Artificial intelligence (AI) models can write and create art; now, companies are leveraging the power of AI to use on construction sites. From alerting site managers of missing PPE to autonomously controlling heavy machinery, AI technology is increasing job site safety, accuracy, and efficiency. Dozer, AIM, and AlwaysAI are some companies leading the way in AI-driven workplace safety.
AI in construction
Construction isn’t necessarily the first industry you’d think of when envisioning how AI can be applied in the real world. Still, in recent years, innovative companies have shown how useful it can be.
- Project planning: AI programs can reduce errors and expedite the planning process by analyzing environmental, material, and regulatory data, making the process simple and seamless.
- Project management: Assisting with accurate costing, estimating, risk management, and monitoring construction progress takes many onerous project management tasks and leverages the power of AI to get them done quicker and easier.
- Robotics and autonomous machinery: AI-operated heavy equipment, robotic devices that can create accurate design layouts, and robots to handle dangerous construction tasks—AI is moving beyond the screen and into the job site to make construction safer and more consistent.
- Safety monitoring: Artificial intelligence software can detect when workers have failed to protect themselves by wearing appropriate PPE and monitor sites for human collisions, safety risks, and hazards.
The link between AI and workplace safety
Human beings are fallible. We make mistakes, miss details, and forget to wear PPE; our decision-making and cognitive abilities are affected by a poor night’s sleep, worries about loved ones, or extreme weather conditions. Conversely, AI provides a consistent, accurate source of data, tracking, and information. Here are four companies leveraging the power of artificial intelligence models to make worksites safer.
4 companies using AI to improve job site safety
Dozer
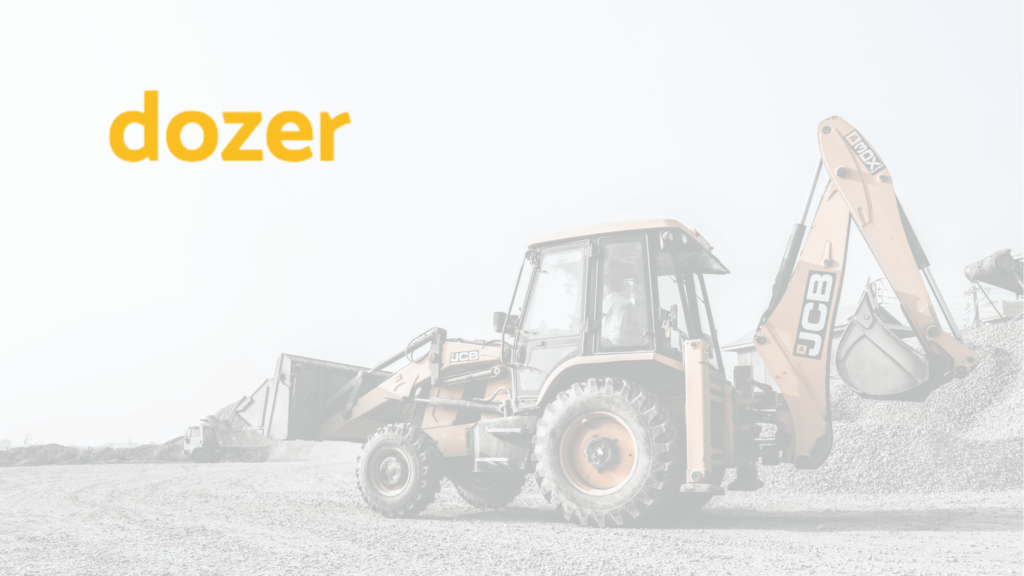
Like an AI-powered dashcam for your construction equipment, Dozer cameras provide a 360-degree view of each machine it’s installed on at the construction site, including the cabin and bucket. In addition to a live video feed you can access remotely anytime, Dozer uses an artificial intelligence platform to document collisions, near misses, and human proximity and calculate each machine’s risk level. All information is compiled in an easy-to-read dashboard, allowing you to track machine operations remotely.
