Building smarter, faster, and with less waste is more important than ever in today’s construction landscape. Panelized construction offers an innovative solution, where building components are pre-made in a factory and assembled on-site. This approach is gaining traction for its potential to save time, reduce costs, and improve energy efficiency. Still, like any method, challenges like upfront costs and transportation logistics are critical for companies to consider before taking the plunge.
Quick look
- Panelized construction pre-manufactures building components in factories, offering time savings, cost reductions, and improved energy efficiency.
- This method bridges traditional construction and prefab techniques, providing design flexibility without compromising precision.
- Builders benefit from faster project timelines, superior quality control, and less material waste than on-site construction.
- While panelized construction offers numerous advantages, challenges like upfront costs and transportation logistics need careful consideration.
What is panelized construction?
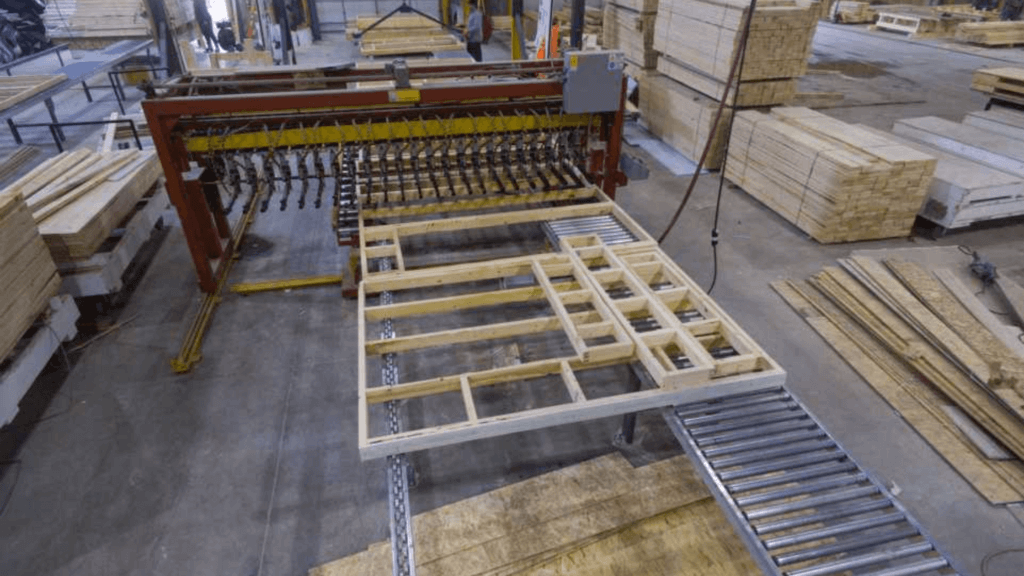
Panelized construction is a modern building technique in which key components—like walls, floors, and roof panels—are manufactured in a controlled factory environment. These pre-made panels are then transported to the construction site, where they’re assembled to create the structure of a home or building.
This process bridges the gap between traditional on-site construction and prefabricated or modular methods, offering a mix of efficiency and flexibility. While it shares similarities with modular and manufactured housing—both involving off-site production—panelized construction often provides more design freedom and customization. Unlike modular homes, which are delivered in large, pre-assembled sections, panelized systems offer builders the ability to tailor layouts while enjoying the benefits of factory precision. It’s a smart hybrid approach that combines the best of both worlds.
Panelized construction vs modular building
At first glance, panelized construction might seem like another prefab building, but key differences set it apart. Both methods aim to streamline construction by creating components off-site in a controlled environment, but the scope and assembly differ significantly.
Prefab construction is an umbrella term that includes modular and manufactured housing. Modular homes are built in large sections or “modules,” which are transported to the site and joined together. Manufactured housing, often called mobile homes, is constructed entirely off-site and delivered as a complete unit. While these methods focus on pre-assembled, nearly finished products, panelized construction takes a more adaptable approach.
