August 22, 2024
A contractor’s etiquette lesson: to be a neighborly contractor, love your neighbors
Being realistic with project schedules, following local building codes, and mitigating excess noise are easy ways to be a neighborly contractor.
August 19, 2024
NYC focus on construction worker ODs highlights an epidemic
Substance abuse-related deaths are at an all-time high in the construction industry, but New York City officials are trying to reduce deaths through education.
August 16, 2024
Nira app sheds light on infrastructure
Nira is a collaborative platform that can render massive 3D assets for greater interactivity, web-based inspection, and review from multiple devices.
August 14, 2024
Chemical exposure and hearing loss in construction
When combined with loud and constant noises common to construction sites, exposure to certain chemicals can lead to auditory damage.
August 13, 2024
Värde Partners and David Weekley Homes join forces for land banking venture
A global investment firm and a home builder recently announced a joint venture to bank residential land in high-demand U.S. markets.
August 13, 2024
CAT’s new 973 track loader adds power and AI
CAT’s new 973 track loader is more powerful, maneuverable, intelligent, and fuel-efficient than before.
August 12, 2024
Kyowa Kirin to build $530 million facility in NC
Japan-based pharmaceutical company Kyowa Kirin recently announced plans to build a new biologic facility in Sanford, NC.
August 12, 2024
Protecting skilled trades workers from silica exposure
Construction workers are often exposed to silica dust, which can lead to lung cancer or silicosis. Protect yourself with these tips.
August 8, 2024
Solving the worker shortage, one employee at a time
Showing respect, offering perks and benefits, and providing growth opportunities are a few ways to improve employee retention in the construction industry.
August 2, 2024
Business spotlight: Canvas robot revolutionizing drywall installation
San Francisco-based construction robotics firm Canvas’ robot drywall finisher makes installing and finishing drywall easier and more efficient.
July 30, 2024
Tutor Perini gets $48 million Alcatraz renovation contract
Tutor Perini landed a $48.6 million renovation contract for Alcatraz that’ll make it safe for the more than one million annual visitors.
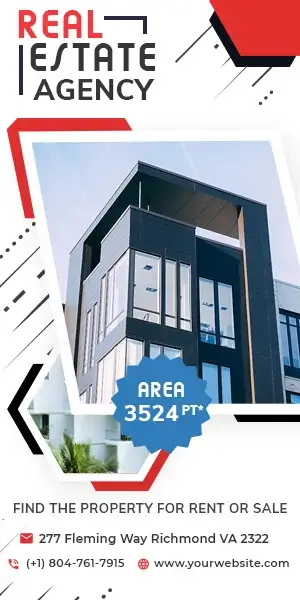