Dozer also sends safety alerts about incidents or close calls, ensuring that you are notified about accidents in real-time without waiting for an incident report after the fact.
The Dozer system is easily installed with included wire management, sensor clips, and camera mounts, and requires a 12-volt power source. The platform is available for desktops and as an app for iPhones and Android devices.
AIM
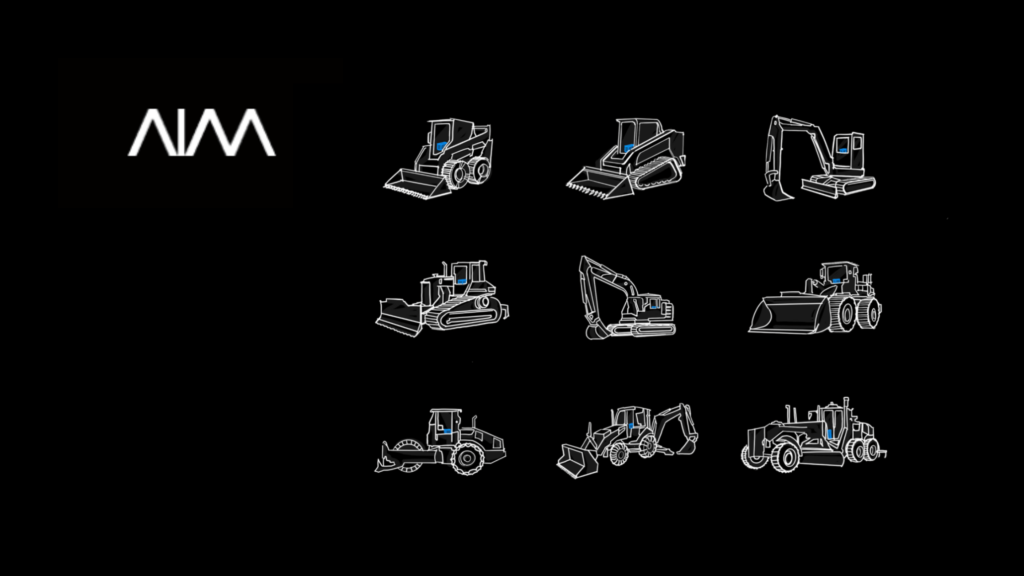
Bellevue, Washington-based AIM has created an AI program capable of operating heavy construction equipment, including bulldozers, excavators, and skid steers. By enabling AIM, heavy equipment becomes fully autonomous and can operate day and night in any weather.
The autonomous system can be retrofitted to older machinery, installed in a day, and allows users to operate in three modes: fully autonomous, via remote control, or manually with an operator.
Although AIM has experienced no accidents to date, its website pre-empts concerns about safety and insurance by stating that every AIM-enabled machine is insured for autonomous operation by a global insurance company.
AlwaysAI
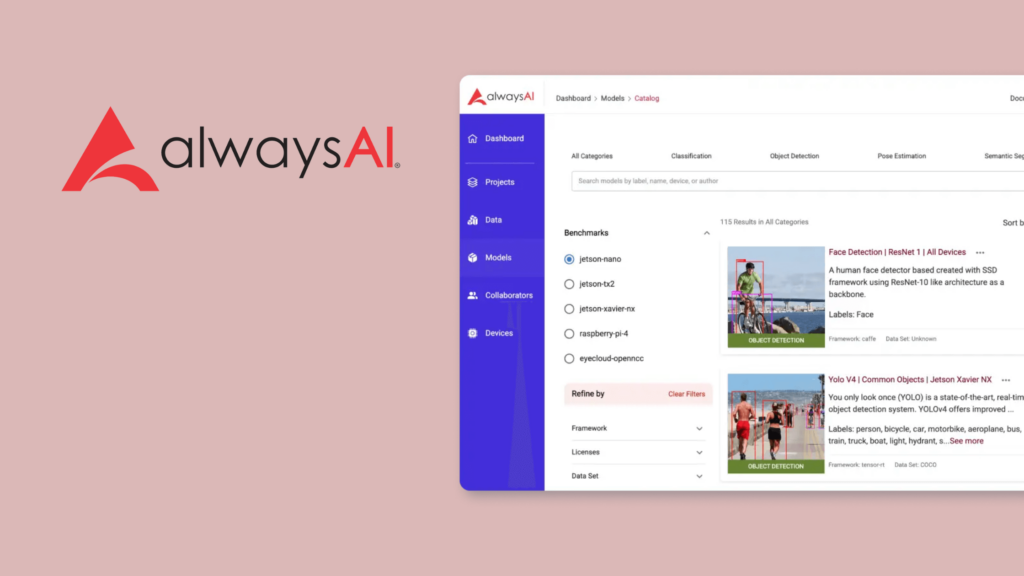
Always AI creates pioneering solutions in a wide variety of industries, including restaurants, retail, mining, and construction. Their AI software uses cameras to identify risks, safety issues, and potential liabilities on construction sites, making projects safer.
