Labor shortages can result in inexperienced workers, overburdened supervisors, and reduced training. These factors can undermine workplace safety and increase the likelihood of accidents and injuries. By proactively addressing these issues—through training, supervision, and clear communication—companies can help mitigate risks and maintain safer worksites despite labor shortages.
The labor problem
Both the United States and Canada are straining under massive skilled labor shortages. A recent report by the National Association of Homebuilders states that 723,000 workers are needed to meet current housing and infrastructure projects in the United States, and a recent survey by the Associated General Contractors of America shows that 88% of contractors need help hiring skilled labor. In Canada, 700,000 skilled tradespeople will retire by 2028, causing a massive shortage of skilled tradespeople.
These labor shortages aren’t just a headache for hiring managers; they also have real-world effects, such as project delays, increased costs, decreased quality control, and safety issues.
Labor shortages and safety
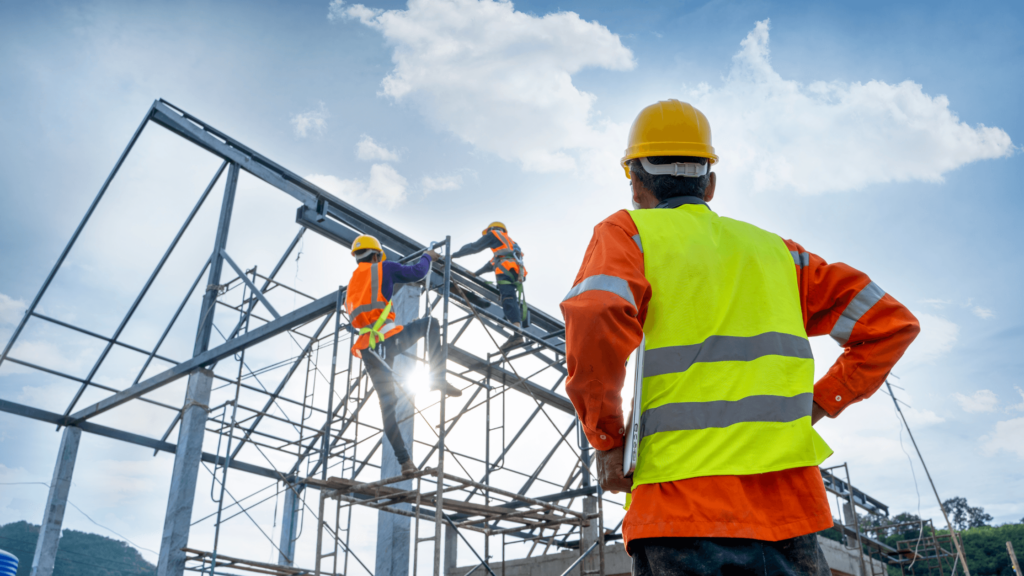
Those who have worked on construction sites know firsthand how labor shortages can compromise safety. When your crew is down a few people, it puts immense pressure on the team to meet deadlines and maintain work quality with fewer hands on deck.
Shortcuts
When deadlines are looming and there aren’t enough workers to fill every role, it can be tempting to cut corners. These shortcuts include skipping safety precautions, rushing through tasks, or failing to perform routine machine maintenance. Shortcuts can compromise the safety of crews and worksites, increasing the risk of accidents like falls, equipment failures, and structural collapses.
Inexperienced crews
Labor shortages often mean that companies must fill roles by any means necessary—even if those applying lack the skills or experience needed to do the job. Inexperienced workers may not have the same technical knowledge or familiarity with safety standards as more seasoned tradespeople. This increases the likelihood of mishandling equipment, misinterpreting instructions, and not recognizing potential workplace safety hazards, such as unstable scaffolding or improperly secured loads.
Reduced supervision
Supervisors are often stretched thin during labor shortages. They try to be in several places simultaneously while managing several or larger crews than usual, which reduces their ability to monitor all activities effectively. Without adequate supervision, crews may fail to wear appropriate PPE and safety rules may not be enforced.
Lack of training
While trying to fill labor gaps, many companies might prioritize getting workers on-site over adequately training them. Untrained workers pose a significant risk to worksite safety because they may not know how to respond to emergencies like fires, chemical spills, or equipment malfunctions.
