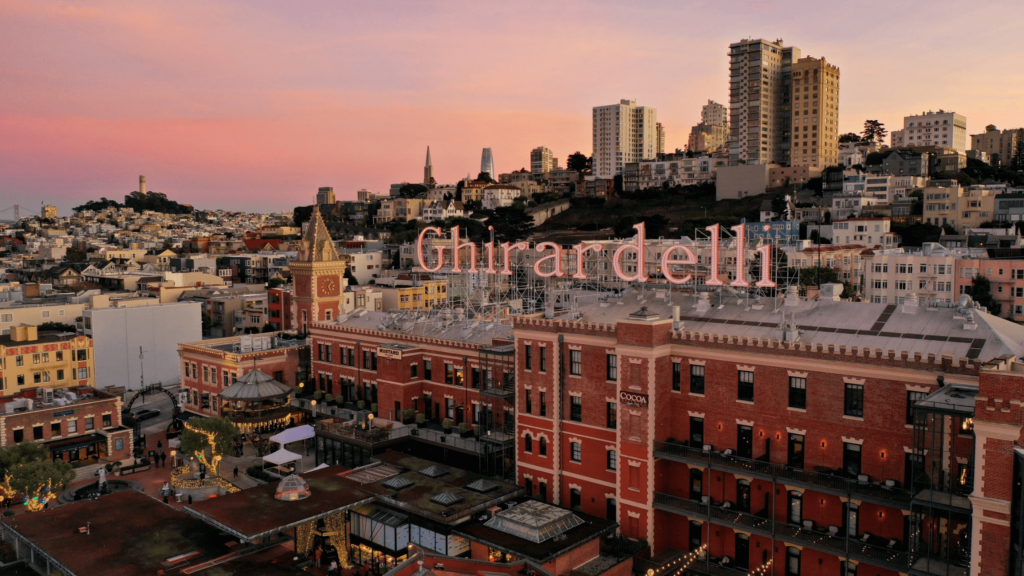
Ghirardelli Square was originally a chocolate factory established by Domenico “Domingo” Ghirardelli in the mid-1800s. The company was sold in the 1960s and transferred to San Leandro. Fearing the building might be demolished, a group of San Franciscans purchased it and repurposed it into a mixed-use complex featuring shops and restaurants. It officially opened on November 29, 1964.
Low-carbon community, Blatchford, Alberta
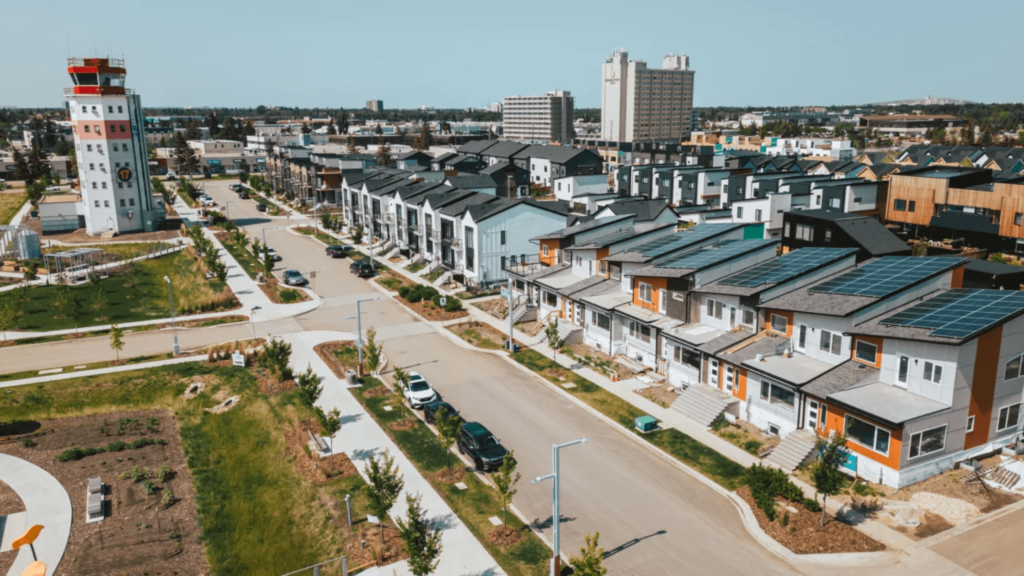
Edmonton’s City Centre Airport, which functioned as Canada’s first licensed airstrip in 1927, was decommissioned in 2013. The airport’s 217 hectares would be converted into a walkable, densely populated, carbon-neutral development housing 30,000 people. The vision was bold, and the centrally located City Centre Airport land was a blank slate.
