Plant Prefab is transforming the construction industry by creating high-quality, sustainable prefabricated homes faster and with less waste. Based in California, this innovative company partners with architects, developers, and homeowners to deliver custom designs that meet the growing demand for eco-friendly housing while tackling challenges like labor shortages and rising material costs. By rethinking traditional building methods, Plant Prefab leads the charge toward a greener, more efficient future.
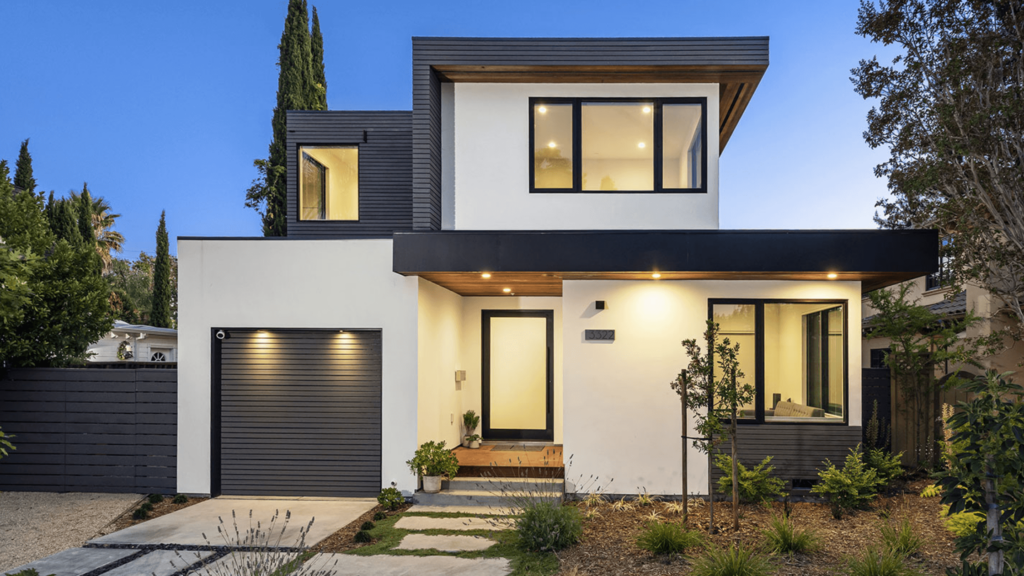
Founded in 2016 by former CEO Steve Glenn, Plant Prefab has carved out a niche in the market by combining sustainability, advanced technology, and exceptional design. “I wanted to be an architect growing up,” says Glenn, though his career path took him down a different road. “I learned that if you really care about the quality of the built environment, developers are in a position to facilitate great design.”
Plant Prefab’s patented Plant Building System allows homes to be built with precision and speed, reducing waste by up to 30% compared to traditional construction methods. This efficiency helps the environment and slashes construction timelines—something today’s market desperately needs.
“We’re working in regions where land is most expensive, and labor is most scarce, for example, urban cities and mountain home communities. Because of costs, their need for construction efficiency is greatest,” says Glenn, claiming that prefab can address a host of building challenges beyond the bottom line.
A bespoke approach to traditional prefab
Unlike many prefab companies offering limited, cookie-cutter options, Plant Prefab specializes in customization. “The industry is focused on lower-cost products. But if you’re building in cities and mountain communities, they tend to have higher budgets because they expect better quality products,” he says. “They need to be customized because lot sizes, zoning, and design requirements can vary from neighborhood to neighborhood. So we said, ‘We’re going to be the best in the world at doing custom products,’ and that’s unique.”
Another unique value-add is Plant Prefab’s robust toolkit. Whereas most prefab building systems use either panels or mods, Glenn’s brainchild employs both. “A hybrid approach is better for the design, the budget, and the transportation logistics,” he says. “Ours is the only facility in the US purpose-built to do both panels and mods with automation.”
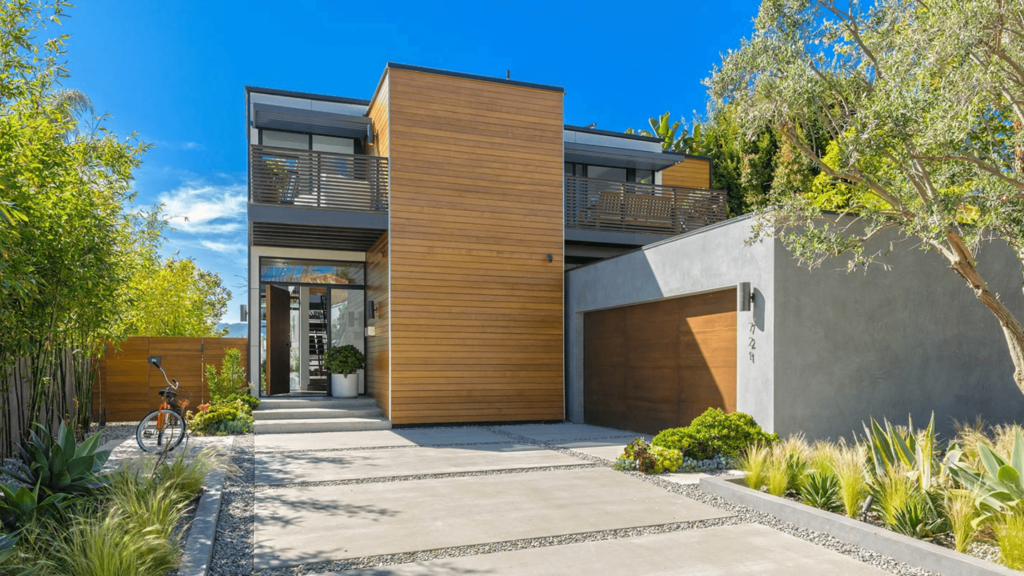
This versatility has earned them recognition for their innovative designs and a portfolio of award-winning projects that showcase their commitment to customization and sustainability, including:
- Custom single-family LivingHome in Santa Monica, CA: Designed by the late Ray Kappe, FAIA, this home was the first to achieve LEED Platinum certification. It combines California Modernist elements with meticulous attention to detail, setting a new standard for sustainable design.
