Modular and prefabricated homes have come a long way. These structures are built offsite—sometimes up to 90% complete—before being transported and installed onsite. With a wide range of customization options and offsite construction processes that ensure complete quality control from one phase to the next, modular and prefabricated homes represent a sustainable, cost-effective solution to the housing crisis. Discover how companies like Plant Prefab, Villa, Biltwise, Method, and Dvele lead the pre-fabricated home revolution with award-winning homes built faster, stronger, and more sustainably than many of their conventionally constructed counterparts.
5 prefab and modular building companies to watch
1. Plant Prefab
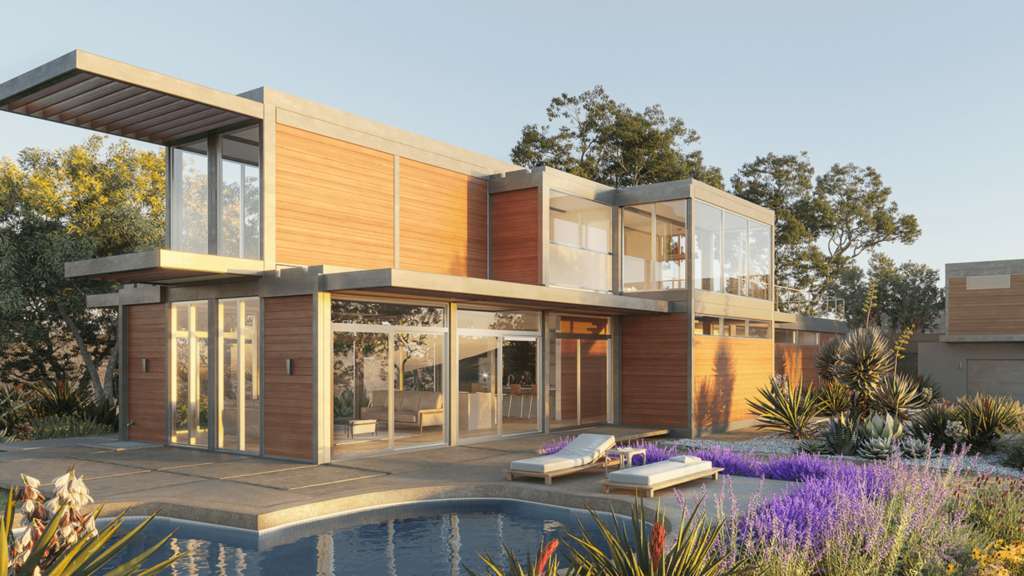
Location: Arvin, California
Website: https://www.plantprefab.com/
Multi-award-winning Plant Prefab in Arvin, California, offers an innovative approach to building prefabricated homes. Using sustainable building practices, Plant Prefab reduces waste by up to 30% compared to traditional construction methods while reducing energy and water use, sourcing recycled materials, and improving indoor air quality.
Plant Prefab uses a hybrid approach to construction, incorporating both modular and panelized components in each build. This approach allows for quick, efficient construction—using their method, construction timelines are reduced by 20-50%—without sacrificing customizability.
In an interview with Under the Hard Hat, former Plant Prefab CEO Steve Glenn explains that this approach sets the company apart from its competitors, “A hybrid approach is better for the design, the budget, and the transportation logistics. Ours is the only facility in the US purpose-built to do both panels and mods with automation.”