New (or more) subcontractors
Labor shortages can force general contractors to use subcontractors to fill gaps in specific trades. While subcontractors may be skilled and experienced in their respective trades, they may not share the same safety standards, and poor communication between subcontractors and leading crews can cause safety hazards.
How to maintain safe work sites amid labor shortages
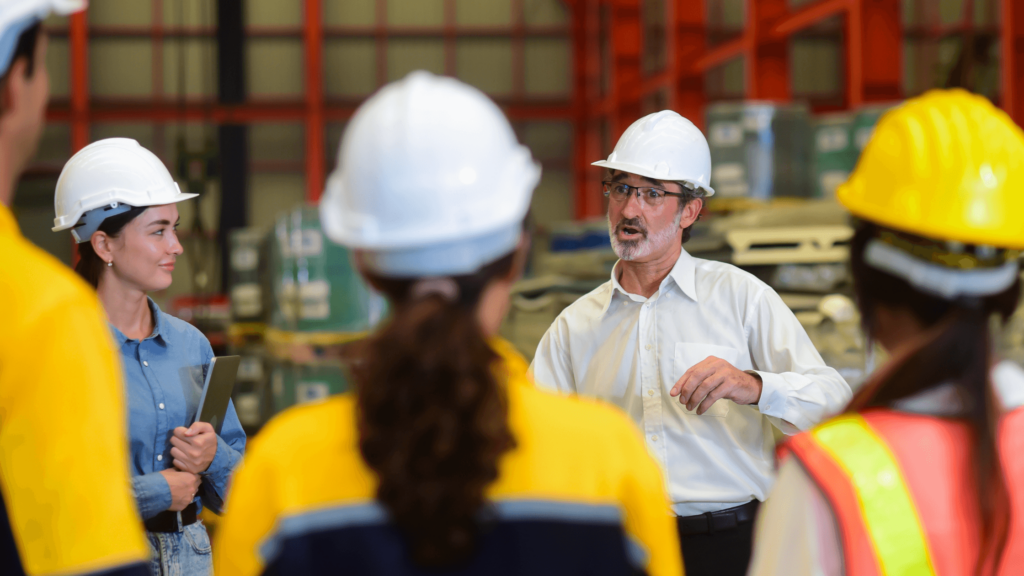
Even when short-staffed, maintaining a strong commitment to safety is crucial for protecting workers, preventing accidents, and ensuring projects are completed on time. There are several steps companies can take to maintain safe worksites even when facing significant labor shortages.
1. Connected safety
When supervisors struggle to be everywhere at once, technology can help shoulder some of the load. Connected safety involves leveraging the power of AI technology to help keep workers (and worksites) safe.
Drones and remote site monitoring systems can use AI to identify risks, hazards, and potential accidents, while AI-powered cameras can identify workers not wearing appropriate PPE. These technological helpers can reduce the need for human oversight by automating many safety monitoring tasks and preventing accidents before they happen.
2. Conduct regular safety briefings
Companies experiencing labor shortages are often short on time, but while skipping safety meetings may be tempting, running a short-staffed crew makes regular safety briefings more critical than ever.
Regularly reviewing safety protocols, procedures, risks, and precautions means everyone’s on the same page, from new hires to subcontractors. These meetings also reinforce that safety culture remains a top priority in the workplace, regardless of staffing issues.
3. Enforce safety protocols
Labor shortages often lead to lapses in safety compliance, but enforcing safety protocols ensures that everyone on the crew knows that safety is non-negotiable. To do this, companies must first communicate their safety protocols (like PPE requirements and safe equipment operation guidelines) before also communicating the consequences of not following these procedures.
4. On-site inspections
Similarly, on-site inspections can help identify and address unsafe conditions before accidents occur. To keep worksites safe, companies should conduct regular inspections to evaluate the safety of scaffolding, tools, machinery, and especially high-risk areas like trenches. On-site inspections reduce risks, eliminate hazards, and provide data and documentation to help companies identify patterns in unsafe practices.
Bottom line
Labor shortages can put worksite safety at risk, but companies can prevent accidents by maintaining safety procedures and protocols. Even when running short on skilled tradespeople, it’s possible to maintain safe worksites with technology, proactive communication, supervision, and consistent oversight.
For more tips about staying safe on the job site and under the hard hat, subscribe to our newsletter!
2 comments