The 12 airport buildings were disassembled, and building materials were removed and repurposed for other sites. Any buildings that could not be reused as complete units were recycled in their component parts and sold back to companies—asphalt, concrete, and gravel were sold back to the construction industry and aviation-related fixtures were purchased by an airport undergoing expansion.
Cotton Factory, Hamilton, Ontario
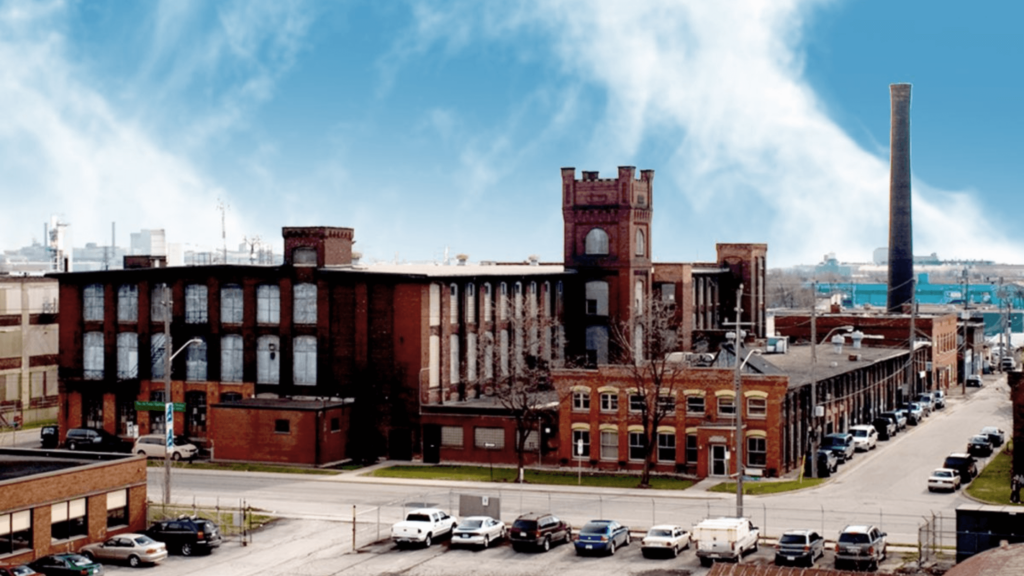
The former site of the Imperial Cotton Co. built in 1900 is a prime example of adaptive reuse. Sitting in the heart of lower Hamilton, The Cotton Factory has been transformed, breathing new life into a historic industrial building. It stands as a creative industries complex, offering space for workshops and small manufacturing, office space for creative professionals, and studios for artists.
Monique Corriveau Library, Sainte Foy, Quebec
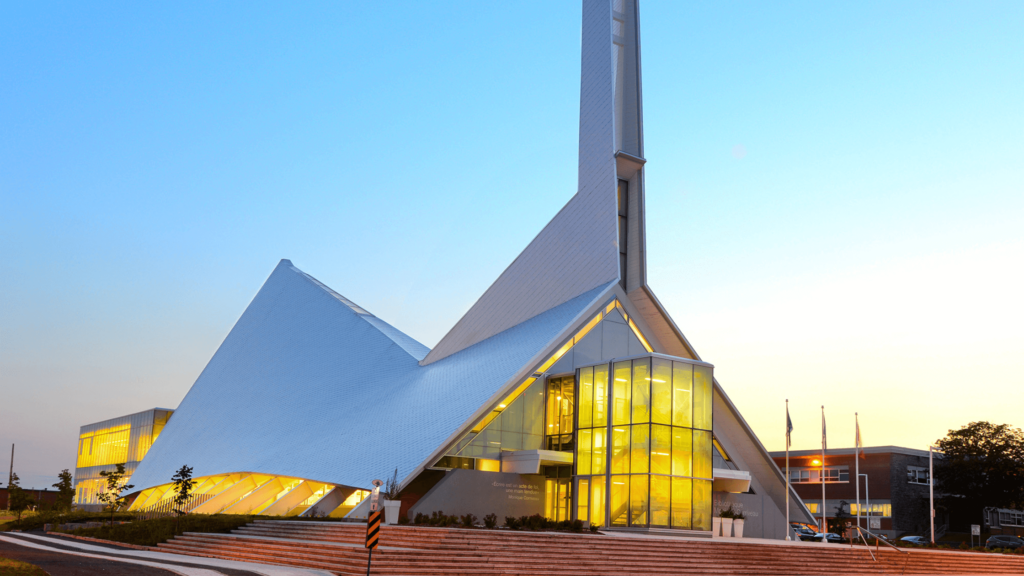
A mid-century modern church, the Saint-Denys-du-Plateau church in Quebec, was given a new life in 2013 and transformed into the Monique Corriveau Library, a modern public library and community center. The church was built in Sainte-Foy in 1964 and was architecturally innovative, even then. Its glass walls between the descending beams formed an open conversation between the congregation inside and the community outside—this prompted its transformation into a public library, a community center, and a cafe. The building was modernized and equipped with the latest technology, but the original structure was left intact.
