The demand for quicker project completions has never been greater, and for builders and contractors facing the persistent challenge of extended building cycles, time is money. Adopting practical strategies such as leveraging technology, identifying bottlenecks, and improving communication can streamline workflows, cut costs, and maximize efficiency on every build.
Quick look
- Reducing cycle time in construction maximizes efficiency, cuts costs, and ensures quicker project turnarounds, keeping clients satisfied and resources ready for new builds.
- Identifying bottlenecks, capping non-essential changes, and focusing on critical tasks keep projects on schedule and prevent costly setbacks.
- Tools like project management software and prefabricated components reduce build times, enhance collaboration, and help avoid delays.
- Clear, continuous communication minimizes mistakes and keeps everyone aligned, reducing rework and maintaining project momentum.
Cycle times in construction
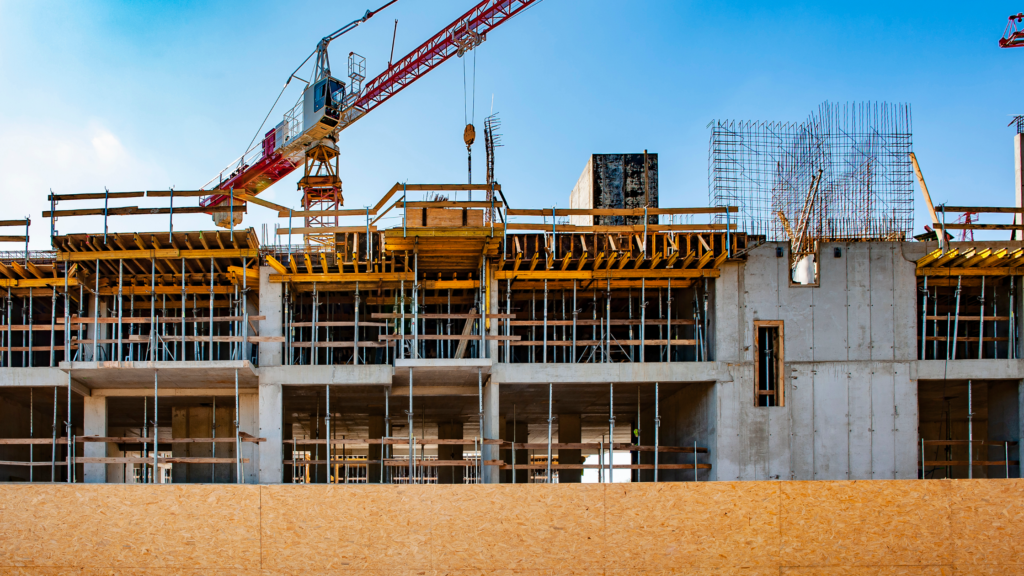
Cycle time in construction is the time it takes to complete a project from start to finish. Think of it as the stopwatch that starts when you break ground and doesn’t stop until the final walkthrough. Keeping this time as short as possible is critical to staying on budget, keeping clients happy, and keeping resources available for the next project.
Before the pandemic, builders had a good handle on cycle times, and many expected things to return to “normal” once restrictions eased. However, supply chain issues, labor shortages, and rising material costs have kept those cycle times stretched longer than anticipated. According to recent industry data, average cycle times are still higher than pre-2020 levels, making efficiency more important than ever. For builders today, finding ways to cut cycle times isn’t just a bonus—it’s essential to staying competitive.
Cycle-time reducing principles
1. Cap changes
Keeping changes to a minimum is one of the most effective ways to reduce cycle time. Each time a change is introduced—whether a design tweak or a material adjustment—it can cause a ripple effect, impacting schedules, costs, and even team availability. By setting clear plans at the start and sticking to them, you help your team stay focused, avoid disruptions, and keep things moving. When changes are necessary, capping them to only the most essential ones keeps the project on track and minimizes wasted time.
