In today’s economy, affordable housing construction projects are hard to come by. Canada, in particular, is seeing a high demand for affordable housing that greatly exceeds the available supply. In Quebec alone, it’s estimated that close to 51,000 households are on a waitlist for affordable housing. In 2025, Canadians will see a few large-scale affordable housing options pop up, like 1600 Av. de Lorimier Place, Hart Road, and Blatchford. While these projects won’t put a dent in the nation’s affordable housing demand, they will relieve hundreds of families from having to continue their search.
5 affordable housing projects being built across Canada
1. 1600 Av. De Lorimier Place
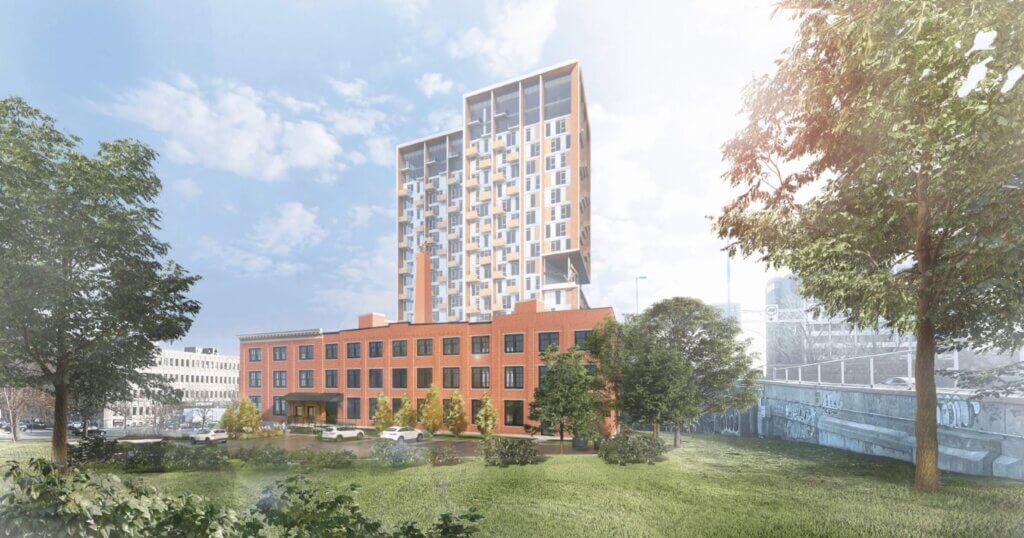
Location: Montreal, Quebec
Size/specs: 304 Units
Timeline: Completion estimated October 2026
Located in the heart of Montreal, 1,600 Av. De Lorimier is a collaboration between developer Bertone and the Canada Mortgage and Housing Corporation. The new high-rise building will include 304 units and has been designed with energy efficiency and accessibility in mind.
This project is expected to revitalize the Centre-Sud district while complementing and preserving the old Barsalou soap factory. Like many buildings in Montreal, it’s a building style that converts old industrial into modern residential. The building is currently in development and is slated for completion in the fall of 2026.