Because panelized systems involve individual components—such as walls, floors, and roofs—delivered to the site for assembly, builders and clients have greater flexibility in customizing layouts, as pre-designed modules do not limit them. Additionally, because panelized components are smaller and easier to transport, they can be used in areas where larger modular or manufactured housing would be impractical.
Panelized construction blends the efficiency of prefab methods with the versatility of traditional on-site building, making it a standout option for those seeking both precision and design freedom.
Perks of panelized construction for builders
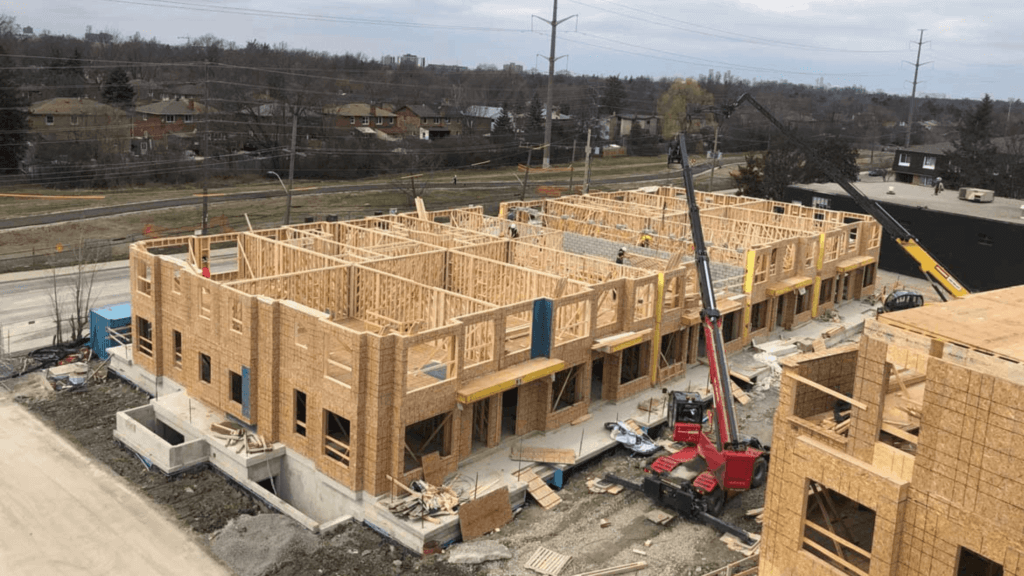
1. Time savings
One of the most significant advantages of panelized construction is how much time it saves on the job site. Because panels are manufactured in a factory before arriving at the construction location, much of the labor-intensive work is completed ahead of time. This reduces the time needed for framing, roofing, and other structural tasks, allowing builders to focus on assembly rather than starting from scratch.
This quick turnaround is especially beneficial for projects with tight timelines or in regions where the weather can be unpredictable. By minimizing the time spent exposed to the elements, builders can protect materials and maintain momentum on the project. With panelized construction, a faster build doesn’t mean compromising quality but achieving it more efficiently.
In traditional construction, delays caused by weather or labor shortages can significantly extend timelines. Panelized construction minimizes these risks because the panels are built indoors under controlled conditions, keeping production on schedule. Once delivered, these ready-to-assemble components fit together quickly and precisely, reducing timelines by up to 50%—translating to roughly five months off a typical build. For builders juggling multiple projects, these time savings can make a huge difference in meeting deadlines and keeping clients happy.
2. Quality control
Panelized construction stands out for its superior quality control. Unlike traditional building methods, which are often subject to weather delays, inconsistent labor, and varying site conditions, panelized components are crafted in a controlled factory environment. This ensures precision and consistency in every piece, from walls to roof panels.
The factory setting allows for advanced technology and skilled workers to oversee every production stage, reducing the likelihood of defects or errors. Materials are stored in optimal conditions, meaning they’re not exposed to moisture, warping, or other environmental factors that can compromise quality. Builders also benefit from panels that fit together perfectly, ensuring stronger, more durable structures.