2. Identify bottlenecks
Bottlenecks are those pesky points where work slows down, whether waiting on materials, dealing with subcontractor delays, or tackling unexpected site issues. Common bottlenecks in construction include supply chain delays, permit holdups, and labor shortages. Addressing these early is crucial. A good strategy is to map out each project phase and pinpoint where delays are most likely. Regular check-ins with your team can also help spot bottlenecks before they become full-blown delays, allowing you to tackle issues head-on and keep workflows smooth.
3. Avoid non-critical tasks in the construction schedule
Focusing on what truly matters is a game-changer for cycle times. Non-critical tasks, while sometimes helpful, can bog down schedules when time is tight. By honing in on essential tasks, you ensure that your team’s energy and resources go toward activities directly impacting project completion. This approach keeps things moving and reduces the risk of unnecessary work dragging down your schedule. Prioritizing the critical path—the tasks that must be done on time to keep the whole project on schedule—helps keep the project streamlined and efficient.
4. Reap the benefits of technology
Technology has transformed construction in recent years, making planning, monitoring, and real-time adjusting projects more manageable. Tools like project management software, modular building methods, and prefabricated components can dramatically reduce build times. For instance, project management software keeps everyone on the same page, tracking schedules and milestones in one central location. Prefab solutions allow large portions of a project to be completed offsite and quickly assembled onsite, saving time and reducing weather-related delays. Embracing these technologies can greatly affect how efficiently you complete projects.
5. Create continuous workflows
Continuous workflows help keep the momentum going from start to finish. Methods like just-in-time delivery, where materials arrive when needed, help eliminate downtime caused by waiting on supplies. Overlapping tasks, when feasible, also helps maximize productivity by allowing teams to start on one phase while another is still being completed. These approaches reduce “dead time” and keep work moving, helping you finish projects faster. When workflows are seamless, projects move smoothly, creating a win-win for everyone involved.
Communication mitigates mistakes
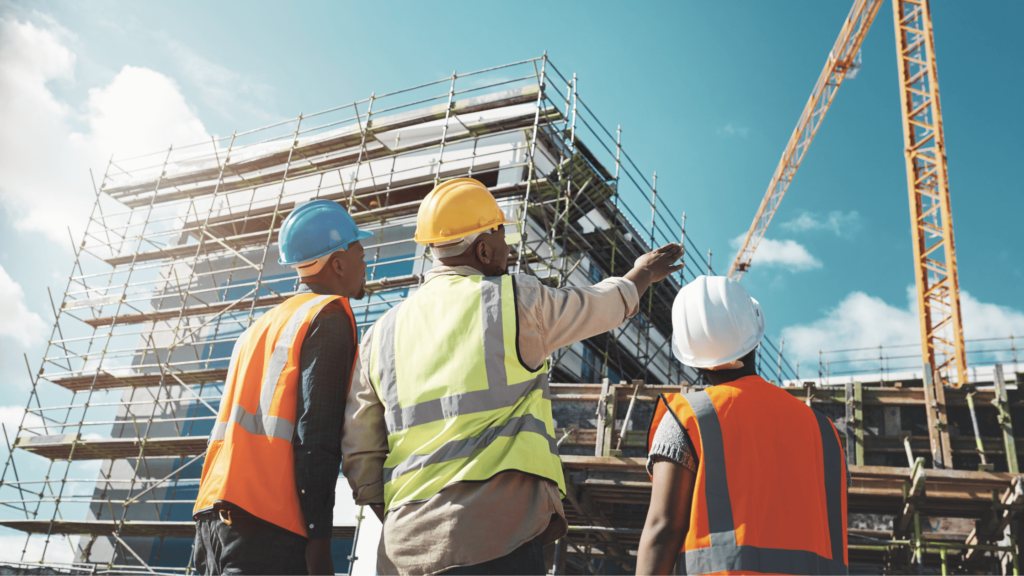
In construction, clear communication is often the difference between a smooth project and one riddled with setbacks. Communication keeps everyone aligned on goals, timelines, and responsibilities from the planning stages to the final walkthrough. A study by PlanGrid and FMI revealed that poor communication and project data account for 48% of all rework on U.S. construction job sites, leading to substantial financial losses. By enhancing communication among team members and stakeholders, construction firms can minimize errors, decrease rework, and improve overall project efficiency.