2. Villa
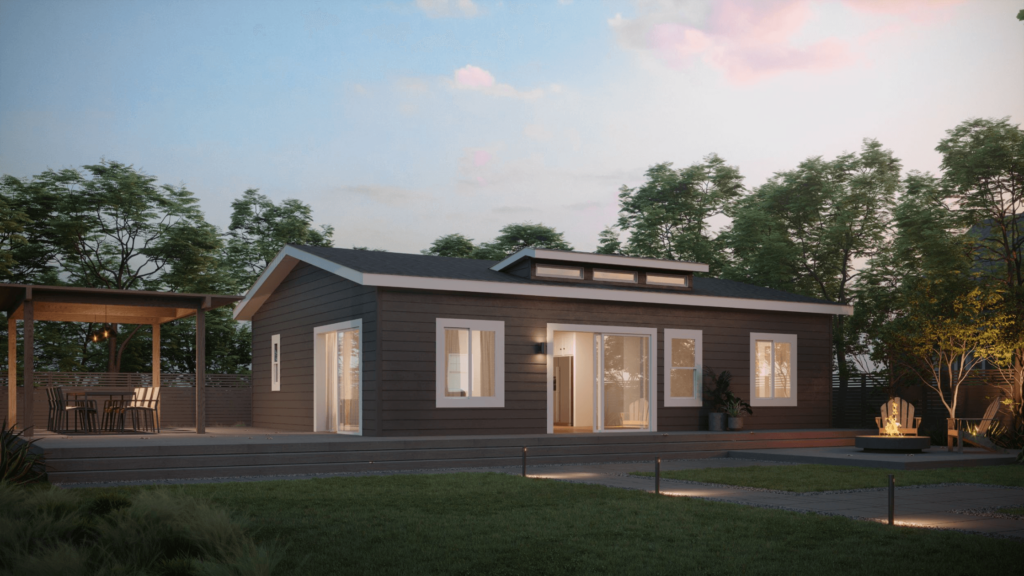
Location: Napa Valley, California
Website: https://villahomes.com/
Villa Homes specializes in accessory dwelling units (ADUs), which are smaller housing units added to existing residential lots, often for use as rental units or in-law suites. ADUs are a powerful tool for reducing the housing crisis, providing detached dwellings on a smaller scale for those who don’t need larger homes.
Villa’s pre-fabricated models range from 400 to 1200 square feet, start at just $106,000, and are completed in under a year. Constructed off-site allows Villa to avoid weather delays, high labor costs, and supply chain bottlenecks, reducing building costs for homebuyers and creating a more efficient building process. Villa’s off-site construction also makes it easier for homeowners to add ADUs to residential lots without enduring a lengthy, disruptive construction process.
3. Biltwise Structures
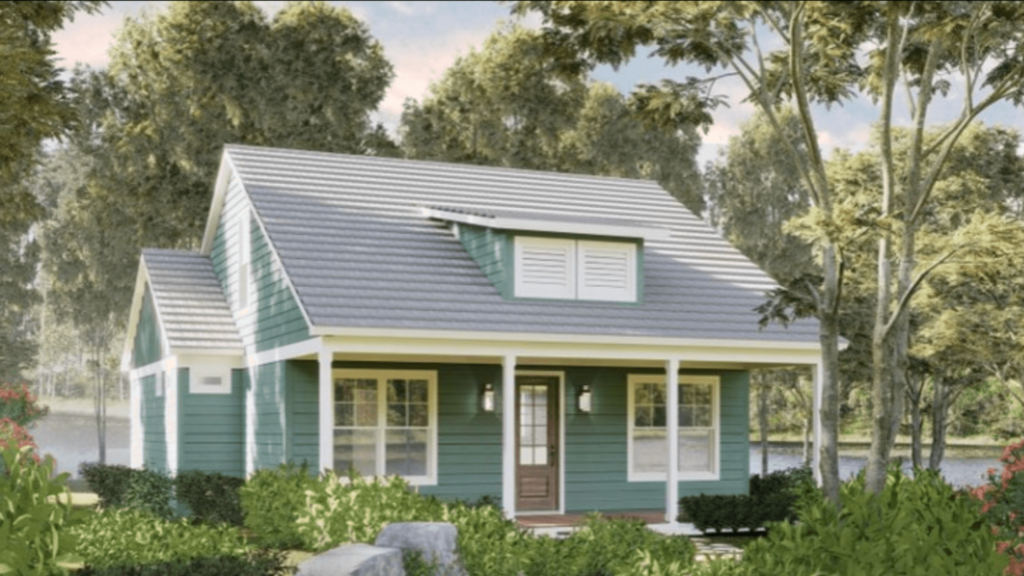
Location: Greenwood, South Carolina
Website: https://biltwisestructures.com/
Biltwise Structures are constructed in an assembly-line style in under 10 days and are 90% complete upon leaving the Biltwise production facility. After undergoing strict quality control checks, the homes are moved to their destination.