For builders aiming to deliver a high-quality product, panelized construction offers peace of mind. Combining standardized manufacturing and rigorous inspections results in homes and buildings that meet and often exceed industry standards. It’s a smarter, more reliable way to build.
3. Cost savings
Panelized construction can be a game-changer for builders looking to save on costs without sacrificing quality. One significant cost benefit comes from labor efficiency. Because the panels are pre-manufactured in a factory, much of the work that would typically happen on-site—like cutting, measuring, and framing—is already done. This reduces the need for large on-site crews and cuts down on labor hours, ultimately saving money.
Another significant cost advantage is the reduction in material waste. In traditional construction, cutting materials on-site often results in leftover scraps that can’t be reused, leading to higher expenses. With panelized construction, precision cutting in the factory ensures materials are used efficiently, minimizing waste and lowering overall material costs.
Faster build times associated with panelized construction can also save builders money by reducing project overheads, such as equipment rentals, on-site storage, and temporary utilities. In the long run, this streamlined process allows builders to deliver high-quality projects while keeping budgets in check—making it a win-win for builders and clients.
4. Energy efficiency
Panelized construction stands apart when it comes to building energy-efficient homes. Precision manufacturing ensures that each panel is cut and assembled to exact specifications, resulting in a tightly sealed structure. This reduces gaps and air leaks, which are common in traditional on-site construction and can lead to energy loss.
Factory-made panels are often designed with energy efficiency in mind, incorporating advanced materials like high-performance insulation and moisture barriers. These features help maintain consistent indoor temperatures, reducing the need for excessive heating or cooling and lowering homeowners’ energy bills.
Builders can also integrate energy-efficient technologies, such as pre-installed conduits for renewable energy systems, directly into the panels during manufacturing. By combining tight seals, superior insulation, and energy-conscious design, panelized construction offers a sustainable approach that meets the growing demand for eco-friendly homes.
5. Design freedom
Panelized construction offers impressive flexibility regarding custom designs and architectural creativity. Unlike modular construction, which often relies on standard sizes and layouts, panelized systems can be tailored to meet unique design specifications. This allows builders and architects to create homes and buildings that reflect individual styles and preferences without compromising efficiency.
Whether you’re working on a modern, minimalist home or a more traditional structure, panelized construction adapts to various architectural styles. Panels can be customized to include unique window placements, vaulted ceilings, or even intricate rooflines. This versatility allows builders and clients to innovate and personalize their projects.
Additionally, panelized construction isn’t limited to residential projects. It can be used for commercial buildings, multifamily housing, and more, making it a versatile solution for almost any type of construction. By combining factory precision with creative potential, panelized construction strikes the perfect balance between efficiency and individuality.
6. Versatility
One of the greatest strengths of panelized construction is its remarkable versatility. This building method can be adapted to suit a wide range of home styles, sizes, and locations, making it a go-to solution for projects with unique requirements.
These are not cookie-cutter homes! From compact urban homes to sprawling country estates, panelized construction can accommodate virtually any design. Its adaptability allows builders to tackle everything from sleek, modern designs to more traditional or rustic aesthetics. Panels can be customized to fit different layouts, rooflines, and architectural details, ensuring the finished product meets the client’s vision.
Panelized construction is also well-suited to various environments. Whether building in a busy city, a remote rural area, or even on uneven terrain, the pre-manufactured panels can be transported and assembled efficiently. This adaptability makes it a practical choice for projects that might otherwise face logistical challenges.
7. Less waste
Panelized construction is an eco-conscious building method that significantly reduces material waste. In traditional construction, on-site cutting and measuring often lead to scraps of wood, insulation, and other materials being discarded because they can’t be reused. This drives up costs and contributes to landfill waste.