Roundhouse, Vancouver, British Colombia
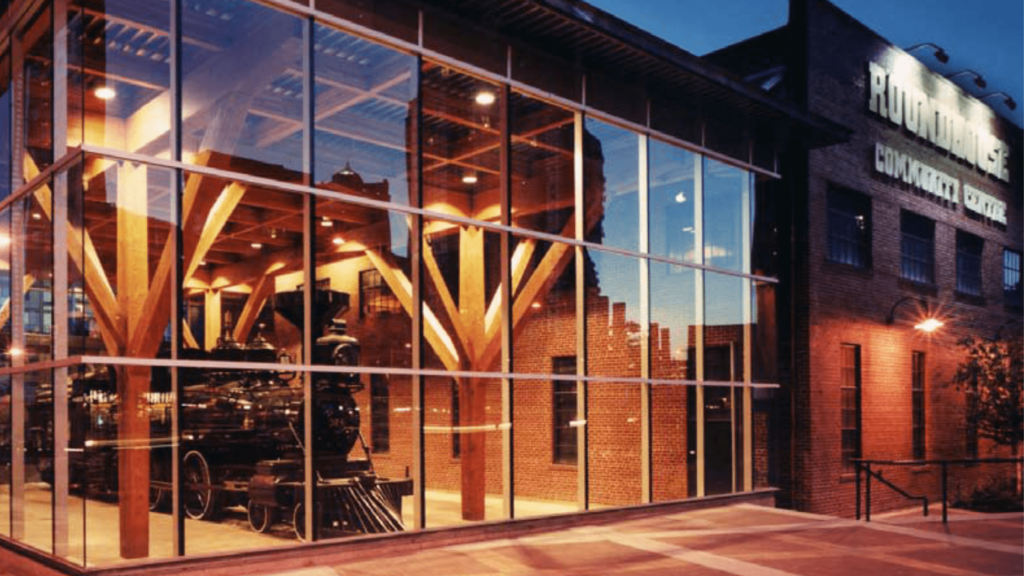
Once the home and service station for great steam locomotives, the Roundhouse is a culturally significant building in the City of Vancouver from an architectural and social perspective. With the rise of diesel-powered engines, the once-vibrant building was abandoned and slated for demolition. Given its uncertain fate, Vancouver residents rallied and helped revive the space as a thriving community center. Roundhouse is Vancouver’s oldest heritage building, which remains on its original site.
Montreal Tower, Montreal, Quebec
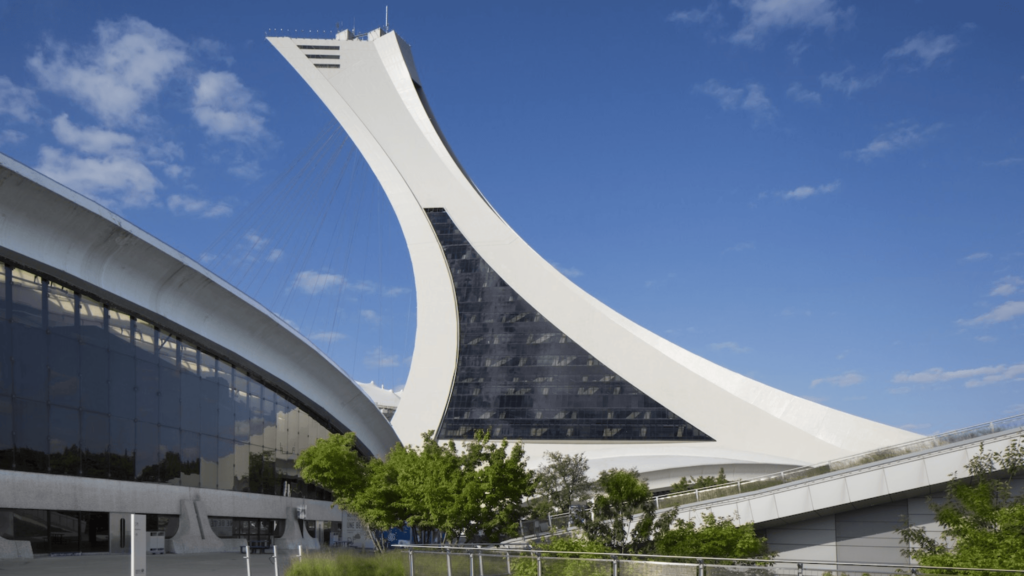
The Olympic Tower has been one of Montreal’s most distinctive landmarks since its completion in 1987. , has finally undergone a renaissance. Initially constructed for the 1976 Montreal Summer Olympic Games, the tower spent most of its post-Olympic years vacant. Renamed the Montreal Tower, this architectural gem was repurposed to house more than 1,000 Desjardins Group employees as a modern office space. The project was extensive and enhanced the existing structure’s architectural features and historic elements.