AlwaysAI Smart Construction uses existing cameras to identify workers not wearing appropriate PPE, monitor entry gates and other site access points, provide information about site occupancy numbers, and track project progress, including machine idle time. All data is updated in real-time and accessible through the SmartAI software, allowing users to manage projects quickly and efficiently.
Dusty Robotics
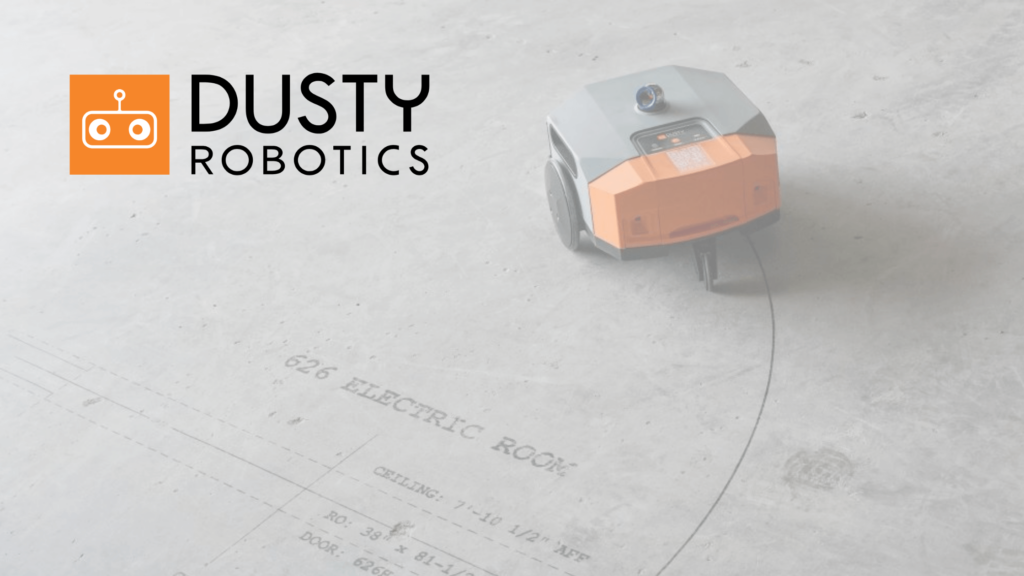
This aptly named company leverages AI and robotics to help create multi-trade design layouts for build sites. Its AI platform reduces total layout time, shortens traditional building methods by 60%, and does everything with 95% precision.
The Dusty Robotics device maps looks like a miniature Zamboni and traverses job sites and building interiors to create accurate layouts. It can map up to 15,000 square feet daily with a single operator up to 1/16” accuracy. The AI-powered model shortens design time, eliminates errors and inaccuracies, and provides tailored layouts for each trade, virtually eliminating accidents due to inaccurate plans.
Using futuristic tech to make job sites safer today
Finding innovative ways to apply AI-powered technology allows companies to make projects run more efficiently while also protecting workers. Artificial intelligence can identify hazards, recognize potential accidents, and ensure proper safety protocols are followed, making it one of the most valuable tools on any job site.