Biltwise Structures says its modular homes are stronger than those made with conventional construction methods because they’re constructed in a climate-controlled factory. Each structure must withstand being transported to its build sites and installed with cranes.
Their approach is also incredibly scalable due to the centralized nature of construction and shortened build times. The Biltwise factory in Greenwood, South Carolina, is 240,000 square feet and capable of constructing over 500 homes yearly, while their 75,000 square foot Colorado factory can create upwards of 700.
4. Method Homes
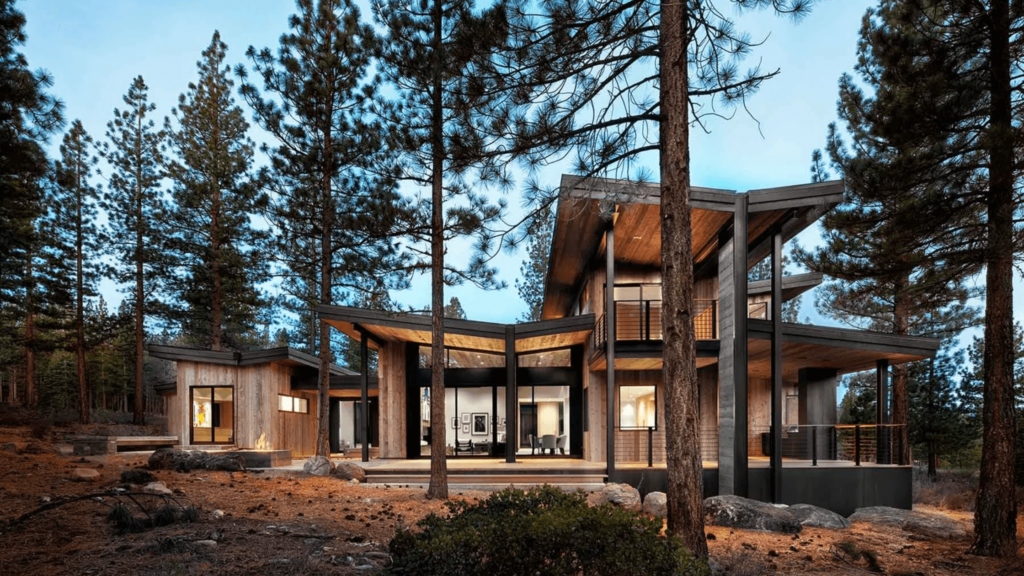
Location: Seattle, Washington
Website: https://methodhomes.net/
Method Homes constructs residential and commercial modular homes with a clean, modern look, servicing most of the western United States and some areas of British Columbia, Canada. This Seattle-based company focuses on sustainable designs, offering the ability to build structures that meet environmental certification standards like LEED, ENERGY STAR, Living Building Challenge, and Passive House. Method Homes says that by building off-site, construction waste is reduced to less than 10%, compared to the 30% of building materials wasted with conventional construction methods.
Even when it comes to custom homes, Method Homes’ offsite construction process significantly reduces the build time. Custom home options are typically built within 20 weeks and fully installed on-site in just four months. Method offers dozens of predesigned options, too, from coastal cabins to sleek city residences.