Evergreen Brick Works, Toronto, Ontario
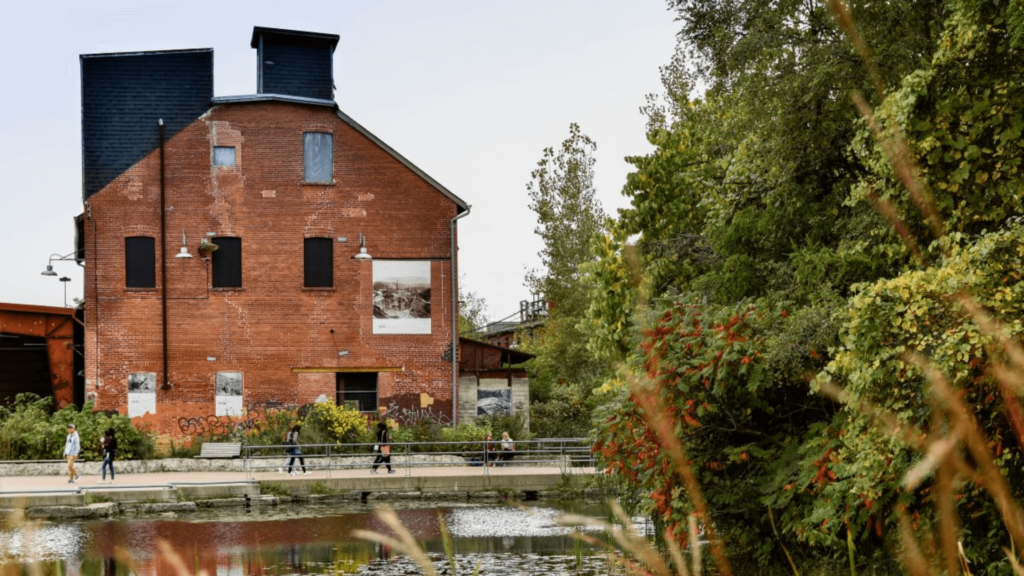
In 2010, Evergreen transformed a collection of 16 deteriorating historical buildings and an adjacent 16-hectare public park in Toronto into a global showcase for green design—collectively, they’re called Evergreen Brick Works, Canada’s first large-scale community environmental center in the heart of Toronto, Canada.
Evergreen Brick Works is open year-round to the public. The site and surrounding trails and ravines see more than 500,000 annual visitors experience its magic—public markets, conferences and events, outdoor learning and nature play opportunities, and public art exhibitions. It’s now a space where people can learn about incorporating regenerative practices into the design of public places to help them heal and grow.
