Mondays can feel tough for everyone, but they bring more than just the start-of-the-week blues in the construction industry. They also increase the chance of getting injured on the job, a phenomenon known as the “Monday effect.” This concerning trend leaves companies scrambling to cover the work, decreases productivity, and often results in costly compensation claims.
The reality of the construction industry
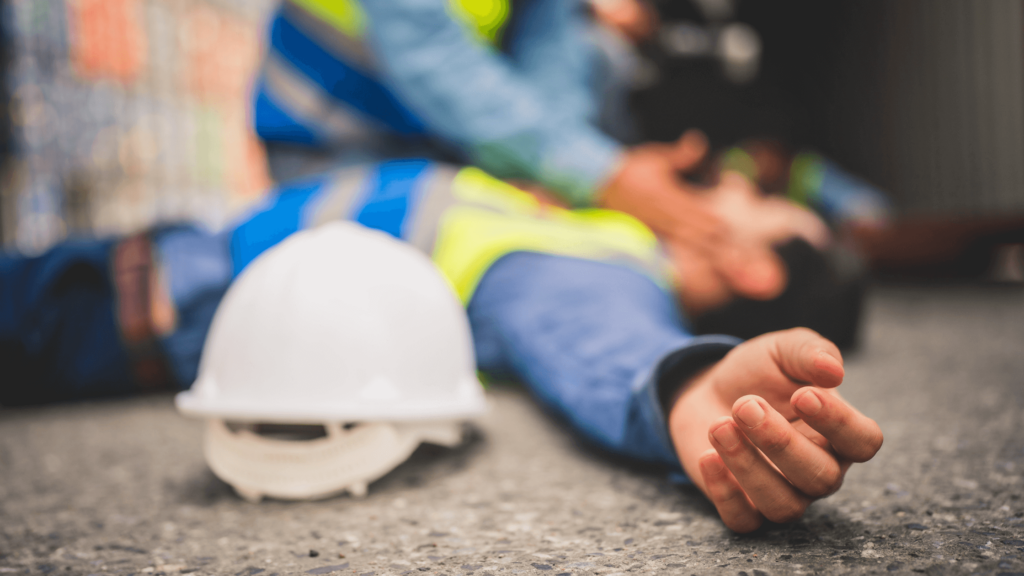
Construction sites are among the most hazardous workplaces, with accidents occurring almost daily and in an instant; workers constantly face falling objects, heavy machinery, and dangerous materials. In 2022, the construction industry accounted for nearly 20% of all workplace fatalities in the United States despite employing only about 7.5% of the workforce.
This disparity shows the value of safety in the industry. While many companies have safety procedures, they often fall short of protecting workers. Accidents carry major financial burdens beyond the human toll. Fatal construction injuries are estimated to cost the United States $5 billion each year, considering healthcare expenses, lost income, reduced quality of life for families, and lost production. Therefore, addressing workplace risks in construction has benefits beyond just life and profits. It helps society as a whole be more productive.
The ‘Monday effect’
The “Monday effect” is a well-documented phenomenon that reveals a spike in workplace injuries at the start of the workweek. For construction workers, this trend has profound implications. Several reports from various countries, including Canada, Spain, and Australia, show that more injuries are reported on Mondays than on other days. For example, a study in Australia found that 23.6% of weekday work injury claims occur on Mondays. This pattern is especially concerning in the construction industry, where physical labor and high-risk activities constantly challenge safety.
The most common injuries sustained are back injuries and wrist sprains, according to a report from Ontario. In addition, from Monday onwards, a study has shown that injury frequency decreases by 29.4% from Monday to Friday, also known as the “Weekday Effect.” The largest decrease occurs from Monday to Tuesday, with 14.3% less chance of injury. These findings indicate that a better job needs to be done regarding safety on construction sites on Mondays. Recognizing this trend as a real threat to worker safety will help companies create strategies that mitigate injuries and keep workers safe.
Why Mondays?
Several factors contribute to this increased risk. One major issue is the impact of poor sleep quality on Sunday nights. Many workers go to bed late after the weekend, leading to insufficient rest and “cognitive failure,” which can result in errors on the job. Additionally, Mondays often mark the beginning of new tasks or projects, introducing unfamiliar risks that workers may not yet be prepared for. Another factor is the change in site conditions over the weekend. Weather, for example, can cause unexpected hazards; strong winds may shift scaffolding or unsecured materials, creating dangerous scenarios for crews returning to work.
Addressing the root causes is key to preventing accidents
Workplace injuries, especially in high-risk industries like construction, rarely occur in isolation. They’re often the result of a combination of factors that create unsafe working conditions. Identifying and addressing these root causes will help to reduce accidents and protect workers.
Here are some of the top causes of accidents in the construction industry:
- Labor shortages: A limited workforce often means employees are overworked, leading to fatigue, mistakes, and unsafe practices.
- Pressure to meet deadlines: Tight project timelines can push workers and management to cut corners, skip safety checks, or rush tasks.
- Poor risk assessments: Failure to identify specific hazards on construction sites leaves workers unprepared and vulnerable to preventable accidents.
- Communication issues: Miscommunication, unclear instructions, or language barriers can result in unsafe actions and misunderstandings.
- Inadequate training and resources: Workers without proper safety training or access to essential tools are more likely to face dangerous situations.
Strategies to reduce worker injury
Workplace injuries risk employees’ health and livelihoods and create significant challenges for companies. The ripple effects of accidents can severely impact a business’s operations and reputation, from costly compensation claims to project delays and strained employee morale. For construction companies, taking proactive steps to reduce injuries will maintain a reliable and productive workforce, help meet project deadlines, and ensure long-term growth.
Here are some strategies to consider implementing into your construction business.
- Invest in safety training: Workers who know how to identify hazards, use equipment properly, and follow safety protocols are far less likely to be injured, helping to keep projects on track and reduce downtime.
- Improve communication: Miscommunication or unclear instructions can lead to mistakes that cause injuries. Establishing clear channels for updates and hazard reporting ensures that workers and supervisors are always on the same page.
- Conduct thorough risk assessments: Job sites change constantly, and failing to evaluate risks can lead to preventable accidents. Regular inspections allow companies to address hazards before they become incidents.
- Enforce adequate rest periods: Fatigue is a leading cause of workplace mistakes. Companies can improve focus and reduce errors by ensuring workers have regular breaks, ultimately saving time and costs.
- Provide proper equipment: Outdated or inadequate tools and gear put workers at risk. Supplying up-to-date, high-quality equipment helps workers perform their tasks safely and efficiently.
- Foster a safety-first culture: A strong safety culture encourages employees to prioritize their well-being over shortcuts. Recognizing and rewarding safe practices helps instill this mindset across the team.
When companies invest in these measures, they protect their employees and minimize injury costs. They also avoid costly project delays while building trust within their workforce to take safety seriously.
Bottom line
Injuries and accidents in construction don’t have to be inevitable. By understanding trends like the “Monday effect” and addressing unsafe working conditions, you can protect your workers, reduce costs, and build a stronger team. Prioritizing safety is more than just a stat on the board—it’s about every individual’s quality of life and ensuring they feel valued, protected, and supported.
Want the resources to keep your team safe? Take the next step to safer worksites and a stronger team by subscribing to our newsletter. You’ll get immediate access to practical safety guides, proven strategies, and expert tips to support your safety strategy.
1 comment