With panelized construction, everything is fabricated in a factory with precision machinery, ensuring materials are used efficiently. Panels are cut to exact specifications, and any excess material is often recycled or repurposed during manufacturing. This level of control means minimal waste compared to the trial-and-error nature of on-site builds.
For builders, less waste means lower material costs and a smaller environmental footprint. It’s a win-win: saving resources while aligning with sustainable construction practices that clients increasingly value. Panelized construction makes it easier to build responsibly without sacrificing quality or efficiency.
Things to consider with panelized construction
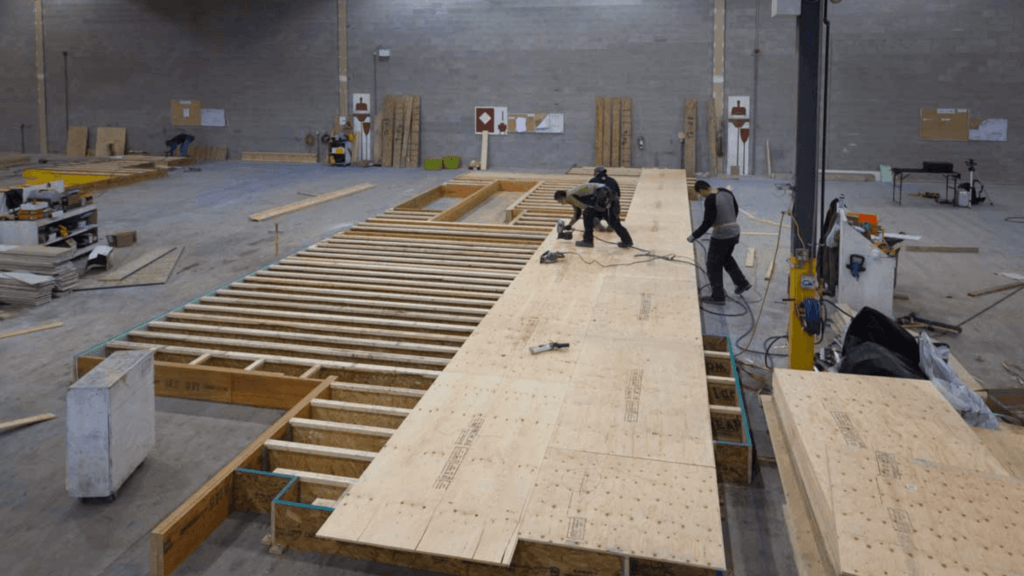
While panelized construction offers numerous benefits, there are a few considerations to make before using this building method. Understanding the potential challenges can help builders and homeowners make more informed decisions.
- Upfront costs: The initial cost of manufacturing panels can be higher than that of traditional building methods. Although long-term savings in labor and materials often offset these expenses, the upfront investment might be a hurdle for some projects, particularly smaller-scale builds or those with tight budgets.
- Transportation logistics: Transporting large panels to the construction site can pose logistical challenges, especially in remote or hard-to-reach areas. Narrow roads, weight restrictions, or rugged terrain can complicate deliveries, adding to overall project costs and timelines.
- Limited familiarity among contractors: Not all contractors and crews are familiar with panelized construction, which can lead to learning curves or missteps during on-site assembly. Finding experienced builders or investing in proper training is essential to ensure a smooth process and avoid costly mistakes.
- Standardization constraints: While panelized construction offers significant design freedom, some highly customized features still require additional on-site work or adjustments, which could diminish the time and cost savings.
Bottom line
Panelized construction offers a smarter, more efficient way to build, combining time savings, cost efficiency, and sustainability. With factory-made panels that minimize waste, ensure quality control, and speed up on-site assembly, it’s no wonder this method is gaining traction in the building industry. It’s clear why many builders see panelized construction as the way forward, and with the right planning, this could be the innovative solution that takes builds to the next level.
Want to learn more? Subscribe to our weekly newsletter!
1 comment