Portland Japanese Garden, Portland, Oregon
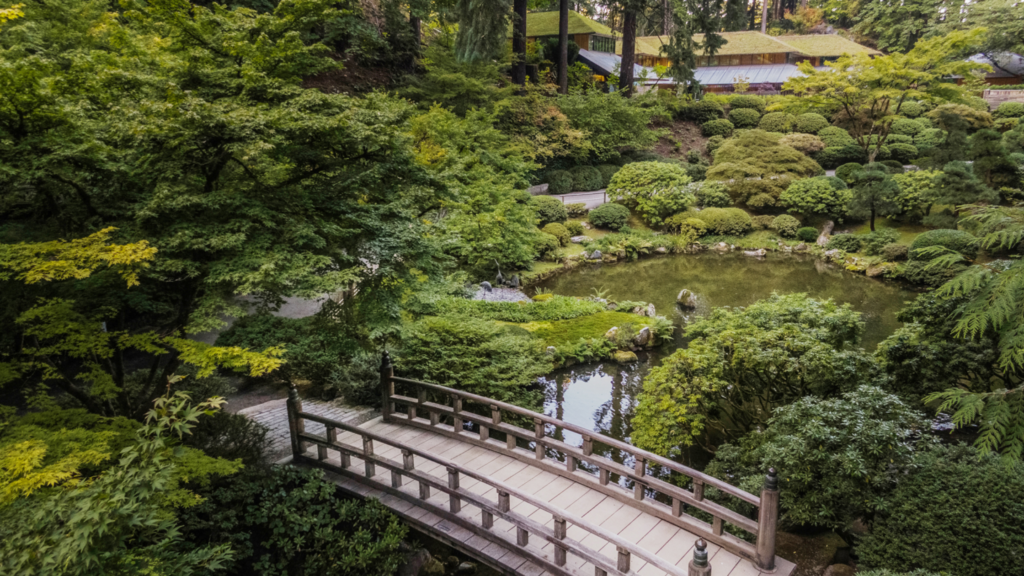
The Portland Japanese Garden is a prime example of the fact that not all adaptive reuse projects focus on transforming interior spaces or historic buildings. Growing cultural ties between Oregon and Japan inspired the gardens. Mayor Terry Schrunk and members of the Portland community came up with the idea to build a Japanese garden on the site of the old zoo in Washington Park. The park served two purposes: it provided the citizens of Portland with a garden of incredible beauty and serenity. It forged a healing connection to Japan on the heels of World War II. It enabled Americans to experience firsthand Japanese ideals and values communicated solely through nature.
Union Station, Denver, Colorado
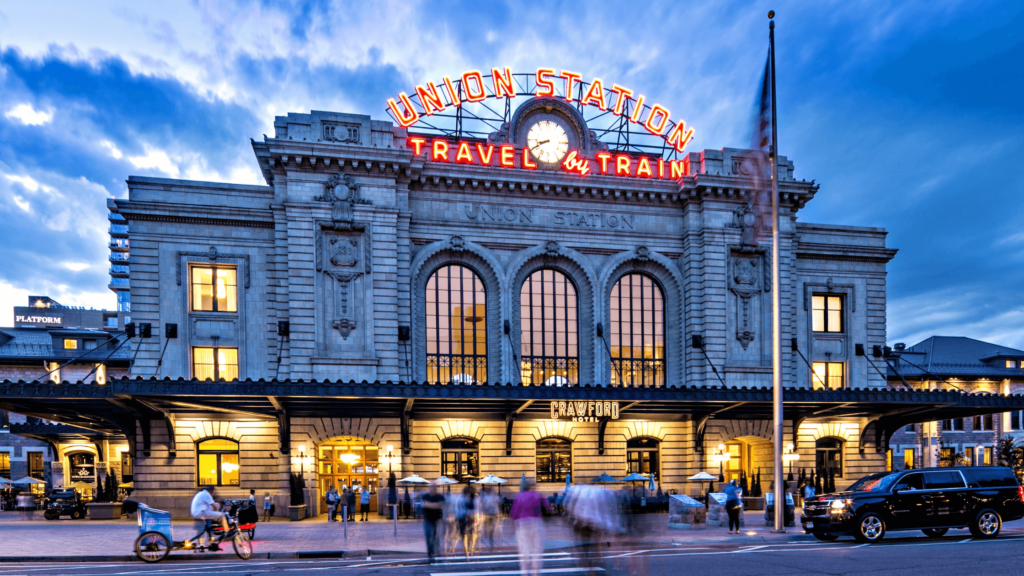
Train stations across America showcase some of the country’s grandest architectural works. Denver’s Union Station opened its doors in 1881 and was the gateway to the growing city. It spanned 500 feet and was adorned with a 180-foot clock tower. At the time, the station was the tallest building in the West. With train travel being phased out by other modes of transportation, the Station gradually fell into disuse. In 2001, efforts began to revitalize the historic landmark, culminating in a grand reopening of the reimagined Denver Union Station—a multi-use complex housing boutique shops, restaurants, and lounges.
The future of construction might be in the past
Adaptive reuse plays an integral role in the redevelopment of cities across the globe. In the best cases, these projects retain timeless architectural features and cultural significance, finding new spaces for people and businesses to gather. But adaptive reuse isn’t just about retaining cultural landmarks—they can also help reduce the environmental impact of construction by reusing existing materials and avoiding demolition and waste.
While not all buildings can be repurposed, contractors and construction companies should consider adaptive reuse to solve building challenges, especially when sites are hard to come by. Abandoned factories and warehouses, old theaters, and neglected office buildings are waiting for someone to see the potential and make them the hottest and most sought-after new venue on the block.