2. Gladstone Village
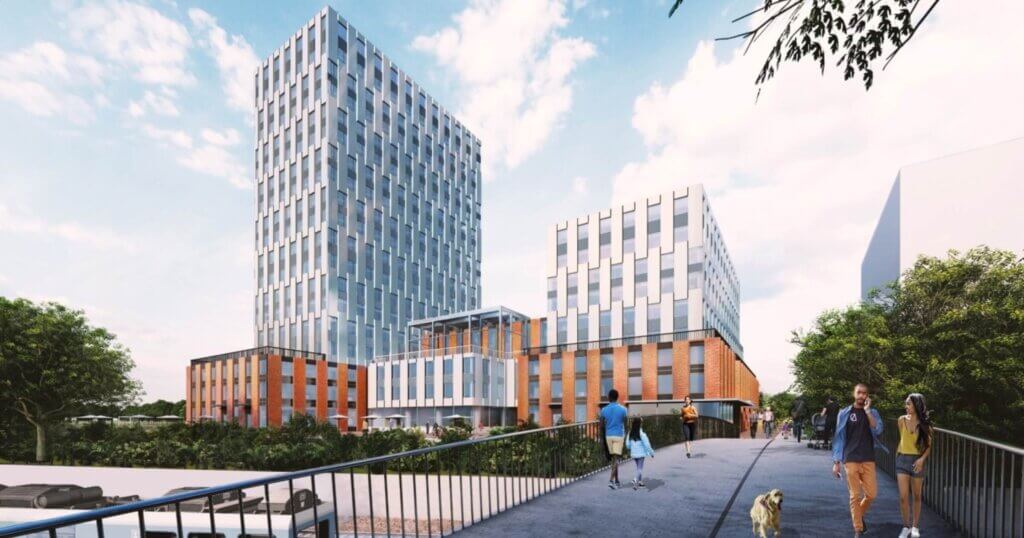
Location: Ottawa, Ontario
Size/specs: 338 Units
Timeline: Completion estimated 2027
Gladstone Village is an affordable housing and mixed-use project consisting of 338 residential units as well as retail and office space. The residential options include mixed-income, mixed-low-density (high, low, and mid-rise), and mixed-tenure (rent or own) options. Phase one, currently under construction, will see an 18-story building with 2,000 square feet of commercial space.
The Ottawa Community Housing project will include both indoor and outdoor spaces for residents to enjoy. The design boasts sustainability features, including high-efficiency heating and cooling and wastewater heat recovery. The roof of the building will also have solar photovoltaic (PV) panels.
The project, slated for completion in 2027, will include scooter and bicycle parking, a fitness room, an event space, EV charging stations, indoor and outdoor lounges, and more.
3. Naut’sa Mawt
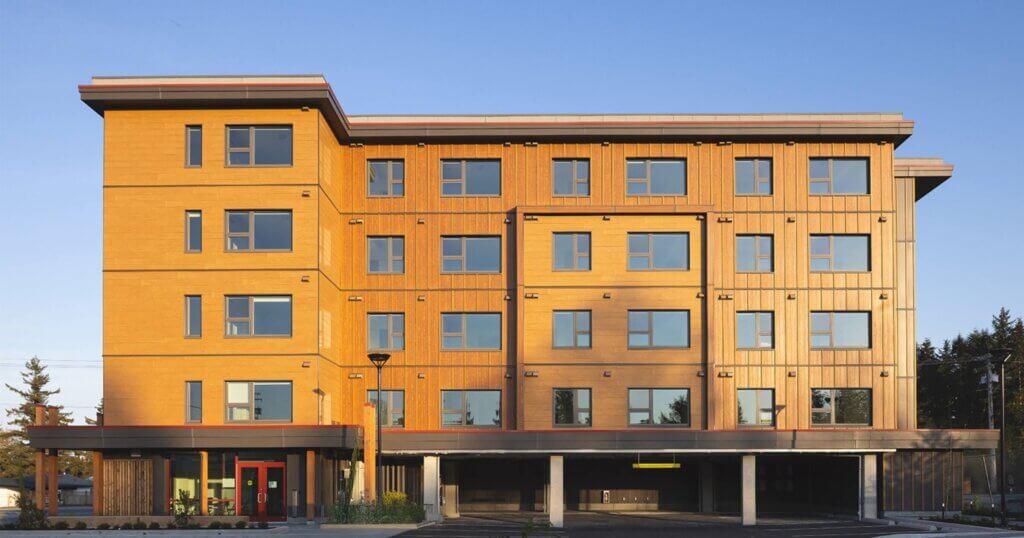
Location: Courtenay, British Columbia
Size/specs: 40 Units
Timeline: Recently finished
The development for Naut’sa Mawt was recently finished in May 2025 and contains 40 affordable homes prioritized for Indigenous people in the Courtenay, British Columbia area. Naut’sa Mawt (pronounced not-sa mott) is a Coast Salish word that means “together as one,” and project manager Wachiay Friendship Centre Society aims to bring the community together with a mix of studio and one-bed units in the 5-story wood frame building.