5. Dvele
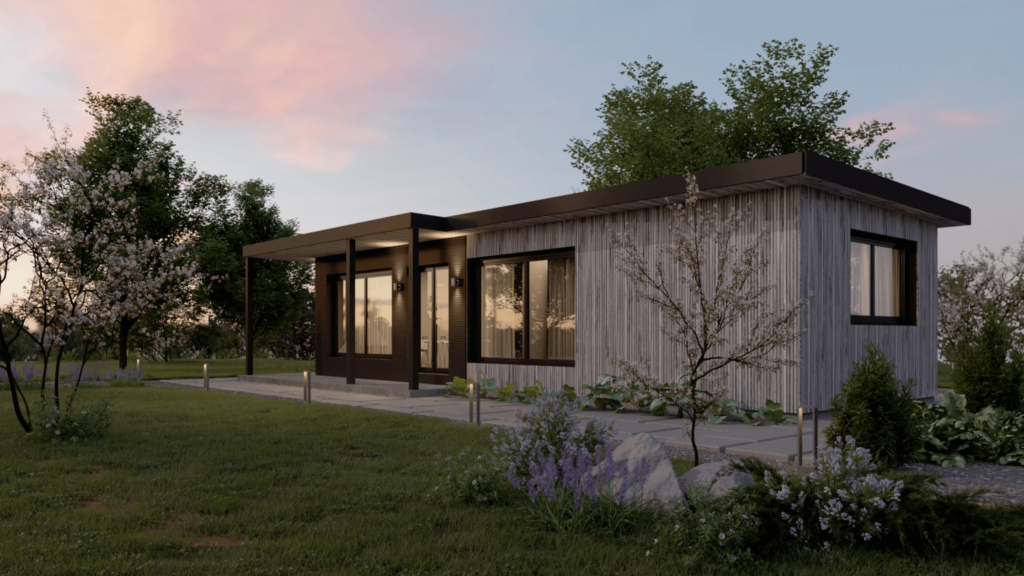
Location: La Jolla, California
Website: https://www.dvele.com/blu-homes/modern-modular-homes
Founded in 2018, Dvele is a modular homebuilder headquartered in La Jolla, California. Dvele specializes in mass-producing homes to “create a healthy living environment, heal the planet, and decrease the cost of homeownership.”
The Dvele website boasts that its homes can be up to 84% more energy efficient than homes built with traditional methods and 20% more efficient than Passive House standards. Coupled with construction timelines 80% shorter than conventional builds, Dvele offers stunning designs with significant advantages.
Dvele also goes beyond waste reduction and energy efficiency, creating “healthy homes” that feature biophilic design, air and water filters to remove environmental pollution, and over 120 sensors in each home to monitor factors like air quality and ventilation. Dvele homes also produce and store clean energy via solar panels and batteries, making homes energy-independent and reducing long-term operating costs.
Why modular or prefab?
Modular and prefabricated homes have gained popularity due to their speed of construction, cost savings, and offsite construction process, which reduces waste and centralizes resources.
To explain the wisdom of prefabricated construction, Texas-based ReMo Homes says, “Consider this scenario: Whenever you order a Tesla Model 3, Elon Musk brings the parts to your front yard and starts assembling them there. Isn’t this absurd? This is what’s happening in the construction industry.”
Modular and prefabricated homes are a realistic way of mitigating the housing crisis. They offer homes with lower construction costs, shorter build timelines, and a more sustainable approach to what is typically an incredibly wasteful industry.
Modular and prefabricated homes offer a host of benefits to both construction companies and homeowners, including:
- Cost savings
- Waste reduction
- Sustainable construction
- Shorter build timelines
- Minimal disruption compared to on-site construction
These benefits used to come at the cost of aesthetics, customization, and curb appeal—pre-fab options were few and far between, leaving homeowners to choose from a scant few cookie-cutter options. Now, with companies like Method and Villa, homeowners can have the best of both worlds: the speed, cost, and efficiency of modular and prefabricated homes, with award-winning architectural designs and seemingly endless customization options of traditional builds.
Bottom line
Modular and prefabricated homes are reshaping the construction landscape, offering innovative solutions to the challenges of more traditional building methods. Companies like Plant Prefab, Villa, Biltwise, Method Homes, and Dvele excel at creating sustainable, efficient, and customizable housing. With reduced waste, shorter timelines, and lower costs, prefabricated and modular homes address the housing crisis while delivering cutting-edge designs and environmental benefits. As the industry continues to evolve, modular and prefab homes are proving that homeowners no longer need to compromise on style or quality to enjoy the benefits of modern, efficient construction.
Like this and want more content like it? Subscribe to our weekly newsletter and follow us on social media for the inside scoop on the latest companies moving towards sustainable building.