Roofers face some of the most dangerous jobs across the construction industry. Injury and fatality statistics continue to climb, making OSHA violations common across many job sites. It’s an employer’s responsibility to establish a stronger safety culture, and identifying hazards, secure ladder usage, roof inspections, and fall protection plans also make a world of difference.
An overview of falls
The construction industry is one of the most dangerous, and the roofing sector, in particular, has one of the highest rates of injury and fatality. According to roofingcontractor.com, roofing is one of the three deadliest of all civilian occupations, with the fatality total climbing to 124 in 2022. Of these 124 deaths, 80.6% were due to a fall, trip, or slip.
While there is no singular reason why falls in construction happen or how to prevent them entirely, a few common causes continuously repeat themselves. Lack of experience, improper equipment, and failure to complete a safety inspection are common factors that lead to accidents. OSHA reports that failure to use fall protection equipment properly is one of the most common citations year after year.
Some workers will naturally be more risk-averse, but by fostering a culture with more stringent safety protocols, we can prevent injuries and fatalities.
The role of employers
Workers are responsible for following safety protocols and protecting themselves, but these protocols trickle down, ultimately, from the companies themselves. The employers have a responsibility to:
- Institute a housekeeping program to lessen the risk of falls, slips, and trips
- Routinely identify and control fall hazards on site
- Installing fall protection measures like proper guard rails
- Provide the correct PPE to roofers working at heights
Employers are also responsible for eliminating language barriers on site and ensuring every employee receives the same accessible, thorough training. Signage, training, and a written fall protection plan must be provided in a language employees understand.
6 ways to prevent roofing falls
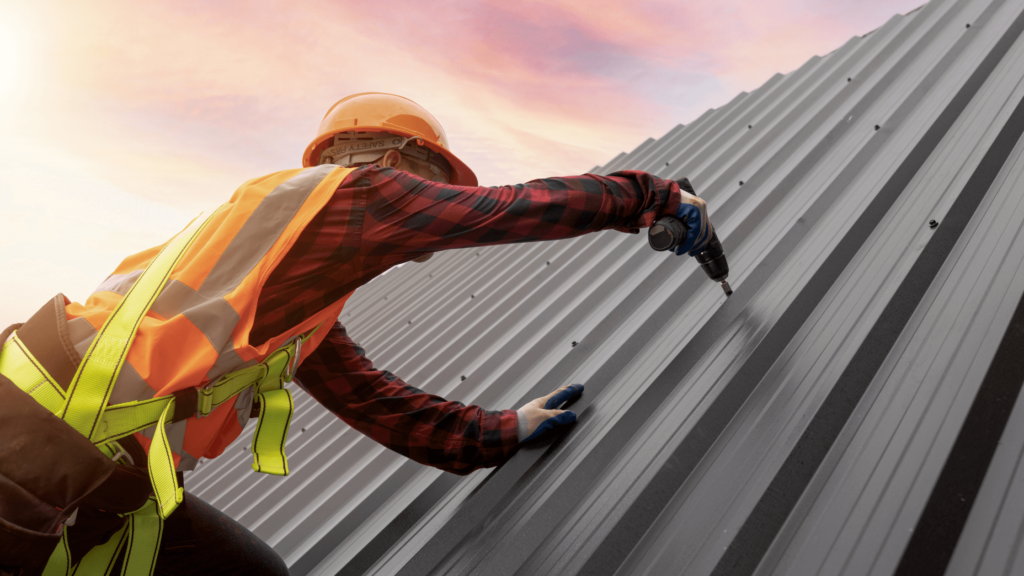
1. Identify hazards
Before any roofing work can begin, employers should conduct a formal assessment to identify fall hazards workers may face. This includes climbing on ladders, working on rooftops, and standing on scaffolding.
Once hazards have been identified, the risk assessment will determine the severity of each risk. When working on rooftops, the evaluation must include access hatches and skylights, which pose additional risks and require separate safety measures. Small platforms, such as balconies and uneven elevations, will also need their own types of equipment and protection.
2. Safety training
Safely executed work starts with thorough safety training. Everyone can prevent falls, slips, and trips, not just while working at heights. Knowing how to examine, install, and troubleshoot fall arrest PPE and its misuse is crucial for preventing injury.
The roofers’ fall-protection training program should be reviewed and modified regularly to ensure it’s current with the latest technology being used on site. It should reflect new, modern hazards that workers will likely face and incorporate real demonstrations and active teaching of the equipment used.
Even if PPE in the work environment remains the same, holding regular refreshers for employees will help everyone keep safety top of mind, and remember what they need to do to prevent injuries at work.
3. Secure ladder use
Installing a ladder might be a part of the workday that roofers do quickly and haphazardly, as it’s routine. However, ensuring proper laddy safety is crucial for preventing workplace injuries.
Begin by conducting a risk assessment before using the ladder. Assess the condition of the ladder, noting any damage or defects. Then, confirm the ladder is a suitable height for the job. Always place the ladder on an even surface to maximize stability.
Before climbing, inspect the rungs and side rails for debris or slippery surfaces. To prevent shifting, the ladder must also be secured and tied off at the top and bottom. Always ensure three points of contact while ascending the ladder, whether two hands and one foot or two feet and one hand. Also, avoid twisting or overarching movements.
The ladder must always extend 3 feet above the access point to ensure a safe transition onto the roof. Workers can use ladder stabilizers to further prevent shifts or sliding.
4. Fall protection plan
Workers need safety harnesses as part of a proper fall protection plan when working on roofs. This is essential for preventing fall mistakes and minimizing the risk of serious injury or fatality.
Fall protection plans may vary depending on the role but should generally contain the following:
- Hazard inspection and identification
- Applicable fall protection mechanisms
- Emergency procedures
- Compliance documentation
- Equipment inspection protocols
- Guard rail installation guides
- Inspection notes
5. Roof inspections
Before workers commence work, the roof should be inspected regularly to identify potential hazards or damage. A proper roof inspection ensures safety compliance and is crucial to maintaining an overall safe environment. An appropriate inspection of the roof should involve the following:
- A routine check by qualified personnel to thoroughly assess the condition of the roof and address any issues
- Keeping thorough records of previous inspections and repairs to track the condition of the roof over time
- Utilizing proper and current technology like infrared imaging and drones to detect damages or vulnerabilities in the work area
By implementing these measures, companies can lessen risks of injury or fatality before they happen.
6. Guard rail use
Often an afterthought on roofing sites, installing guardrails is essential for preventing falls and injuries on the job site. Guardrails create an effective physical barrier that prevents workers from accidentally stepping off the edge. Safety nets and personal fall arrest systems are great alternative solutions, but they may not offer the same level of continuous protection.
Guardrails provide a constant visible barrier that helps improve safety, especially while working near the roof’s edge. They’re also easy to install and require minimal maintenance. When installed in place, they provide a reliable method of fall protection without the need for significant adjustments or extensive training.
Guard rails are also cost-effective. While safety is most improved when multiple fall protection precautions are in place, guard rails are a simple, accessible bare minimum that most sites could implement immediately.
Bottom line
Roofing falls are preventable, and proper fall prevention starts with the employer and the roofer fostering a safer environment. By identifying hazards, implementing a thorough fall protection plan, and conducting proper safety training, your crew will be well on its way to improving injury and fatality statistics.
For more on the best safety measures and tips, subscribe to our weekly newsletter.