- Three-story townhomes in San Francisco, CA: In collaboration with KieranTimberlake, Plant Prefab developed seven townhomes in the Presidio National Park. This project was the first multi-family dwelling in San Francisco to achieve LEED Platinum certification, featuring energy-efficient appliances, photovoltaic panels, and sustainable materials.
- Affordable housing development in Santa Monica, CA: Partnering with Brooks + Scarpa, Plant Prefab is constructing a four-story affordable housing development featuring 13 units. Utilizing the Nest LivingHome Toolkit, this project aims to provide supportive housing for low-income families, focusing on cost-effectiveness and sustainability.
- LivingHome 6 in Napa County, CA: This custom single-family home was designed for a chef passionate about sustainability. The 1,200-square-foot residence features an open living space, a gourmet kitchen, and extensive outdoor areas, achieving LEED Platinum certification and significantly reducing energy consumption.
Sustainable products, sustainable building
Plant Prefab’s focus on sustainability, both in terms of what it builds and how it operates, sets it apart in the industry. Sustainability is at the heart of everything they do, including reducing energy and water use, sourcing recycled materials, and improving indoor air quality. “The environment factors into how we build, as well as how we operate,” Glenn emphasizes. “We’re careful about our practices in terms of our own ecological footprint.” Their commitment ensures that every project leaves a smaller environmental footprint without sacrificing style or quality.
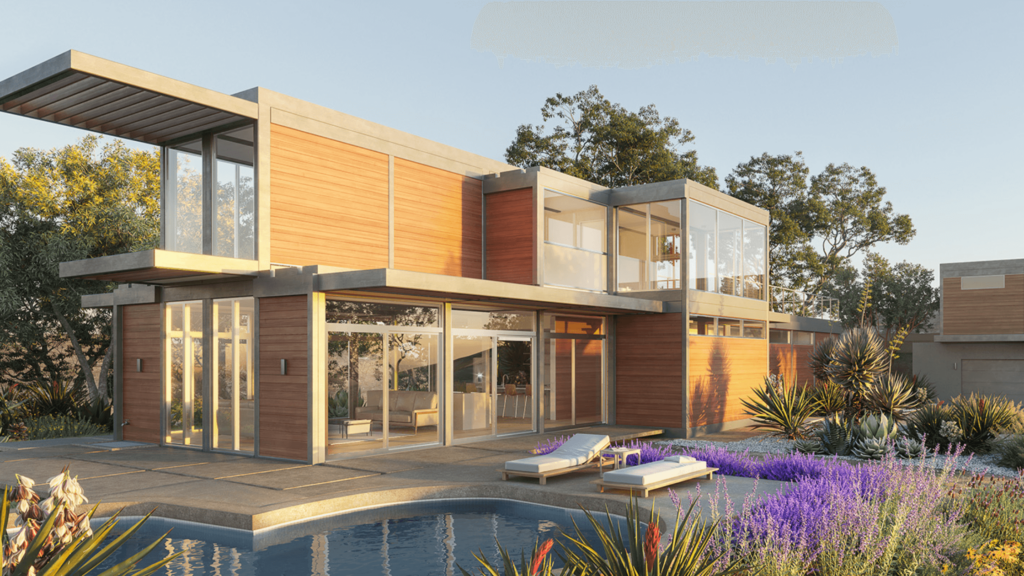
With rising pressures on the construction industry to deliver housing faster and more sustainably, Plant Prefab offers a forward-thinking solution. By combining cutting-edge technology, eco-friendly practices, and a dedication to customization, they’re proving that prefab homes can be efficient and beautiful. “I think good design inspires people. It certainly inspires me,” Glenn says. “If it’s a home, you feel more comfortable, you feel safer, you feel happier. If it’s a work environment, you feel more productive. If it’s a hospital, you heal faster. Design matters, and we’re helping to make good design responsibly.”
Whether you’re an industry professional or simply curious about the future of housing, Plant Prefab is a name to watch.
Want to stay updated on the latest in sustainable construction and prefab innovation?
Subscribe to our newsletter and join a growing community dedicated to advancing the future of the AEC industry.
1 comment