Volumetric concrete mixers, or mobile batch plants, mix concrete directly on-site, allowing crews to control the exact amount and quality needed for each project. Unlike traditional drum mixers that carry pre-mixed concrete, volumetric mixers store the raw materials separately and combine them just before pouring. Controlling material use and disposal can lead to cost savings, greater flexibility, and a higher-quality product in an industry with high waste production. This approach is invaluable in construction, where adaptability and efficiency are crucial.
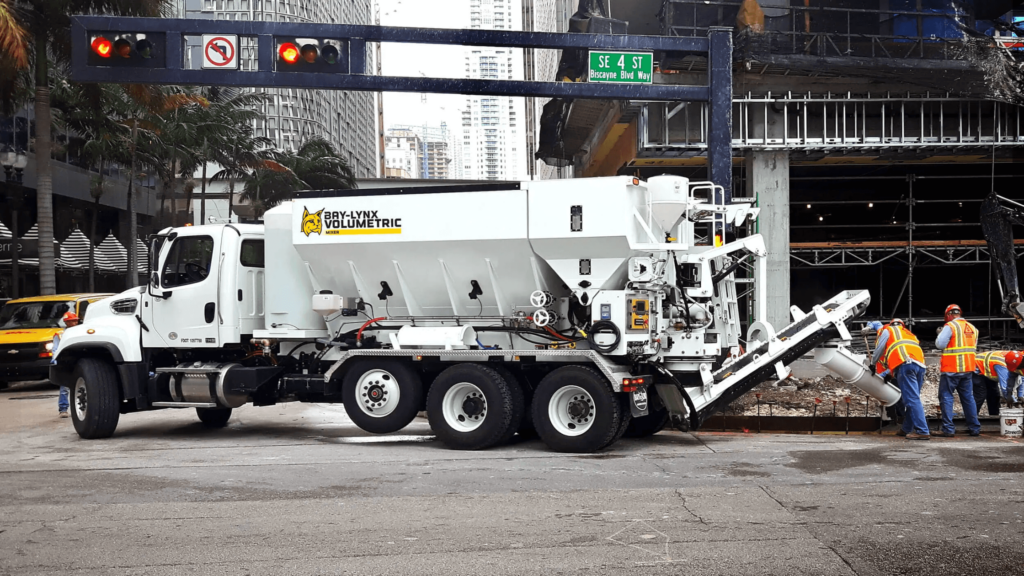
What are the benefits of volumetric mixers?
Precision and control
Volumetric mixers provide exceptional control over the mix design and quantity of concrete. Operators can adjust the proportions of water, cement, and aggregates on-site, which is especially useful for projects with variable specifications or unexpected changes. This precision reduces waste, as only the exact amount needed is produced.
Fresh, consistent concrete
Volumetric mixers ensure the concrete remains fresh by mixing on demand, maintaining its integrity and workability. This helps avoid common quality issues like setting or curing too early, making volumetric mixers ideal for remote locations or projects with extended schedules.
Reduced waste and cost savings
Since volumetric mixers only produce the necessary amount of concrete, there’s minimal leftover waste. This is both environmentally beneficial and cost-effective, eliminating disposal fees and saving materials. Due to the reduced need for extra batches, contractors can be more accurate with project budgets and timelines. It also translates to lower labor costs when concrete delivery is delayed.
Flexibility across diverse projects
These mixers are suited for a range of projects, from minor repairs to large-scale foundations, offering flexibility unmatched by drum mixers. Operators can easily switch between different mixes on the same day, allowing one mixer to cater to multiple jobs.
Challenges of using volumetric mixers
Initial investment
Volumetric mixers are more expensive than traditional drum mixers, which may deter smaller contractors from adopting them. The upfront cost, while eventually offset by long-term savings, is significant, requiring a commitment to training and proper maintenance.
Operator training
Successfully using a volumetric mixer requires well-trained operators who understand how to adjust the mix for different applications. They must also know the mix designs and address any issues that may arise on-site. Skilled operators are essential to fully leveraging the benefits of these mixers.
Maintenance demands
Volumetric mixers require regular maintenance to function optimally. With multiple moving parts and components that handle different materials, these machines can experience wear and tear more frequently. Routine checks and maintenance are crucial to avoiding costly repairs and ensuring long-term productivity.
Why volumetric mixers are a good choice
Volumetric mixers offer a blend of convenience and efficiency that aligns well with the demands of modern construction. The ability to mix on-site means reduced delays, more control over project quality, and adaptability for last-minute changes or unique requirements. Additionally, their environmentally friendly approach aligns with industry efforts toward sustainability, particularly by minimizing waste.
Construction companies using volumetric mixers are setting themselves up for smoother operations, reduced costs, and more satisfied clients. As construction prioritizes adaptability and sustainability, volumetric mixers will likely become a staple on job sites.
To stay updated on more construction-related insights, subscribe to our newsletter at Under the Hard Hat.