The rent in Naut’sa Mawt will range from $500 to around $1,300 per month, and almost all units will be adaptable or accessible for people with diverse needs. The project managers hope to facilitate the gathering of indigenous and non-indigenous communities to exchange culture and traditions. The building will also be located right across from the Wachiay Friendship Centre, which offers more than 50 services to the Courtenay community.
4. Hart Road
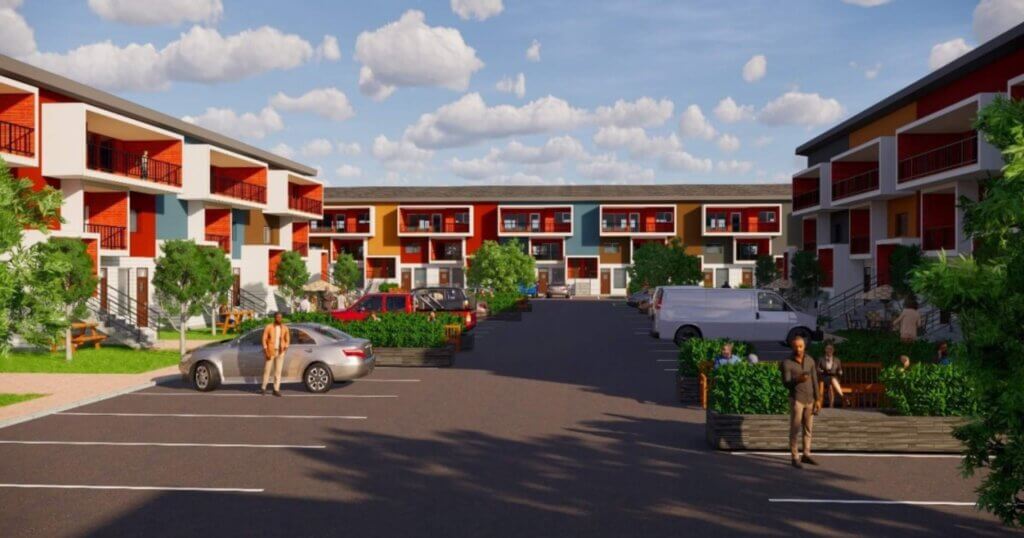
Location: Saskatoon, Saskatchewan
Size/specs: 164 Homes
Timeline: Completion estimated for fall 2025
Hart Road is one project on our list near completion. It’s described as a self-contained community specifically for the First Nations and Métis peoples. Managed by Camponi, this project will bring unity, community, and empowerment to Indigenous communities. Camponi surveyed members of the community to get a sense of what they’d like to see in the building, and Indigenous daycare topped the list and will be offered.
The project features 164 units and is supported by Saskatoon’s affordable housing plan. It will also feature a gym and a community kitchen. Phase one is expected to be completed in June 2025, with tenants moving in as early as the fall.
