July 17, 2024
Cordish Companies unveils $1.4 billion Petersburg project
The Cordish Companies announced a $1.4 billion mixed-use development in Petersburg, VA, including a casino.
July 11, 2024
B.C. construction labor shortage good for workers
A shortage of construction workers in British Columbia is increasing wages and impeding contractors’ ability to take on new projects.
July 10, 2024
Pregnant Workers Fairness Act protects workers with pregnancy-related conditions
The new Pregnant Workers Fairness Act helps employees with pregnancy-related health conditions by offering reasonable accommodations at work.
June 28, 2024
Worker receives $900k settlement for busted hip
Allowing hazardous construction site conditions ruined a young union operating engineer’s hip, damaging his livelihood, and cost those he sued $919,000 for injuries.
June 27, 2024
Families of workers killed, injured at U of Chicago Hospital sue
Families of one ironworker killed, and another injured due to falls suffered in high winds on a Chicago construction site are suing two defendants for…
June 27, 2024
Work on billion-dollar Pittsburgh hospital tower halted
Pittsburgh city officials have paused work on a 900,000 SF hospital tower due to a lack of building permits, putting over 100 workers temporarily out…
June 26, 2024
NTSB preliminary report on Youngstown explosion released
The NTSB’s preliminary report on the fatal gas explosion in Youngstown answered some questions regarding the blast that killed one and injured nine others.
June 25, 2024
140k contract led to gas explosion killing 1, injuring 7
A small-dollar contract to remove and relocate utility lines in Youngstown led to a fatal gas explosion. The incident is currently under investigation by NTSB.
May 27, 2024
Ontario contractors expect robust growth in 2024
The annual Ontario Construction Secretariat Survey found Ontario contractors are hopeful about the upcoming year and expect business growth.
May 21, 2024
Fern Hollow Bridge lawsuits target Pittsburgh and three engineering firms
Survivors of the Fern Hollow Bridge collapse are suing three prominent engineering firms and the city of Pittsburgh for negligence.
May 21, 2024
Fire safety for construction sites
Fire safety in the construction industry involves proper fire training, regular safety meetings, fire safety procedures, situational awareness, and learning from mistakes.
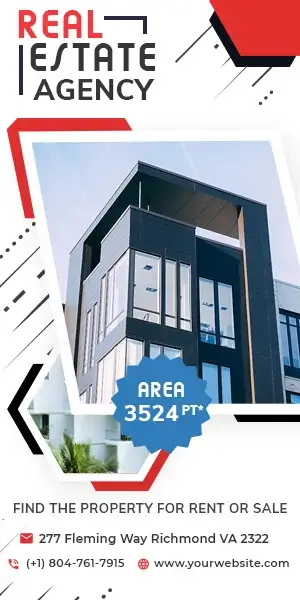