Effective communication means that each team knows exactly what’s expected and when, reducing the risk of overlapping work or missed steps. Regular updates, clear documentation, and quick responses to questions or concerns help keep things moving forward without hiccups. This transparency ensures that potential issues are flagged and addressed before they snowball, helping everyone work more efficiently.
When communication is strong, misunderstandings that lead to errors are minimized, reducing rework and keeping the project timeline intact. It’s no wonder that communication is often seen as one of the most critical tools for project success in construction.
Why reducing cycle time matters
Reducing cycle time in construction is more than just working faster—it’s about creating a host of benefits that make projects smoother, more profitable, and more satisfying for everyone involved. Here’s how trimming down your build times can positively impact your projects:
- Cost savings: Every delay costs money, whether labor, materials, or equipment rentals. Fewer delays mean fewer expenses, keeping projects within budget and freeing up funds for other needs.
- Efficiency: Faster cycle times help teams stay productive, freeing them up to take on more projects. When things move steadily, everyone is more focused and efficient, driving productivity up and keeping projects on track.
- Improved cash flow: The quicker a project wraps, the quicker the payments. Completing projects on or ahead of schedule helps maintain a healthy cash flow, which is essential for any construction business’s financial stability.
- Client satisfaction: Shorter timelines are always a win for clients who can enjoy or use the completed space sooner. Meeting or beating timelines also builds trust and rapport, increasing the likelihood of repeat business or referrals.
Competitive advantage
Companies that can consistently complete projects faster gain a strong reputation in the industry. Reliability and efficiency set these companies apart, helping them attract new clients and stand out from competitors. In a field where clients often choose based on experience and past success, a reputation for timely, efficient work is a powerful advantage.
Enhanced workforce morale
Shorter cycle times can significantly impact the team’s motivation and job satisfaction. Long, drawn-out projects often lead to burnout and fatigue. By streamlining timelines, workers avoid staying on one project for too long, which keeps morale high and everyone more engaged. Happier teams are often more productive teams.
Reduced risk of market changes
The construction market is often unpredictable, with fluctuating prices, labor availability, and regulatory requirements. Completing projects faster helps reduce exposure to these potential risks, protecting your budget and timeline from unexpected increases in material costs or changes in compliance regulations. In short, the quicker you finish, the less you’re affected by market shifts.
Better resource allocation
When projects wrap up quickly, resources like personnel, equipment, and materials are freed up sooner. This allows companies to reallocate them to new projects, maximizing productivity and preventing resources from sitting idle. Effective resource management translates to more completed projects and greater profitability.
Positive environmental impact
Streamlined construction processes are often more environmentally friendly. Reducing cycle times can lower energy use and minimize waste, as there are fewer delays, less equipment idling, and more efficient use of materials. By adopting practices that reduce cycle time, companies can support sustainability and reduce the environmental impact of their projects.
Reducing cycle time isn’t just a nice-to-have—it’s a smart business move that benefits everyone, from the workforce to clients to the environment.
Bottom line
Reducing cycle time in construction isn’t just about speeding things up—it’s a strategic move that leads to significant cost savings, greater efficiency, and better overall project outcomes. Builders can keep projects on track and clients satisfied by capping unnecessary changes, addressing bottlenecks, leveraging technology, and prioritizing strong communication.
Embracing a more efficient approach benefits everyone involved—from the crew to the client—and keeps your business competitive in an evolving industry.
Want to learn more? Subscribe to our weekly newsletter!