5. Blatchford development
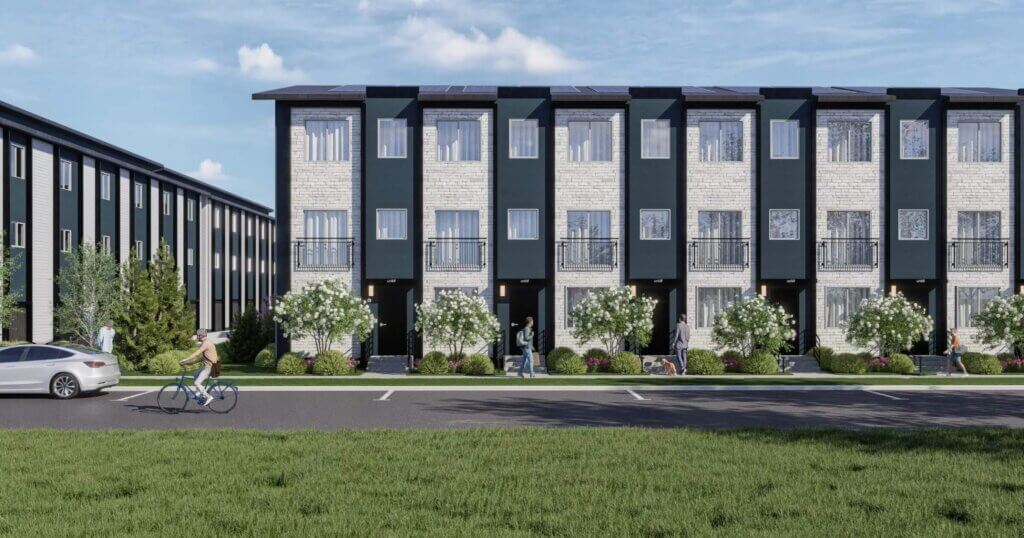
Location: Edmonton, Alberta
Size/specs: 401 Units
Timeline: Full community completion by 2042
Edmonton’s Blatchford development is the largest on our list, with 401 total units. This project aims to establish an affordable, carbon-neutral community. Located in the heart of the city, Blatchford will actually be built on the site of the former Edmonton City Centre Airport. It will have green areas and many energy-efficient amenities like solar panels and district energy systems.
Smart city features include smart waste management, water conservation, and traffic monitoring in an effort to reduce the community’s carbon footprint. The project also features a mix of housing options catered to incomes of all levels, making it accessible for all.
Is large-scale affordable housing construction growing in 2025?
Currently, the Canadian residential construction market has been grappling with internal and external factors that have slowed growth and availability over the past few years. The main challenges the market is facing include rising interest rates, mortgage rates, and labor shortages in the construction industry.
Large-scale construction projects, in particular, are also struggling with developer financing. Increased borrowing costs make many projects less financially viable. The market is also facing issues with skilled worker gaps. Where construction does pick up, there is often a lack of qualified workers, which slows down project quality and completion timelines.
Finally, the market is experiencing rising material costs, shortages, and supply chain disruptions. While not new, these challenges combine to slow the growth of the market, while affordable housing demand is only rising. Hope, however, is not completely lost as new leaders in government bring new initiatives to mitigate the issues plaguing the industry.
What to expect next in affordable housing construction
Although there are many ongoing challenges, there are also factors that could contribute to a rebound in affordable housing construction in Canada. Here are some elements that could contribute to new opportunities for some small contractors:
- Government housing programs and initiatives: The Canadian government has been working toward improving housing affordability. They’ve allocated funds to affordable housing initiatives, have increased investments in infrastructure in urban areas, and have offered tax breaks and other financial incentives to smaller contractors working on residential units.
- Interest rate stabilization: As the Bank of Canada makes an effort to curb inflation, interest rates are expected to stabilize in 2025. The plateau should bring slower mortgage rates and may stimulate the demand for new affordable homes.
- Technology advancements in construction: Modular and prefabricated construction have risen in popularity, making it easier for developers to save time and money. This, combined with the increase in construction AI and automation, helps reduce labor costs, increases project speed, and potentially meets the rising housing demand.
Don’t expect these factors to change the market overnight, but they could compound and balance out the demand vs supply starting this year and continuing into the future. With the new administration in place, there might be shifts in policy that accelerate housing starts or slow the progression of more affordable projects throughout the country.
Loved this article about affordable housing in Canada? Check out similar articles about the housing market and upcoming construction projects, including a look at data center construction projects underway and why mid-rise construction is the sweet spot for housing growth.
And don’t forget to subscribe to the newsletter and follow us on LinkedIn to stay looped in about news in the AEC space.